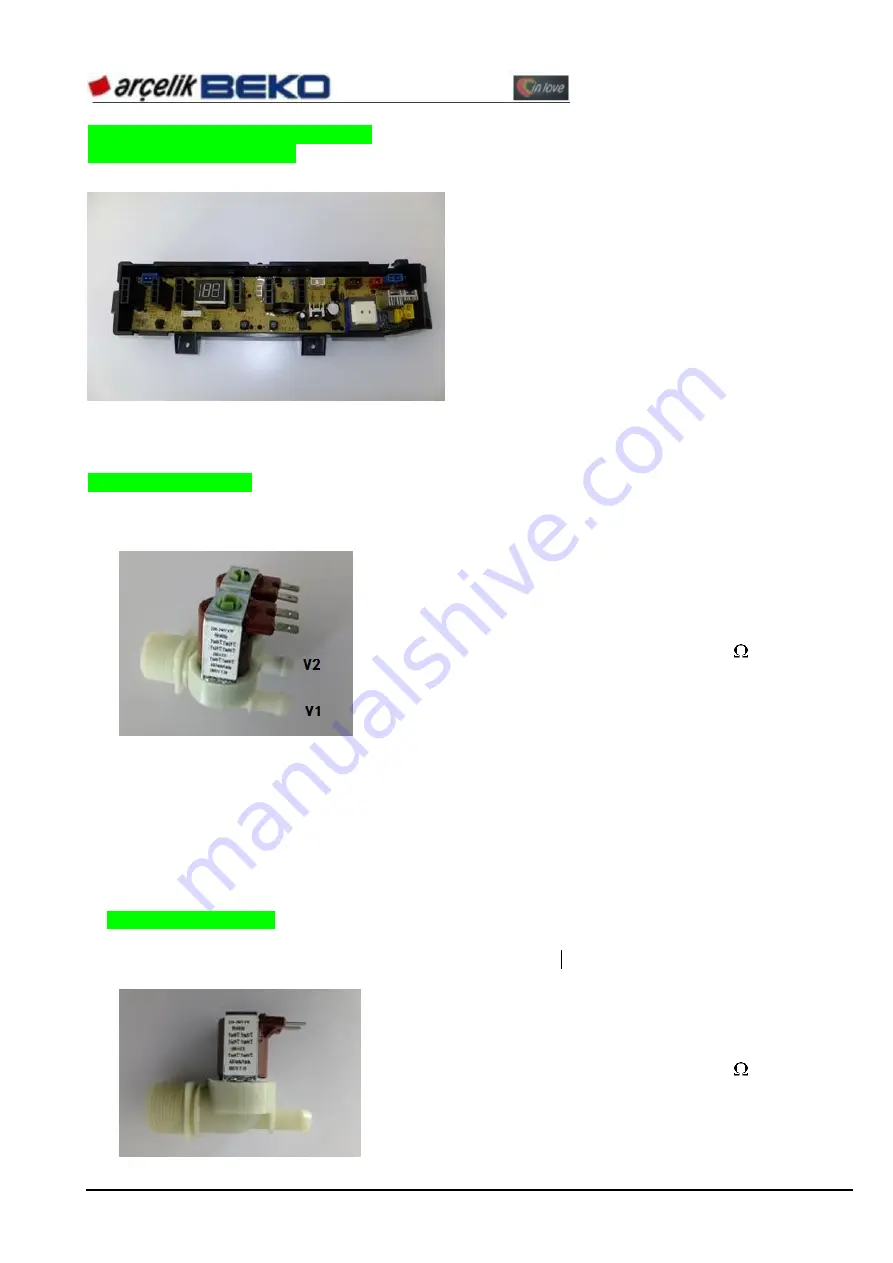
RETRO WASHING MACHINE
45
9. Component Operation Principles
9.1. Electronic Card Group
9.2. Water inlet Valve
It is used to take water inside the machine at the desired amounts when necessary.
• 2-valve for the models with single water inlet and softener.
Valves are related with the triacs which are located on the electronic card.
Both valves are released at the same time in the softener. Water is come into softener
compartment of the detergent box.
9.3. Single inlet Valve
It provides water to the steam generator for steam application.
Electronic card group is composed of main
board, card holder parts.
There are tack switch used for program
selection the main board.
Wash programs, wash and spin engine
profiles which are written on the
microprocessor built onto the main board
and components (motor, pump, valves,
safety switch, pressure sensor, spin time
/temperature selection) are controlled
Picture 9.1 Electronic card group
Operating Voltage
: 220 / 240VAC 50-60 Hz
Rated Power
: 5-8 W
Flow (V1)
: 15.5 l/min
Flow (V2)
: 5 l/min
Operating Temperatures : T85°C
Coil Resistance
: 3375 - 4125
Picture 9.2 Water Intake valve
Operating Voltage
: 220 / 240VAC 50-60 Hz
Rated Power
: 5-8 W
Flow (V1)
: 15.5 l/min
Operating Temperatures : T85°C
Coil Resistance
: 3375 - 4125
Picture 9.3 Single inlet valve
Summary of Contents for BEKO RETRO
Page 42: ...RETRO WASHING MACHINE 42 8 General Operation Principle 8 1 Water Intake Profile 1 20 N 2 3 N 0...
Page 54: ...RETRO WASHING MACHINE 54...
Page 57: ...RETRO WASHING MACHINE 57 12 2 Machine does not start...
Page 61: ...RETRO WASHING MACHINE 61 12 3 3 E3...
Page 68: ...RETRO WASHING MACHINE 68...
Page 88: ...RETRO WASHING MACHINE 88...
Page 90: ...RETRO WASHING MACHINE 90 15 2 Control Group...
Page 91: ...RETRO WASHING MACHINE 91 15 3 Water System Group...
Page 92: ...RETRO WASHING MACHINE 92 15 4 Lid Group...
Page 93: ...RETRO WASHING MACHINE 93 15 5 Body Group...
Page 94: ...RETRO WASHING MACHINE 94 15 6 Top Cover Group...
Page 95: ...RETRO WASHING MACHINE 95 16 List of Components SAP must be referred for the part list...