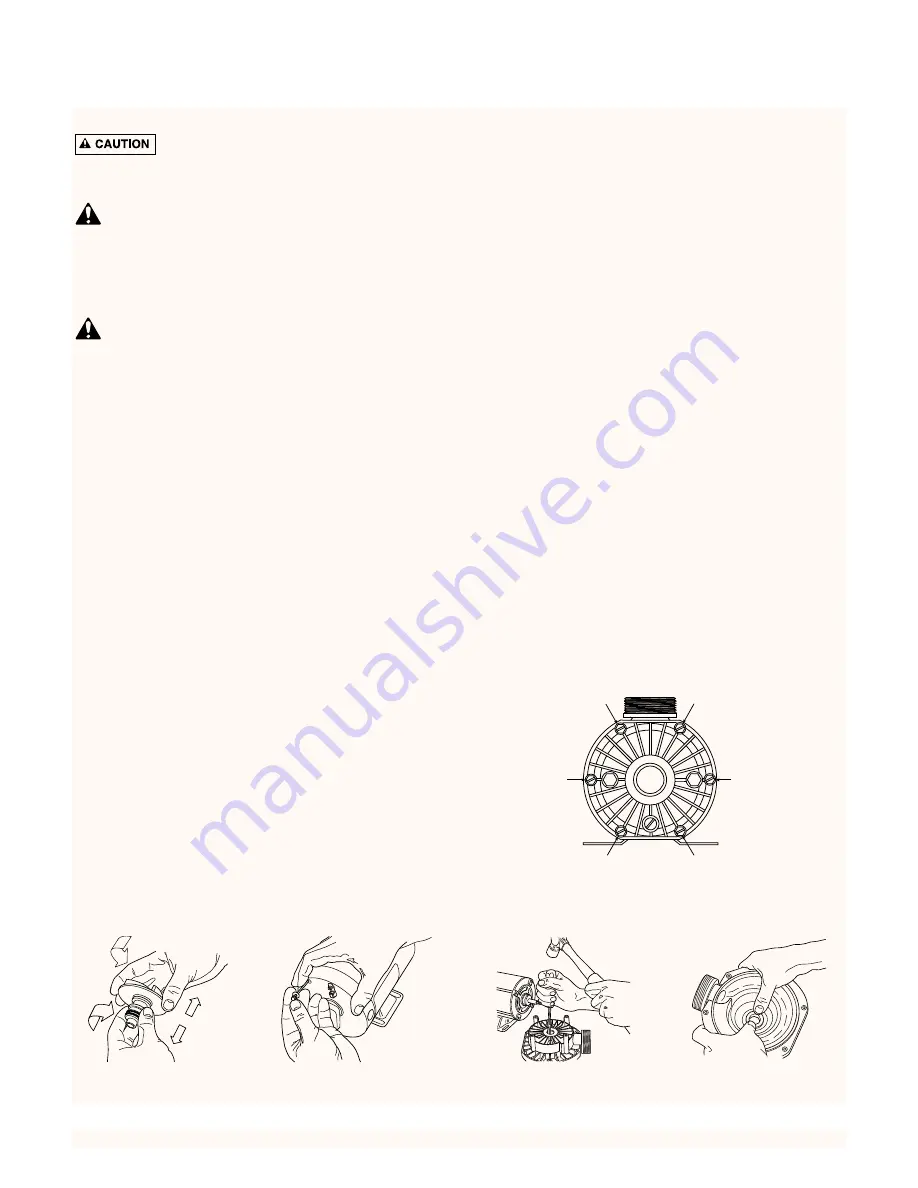
12
PUMP SERVICE
To protect against possible electric shock,
use only identical replacement parts when servicing.
System should only be serviced by qualified personnel.
Before removing trap cover:
1. STOP PUMP before proceeding.
2. CLOSE GATE VALVES in suction and discharge pipes.
3. RELEASE ALL PRESSURE from pump and piping sys-
tem.
To avoid dangerous or fatal electrical shock haz-
ard, turn OFF power to motor before working on
pump or motor.
Trap needs no lubrication or regular maintenance be-
yond reasonable care and periodic cleaning of strainer
basket.
If shaft seal is worn or damaged, repair as follows:
Pump Disassembly:
1.Unplug motor before servicing or repairing pump or
motor.
2.Close all valves in suction and discharge piping.
3.Remove drain plugs from the bottom of pump and
trap; drain pump completely.
4.Disconnect pipe unions (or clamps) on suction and
discharge piping. Remove hold down bolts and with-
draw complete pump/motor/trap assembly.
5.Remove cap screws (Key No. 16, Pages 14 and 15)
from front plate (Key No. 13). Remove front plate
with trap (Key No. 20) attached. Remove and inspect
O-Ring (Key No. 12).
6.Remove end cap (Key No. 2) from motor.
7.Hold motor shaft with 7/16” wrench on flats on
motor shaft; unscrew impeller (Key No. 11).
8.Carefully remove rotating half of seal (Key No. 10)
from impeller sleeve. Twist as you pull; make sure
you do not damage surface of sleeve where seal both
seats and seals. See Figure 14.
9.Remove motor throughbolts (see Figure 15). Remove
seal plate (Key No. 9). Tap stationary half of seal out
of seal plate (see Figure 16).
10. If necessary, disconnect electrical wiring from motor
terminal board and remove motor (Key No. 6) from
motor cover (Key No. 7).
Pump Assembly:
1. Examine seal cup and O-Rings. Replace anything that
shows signs of wear or damage.
2. Check the shaft seal (Key No. 10, Page 15) for scor-
ing, scratches, chips, etc., and for any signs of dam-
age to spring or retainer. Replace if any wear or
damage is visible.
3.Press stationary half of seal into seal plate (Key No. 9)
using finger pressure only (see Figure 17). Make sure
seal is firmly and evenly seated.
4.Install rotating half of seal on impeller sleeve. Push it
onto sleeve until it butts against back of impeller.
5.Insert impeller sleeve through center hole in seal
plate (Key No. 9). Thread slinger (Key No. 8) over the
end of the impeller sleeve.
6.If motor has been removed from motor cover, rein-
stall it now. Set up seal plate (Key No. 9) in front of
motor cover; hold motor shaft with 7/16” wrench on
shaft flats (under cap) and thread impeller through
center hole in seal plate onto shaft). Make sure that
slinger is in place on impeller sleeve – not loose on
shaft.
7.Install motor throughbolts; make sure seal plate butts
firmly against motor endbell.
8.Install front plate (Key No. 13). Tighten cap screws in
sequence as shown in Figure 18; tighten to 30 inch-
lbs. (34.5 cm-kg.) torque.
9.Reinstall drain plugs; reinstall pump and motor on
base and tighten hold-down bolts.
10. Reconnect unions; tighten hand tight only.
Figure 14
Figure 15
Figure 16
Figure 17
#1
#6
#2
#5
#3
#4
Start
Here
Figure 18 – Pump front Plate Torque Sequence.