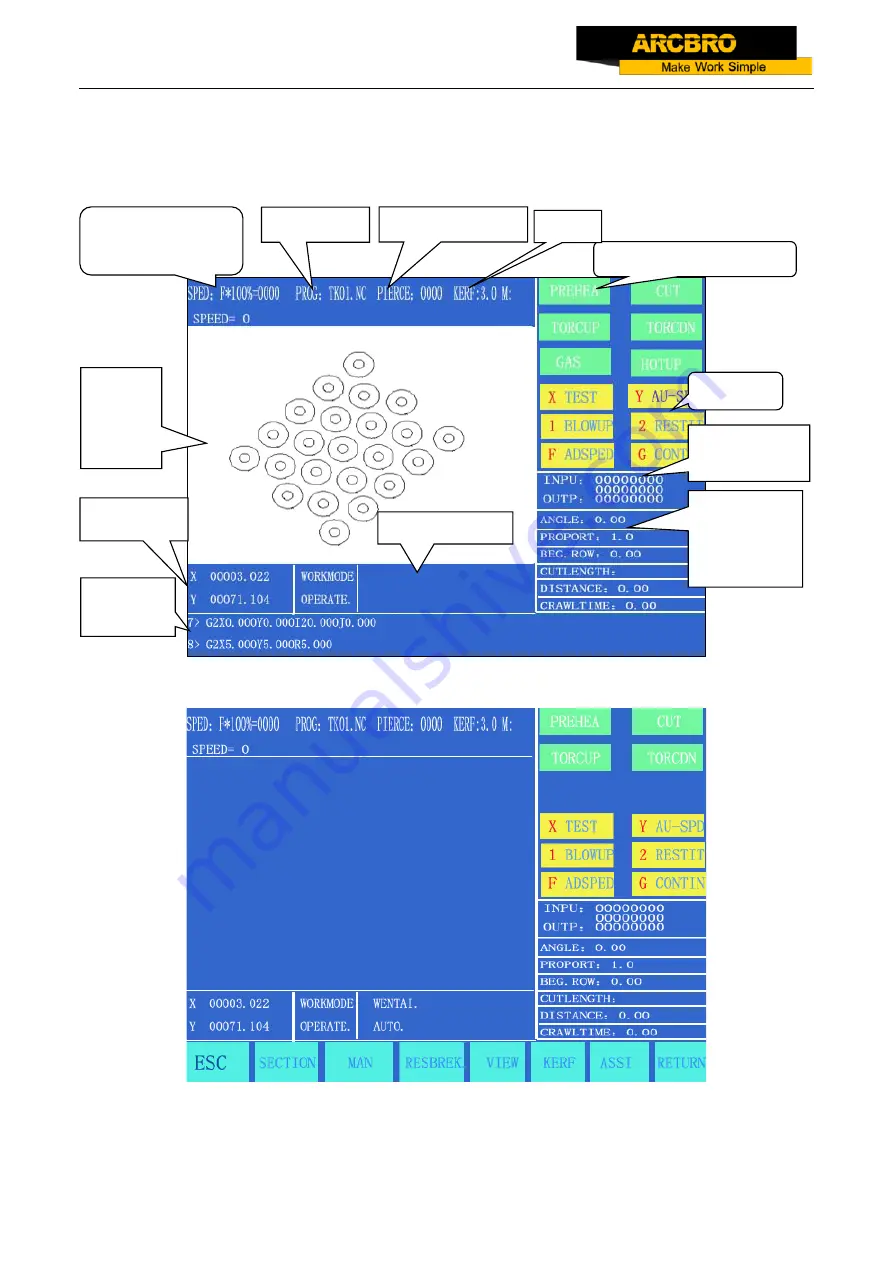
Service Support Spirit
26
Unique Solution
WWW.ARCBRO.COM
8. Automatic Function(AUTO)
In the main menu, press [F1] to enter the automatic function window, as shown in the figure below.
Flame mode
Fig. 8.1 Automatic Function (AUTO) Window
Plasma Mode
Active speed
multiplying factor
Program
Heavy-current control
Piercing Hole
Kerf
Input/output
indication
Function
Coordinate
Pattern
Display
Space
Machining
parameter
indication
Work mode
Machining
Program