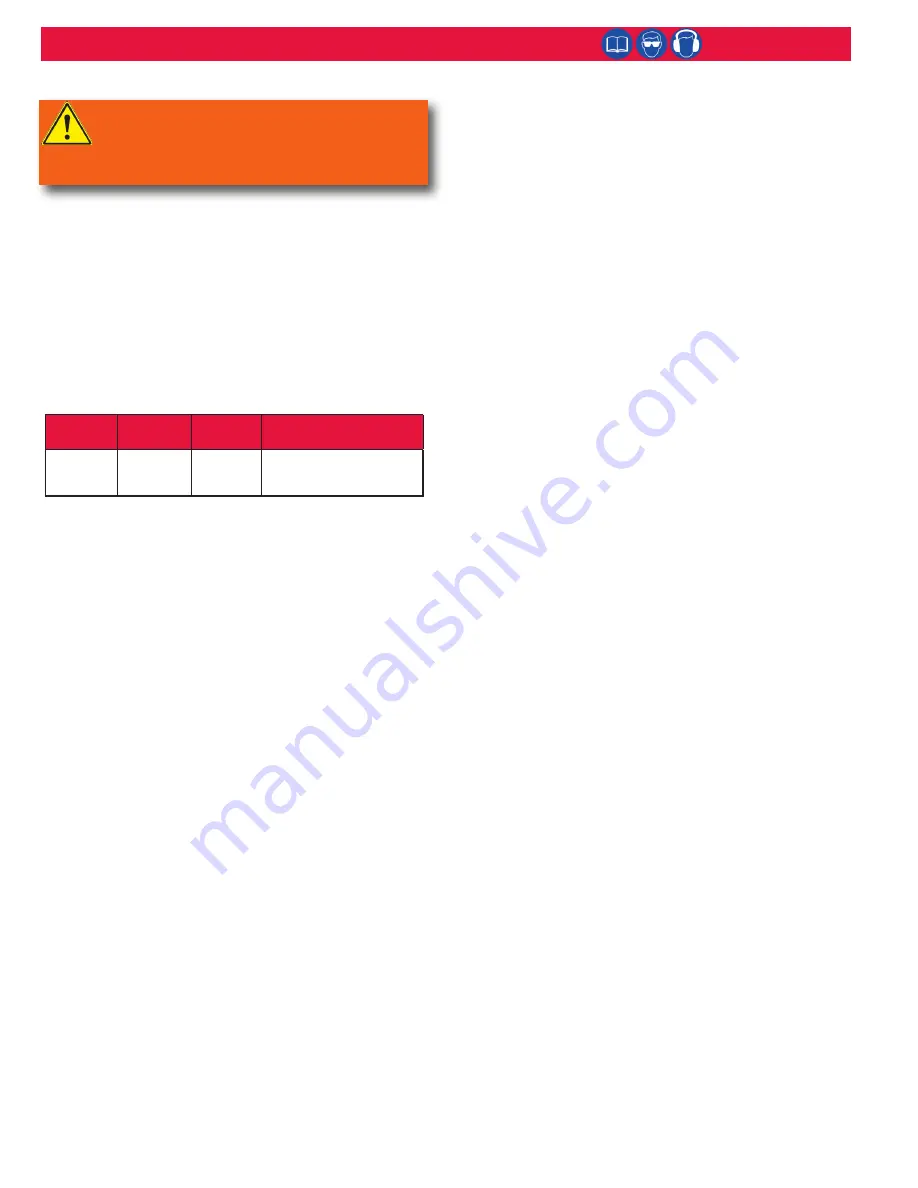
4
913F Powerig® Unit (HK1191)
POWER SOURCE:
Honda 5.5hp, 4-cycle, single-cylinder,
air-cooled gasoline engine - point condenser ignition with 3
amp charging coil.
OUTPUT PRESSURE:
PULL: 5,800 PSI (400 bar), MAX 8,400 psi (580 bar)
RETURN: 2,800 PSI (193 bar), MAX 6,000 psi (413 bar)
PRESSURE SETTING AS SHIPPED:
PULL: 5,400 - 5,700psi (37,200 - 39,300 kPa)
RETURN: 2,200-2,400 psi (15,200-16,500 kPa)
AMBIENT OPERATING TEMPERATURE RANGE:
0° (18°C) to -120° (49°C)
MAXIMUM HYDRAULIC FLUID TEMPERATURE:
150°F
(65°C)
HYDRAULIC FLUID:
Use 32AW (0°F - 70°F ambient),
46AW (30°F - 120°F ambient), or ATF (30°F - 90°F ambient).
