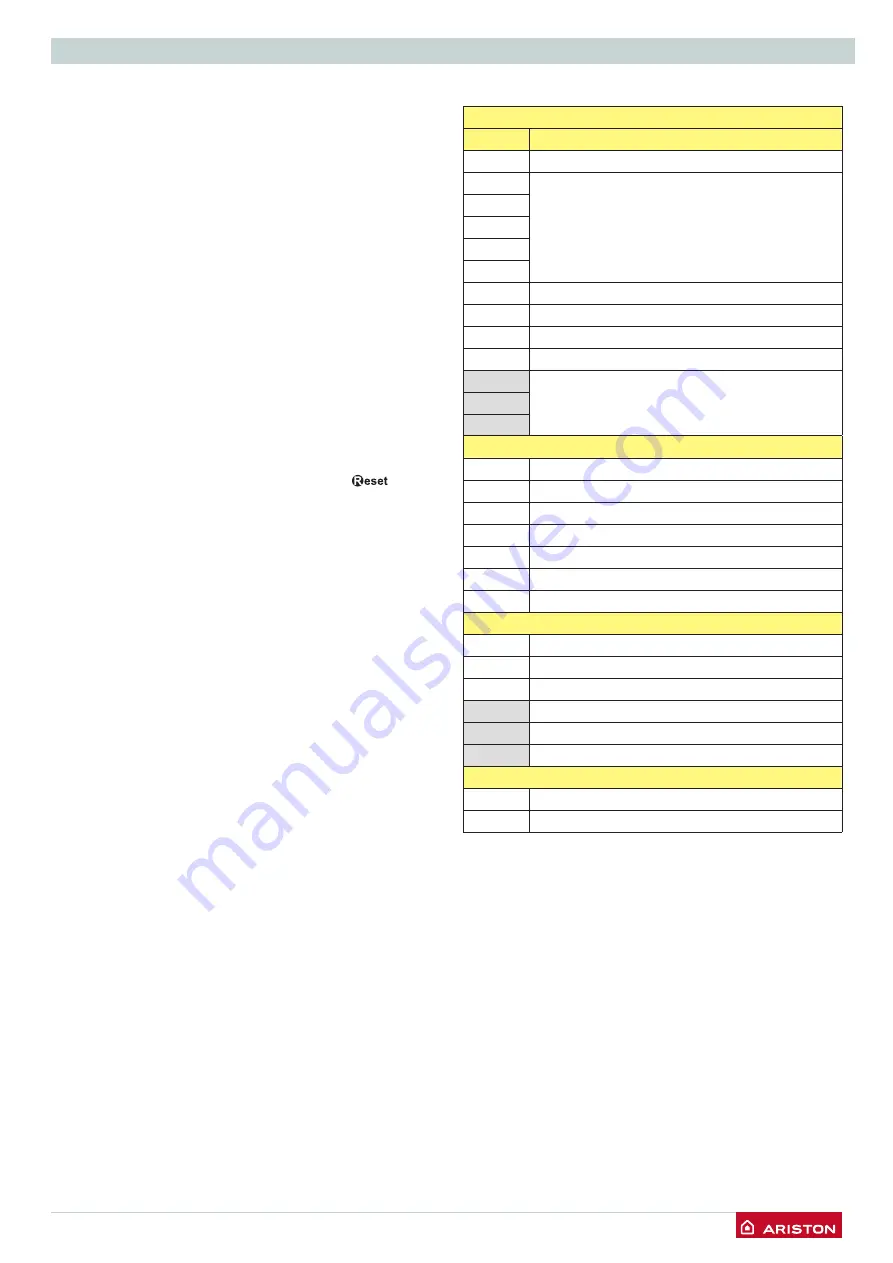
/
35
BOILER PROTECTION DEVICES
Boiler protection devices
The boiler is protected from malfunctioning by means of internal
checks performed by the P.C.B., which stops the boiler from
operating if necessary.
