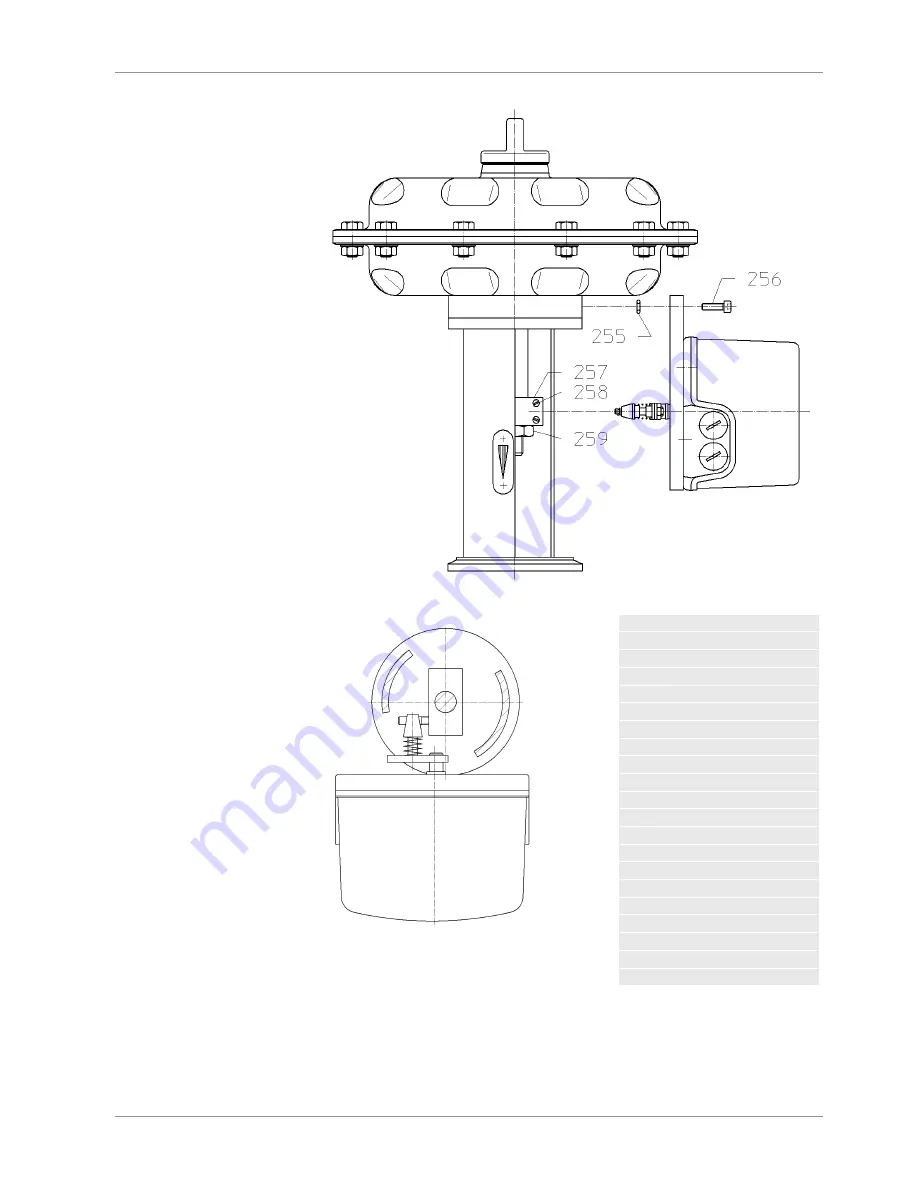
ARCA Regler GmbH
9 Installation
Series 824
27 / 46
09.2018 / 1.0
Illustration 10:
Assembly 824/813 side view
211
Pivot lever
212
Spring lock washer
213
Hex screw
214
Hex nut
216
Hex nut
217
Washer
218
Sliding washer
219
Spring
220
Conical roller
221
Circlip
222
Stroke setting screw
250
Adapter plate
251
Cylinder head bolt
252
Adapter
253
Grub screw
254
O-ring
255
O-ring
256
Cylinder head bolt
257
Bracket
258
Stroke driving pin
259
Hex nut
Illustration 11:
Installation 824/813 top view