ATF
Hydraulic fluid
shall meet DEXRON® III, DEXRON VI,
MERCON, Allison C-4 or equivalent ATF specifications.
Fire resistant fluid may be used if it is an ester based fluid
such as Quintolubric HFD or equivalent. Water based fluid
shall NOT be used as serious damage to equipment will
occur.
ENGINE OIL:
Use 5W30 (0°F - 100°F ambient)
or 10W-30 (20°F - 120°F ambient)
RESERVOIR CAPACITY:
5.0 gallons (19 liters)
FLOW RATE:
400 in
3
/min up to 660 psi
115
in
3
/min above 660 psi
Specifications
The Huck Model 913F Powerig® hydraulic power source is
a portable, gasoline-powered unit designed to operate all
Huck hydraulic installation equipment, excluding Huck-Spin
tools.
Figure 1
shows the construction features of the unit
and identifies its main components. Hydraulic pressure is
developed by a two-stage, gear piston hydraulic pump driven
by a Honda 5.5hp engine. The pump output is directed to
either the PULL or RETURN pressure port of the installation
tool by a four-way directional valve. This valve is controlled
from the tool through a trigger/switch.
This is a 12-volt control system. Internal relief valves are
preset at the factory for the protection of the operator and
the equipment. External relief valves control the PULL and
RETURN pressures.
The factory preset pressure for the:
External Relief Valve = 5400–5700 psi (372–393 bar)
Return Pressure Valve = 2700–3300 psi (186–227 bar)
Pressures can be adjusted to match the Huck installation tool
being used. See the applicable installation tool manual.
Hydraulic fluid is stored in a reservoir which serves as the
base for the motor-pump and directional valve. Hydraulic
quick disconnect couplers are furnished for connecting hoses
to the installation tool and Powerig. This Powerig includes
a roll cage for protection, as well as to facilitate moving the
unit to various work stations. The unit weighs approximately
175 pounds (79.379 kg) when filled with hydraulic fluid.
Description
WARNING: RETURN pressure can be adjusted
to 6000 PSI if required for use with HPT tools
ONLY. DO NOT OPERATE OTHER HUCK TOOLS
AT THIS RETURN PRESSURE. Severe personal
injury and damage to tool may result.
WIDTH
LENGTH HEIGHT
WEIGHT
(without hydraulic fluid)
21.0 in.
(54.7 cm)
24.0 in.
(62.9 cm)
27.0 in.
(69.9 cm)
122.0 lbs.
(54.7 kg)
Troubleshooting
1. With Powerig® unit engine running, tool fails to
operate when trigger is depressed:
a. Loose or damaged control cord or connectors.
b. Loose or faulty hydraulic hose couplings.
c. Defective tool trigger assembly.
d.
Low hydraulic fluid level in reservoir.
e. Contamination in kick-down valve.
f. Broken hydraulic line, possibly under cover plate
g. Worn pump-motor coupling or loose/damaged shaft
extension.
h. Loose or damaged wires or connectors in Powerig
magneto/trigger/solenoid circuits.
i. Worn poppets or seals in directional valve (rebuild
using 129437 kit).
j. Contamination in or defective pilot valve.
k. Defective 130997 electrical assembly (includes resistor
and diodes).
l. Defective magneto stator.
m. Installation tool not functioning.
2. Tool does not return on release of trigger:
a. Loose or faulty hydraulic hose couplings.
b. Defective tool trigger assembly.
c. Contamination in kick-down valve.
d. Contaminated in or defective pilot valve
e. Loose or damaged wires or connectors in Powerig
magneto/trigger/solenoid circuits.
f. Installation tool not functioning.
3.
Pump cavitation (noisy throughout installation cycle):
a.
Low hydraulic fluid level in reservoir.
b. Clogged suction strainer in reservoir.
c.
Hydraulic fluid viscosity too high for ambient
temperature
4. Tool operation is slow but entire cycle does occur:
a. Pump cavitation (see above)
b. Worn poppets or seals in directional valve (rebuild
using 129437 kit).
c.
Worn 508708 valve stem in external relief valve.
d. Low engine shaft speed
e. Worn or defective hydraulic pump
Always check the simplest possible cause of malfunction first. For example, blown fuse, tripped circuit breaker, defective switch or
control cord. Eliminate each possible cause until the defective circuit or part is located. Where possible, substitute known good parts
for suspected bad parts. A qualified electrician should check out the electrical system. Use this section as an aid in locating trouble
and correcting it.