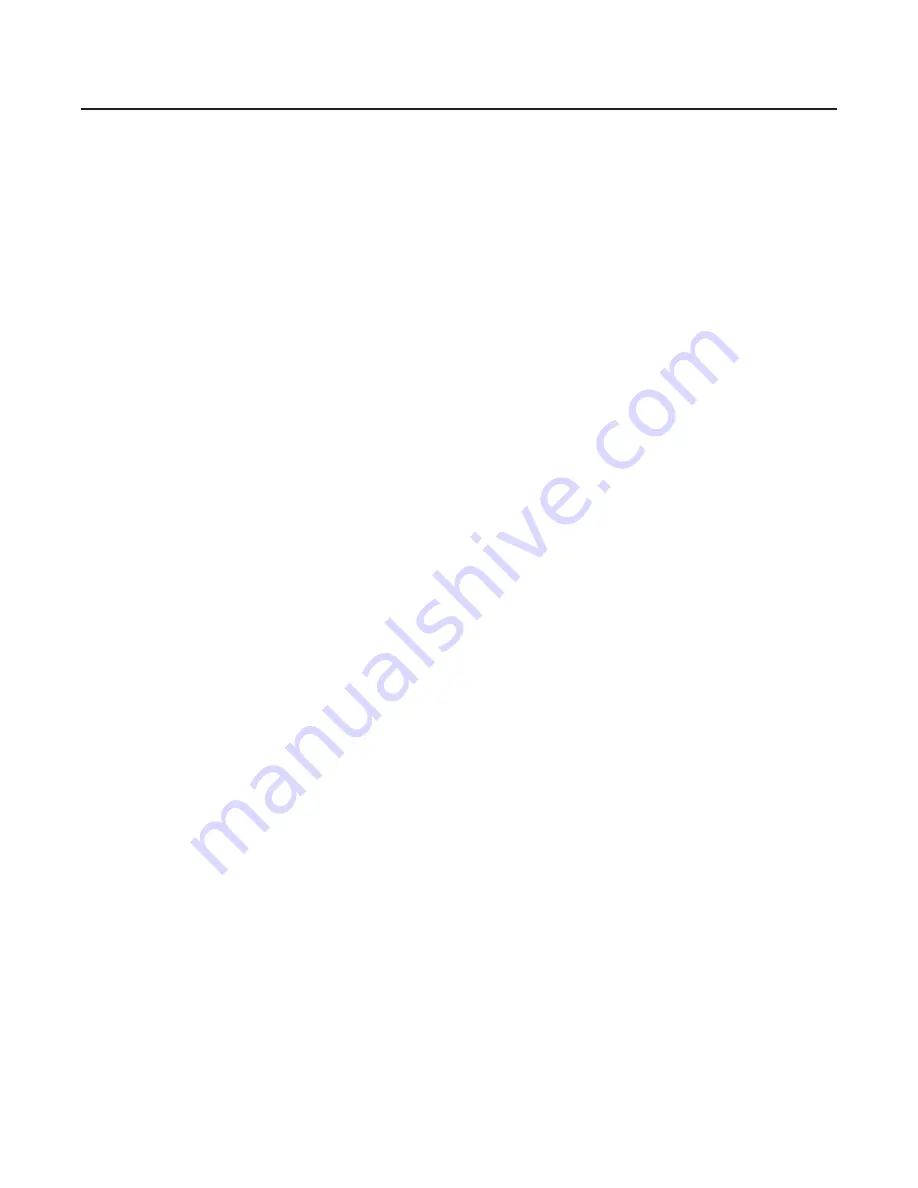
11
Diaphragm
Performance
and
Durability
Steamix
203
operates
on
a
pressure
actuated
diaphragm
principle
as
discussed
on
page
5
of
this
manual.
A
specially
designed
double-coated
elastomer,
high
performance
diaphragm
has
been
custom
designed
for
this
application
based
upon
extensive
research
and
laboratory
and
field-testing.
Diaphragm
Service
Life
A
chronological
operational
service
life
of
a
diaphragm
is
virtually
impossible
to
specify
due
to
the
wide
diversity
of
field
application,
inlet
steam
and
water
pressure
and
outlet
flow
temperature
which
Steamix
experiences.
Steamix
diaphragms
are
continuously
cycle
tested
at
our
state
of
the
art
test
facility
in
Three
Rivers,
MI
and
the
diaphragms
must
be
able
to
exceed
50,000
field
simulated
operational
cycles
at
the
maximum
steam
pressure
rating
of
150
psi.
In
real
terms
that
equates
to
approximately
50
wash
down
cycles
every
day
for
three
years.
Some
diaphragms
last
longer
(we
have
on
record
installations
still
fully
operational
at
12
years
and
counting),
some
do
not
last
as
long,
which
is
why
we
offer
a
full
replacement
two-year
warranty.
Safety
A
diaphragm
is
a
mechanical
component
in
a
mechanically
operated
product.
All
mechanical
products
have
the
potential
to
fail
at
some
point
in
their
service
life.
Steamix
is
the
only
product
supplied
for
this
application,
which
we
are
aware,
that
will
fail
to
cold
water
flow
in
the
event
that
its
primary
operating
component
(diaphragm)
experiences
failure.
Tips
for
Ensuring
Long
Diaphragm
Service
Life
1.
Cool
Down:
Do
not
use
a
spray
nozzle
as
a
long-term
flow
control
device.
Turn
the
Steamix
off
at
its
inlet
flow
control
when
it
is
not
in
use
and
let
the
valve
cool.
Itís
good
for
the
nozzle,
itís
good
for
the
hose,
itís
good
for
the
diaphragm.
2.
Steam
Quality:
Maintain
your
steam
system
efficiently
and
watch
the
condensate
chemistry.
Highly
acidic
carbonic
acid
is
not
good
anywhere
in
the
system
and
the
diaphragm
is
no
different.
3.
Trap:
Trap
the
steam
line
feeding
the
Steamix
effectively.
Compounding
large
quantities
of
acidic
condensate
with
water
hammer
and
pressure
shocks
can
cause
all
sorts
of
problems
and
again
the
diaphragm
can
suffer.
By
maintaining
a
reasonable
distance
(we
suggest
6
feet)
between
the
steam
trap
and
Steamix,
the
cooled
condensate
in
the
pipework
between
the
steam
trap
and
Steamix
will
assist
with
Tip
#1.
4.
Back
Pressure:
Keep
an
eye
on
the
pressure
loss
ratio
discussed
on
page
12
of
this
Product
Manual.
High
back
pressures
combined
with
diverse
inlet
pressures
make
the
Steamix
work
extra
hard
and
additional
stress
is
placed
upon
the
diaphragm.
5.
Keep
it
Low:
Steamix
is
rated
for
use
with
up
to
150
psi
steam.
However,
the
outlet
flow
rate
and
temperature
rise
does
not
improve
dramatically
beyond
100
psi
steam.
In
other
words,
we
do
not
need
steam
pressures
higher
than
100
psi
for
effective,
high
temperature
washdown.
When
possible,
lower
the
inlet
steam
pressure
to
100
psi
or
below.
Tests
have
shown
us
that
the
extra
30
degrees
or
so
which
150
psi
steam
gives
you
can
really
intensify
temperature
related
fatigue
on
the
diaphragm
and
seals
within
Steamix.
Optimum
performance
pressures
are
noted
on
Page
6
of
this
manual.