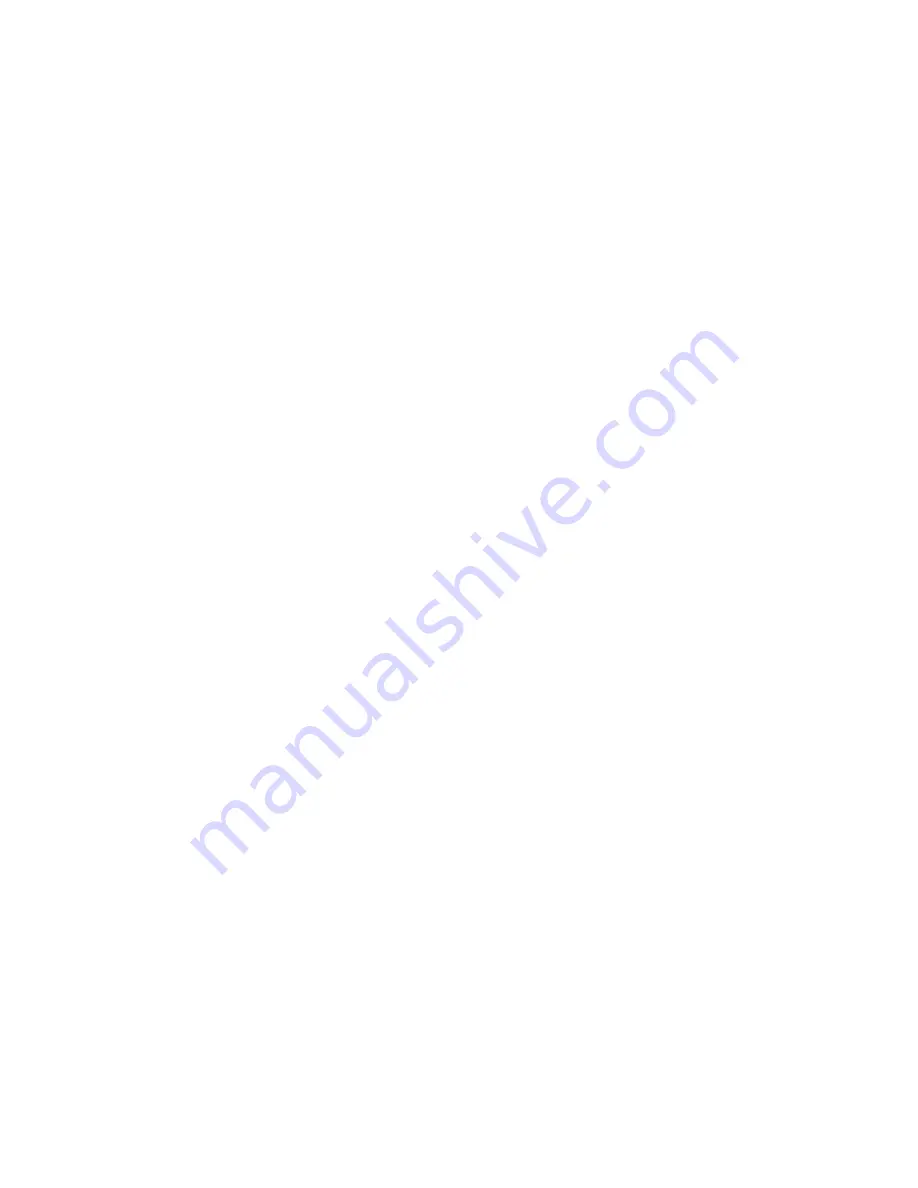
Manufacturer:
Merloni TermoSanitari SpA - Italy
Commercial subsidiary: MTS (GB) LIMITED
MTS Building
Hughenden Avenue
High Wycombe
Bucks HP13 5FT
Telephone: (01494) 755600
Fax: (01494) 459775
Internet: http://www.mtsgb.ltd.uk
E-mail: [email protected]
Technical Service Hot Line: (01494) 539579
Summary of Contents for eco Genius 24MFFI
Page 33: ...9 FIG 1 26 FIG 1 27 Q...
Page 42: ...18 W1 FIG 1 72 FIG 1 73 W1 W1 W1...
Page 50: ...26 ecoGENUS 24 MFFI ecoGENUS 24 RFFI...
Page 55: ...31...