In the event of the boiler being shut off in this manner, a code
appears on the display which refers to the type of shut-off and the
reason behind it.
There are two types of shut-off:
Safety shut-off
This type of error is “volatile”, which means that the boiler starts
up again automatically as soon as the problem which caused the
shut-off is removed; the error is indicated by the «Err» symbol which
appears on the display and the error code.
In fact, as soon as the cause of the shut-off disappears, the boiler
starts up again and continues to operate normally.
While the boiler is shut off for safety reasons it is possible to attempt
to restore normal operation by switching the appliance off and on
again using the on/off button on the control panel.
If after attempting this the boiler still shows a safet shut off, switch it
off and ensure that the external electrical switch is in the off position.
Shutdown
This type of error is “non-volatile”, which means that it is not removed
automatically. To restore normal operation press the
button
on the control panel.
The first figure of the error code (e.g. 1 01) indicates within which
operational assembly the error occurred.
1 - Primary Circuit
3 - Internal Electronic Part
5 - Ignition and Detection
6 - Air inlet - flue gas outlet
Malfunction warning
This warning is shown by the display in the following format:
5 P1 = FIRST IGNITION ATTEMPT UNSUCCESSFUL
the first figure indicating the operational assembly is followed by a P
(warning) and the code relating to the specific warning.
Important
If this shutdown occurs frequently, contact an authorised Technical
Service Centre for assistance. For safety reasons, the boiler will
permit a maximum of 5 resets in 15 minutes (5 presses of the RESET
button); at the 6th attempt within this 15-minute period the boiler
will shut down and may only be operated again after the electricity
supply has been disconnected. If the shutdown is occasional or an
isolated event, this is not a problem.
Anti-frost Device.
The anti-frost function acts on the central heating flow temperature
probe, independently from other regulations, when the electrical
supply is turned on.
If the primary circuit temperature is between 3°C
and 8°C the pump will run until the temperature
reaches > 9°C.
If the flow temperature remains between 3°C and 8°C the pump will
continue to run for a maximum of 20 minutes unless a temperature
above > 9°C is detected in the central heating flow, after this the the
burner will fire (heating position) until a temperature of > 30°C is
detected.
If the central heating flow temperature is < 3°C, the burner will fire
(heating position) at minimum power until the temperature reaches
> 30°C, the burner will go out.
If lockout is caused by overheat the burner will not fire but the pump
will continue to run.
The anti-frost device activates only when (with the boiler operating
correctly):
- the boiler is electrically powered;
- there is a supply of gas.
Central Heating circuit
Display
Description
1 01
Overheat
1 03
Insufficient circulation
1 04
1 05
1 06
1 07
1 10
Flow temp. probe circuit open / short circuit
1 12
Return temp. probe circuit open / short circuit
1 14
External sensor circuit open / short circuit
1 18
Heating delivery probe problem
1 P1
Insufficient circulation indication
1 P2
1 P3
Internal P.C.B.’s
3 01
EEPROM error
3 02
Comunication error
3 03
Main P.C.B. error
3 04
Too many (> 5) resets in 15 minutes
3 05
Main P.C.B. error
3 06
Main P.C.B. error
3 07
Main P.C.B. error
Ignition and Detection
5 01
No flame detected
5 02
Flame detected with gas valve closed
5 04
Flame lift
5 P1
1st Ignition Failed
5 P2
2nd Ignition Failed
5 P3
Flame cut-off
Air Inlet / Flue gas outlet
6 04
Insufficient fan speed
6 10
Thermofuse open
Table summarising error codes
Summary of Contents for CLAS HE R
Page 27: ... 27 INSTALLATION Y Plan system utilizing external 2 channel programmer ...
Page 28: ...28 INSTALLATION Y Plan system utilizing integral 2 channel programmer ...
Page 61: ......
Page 62: ......
Page 63: ......