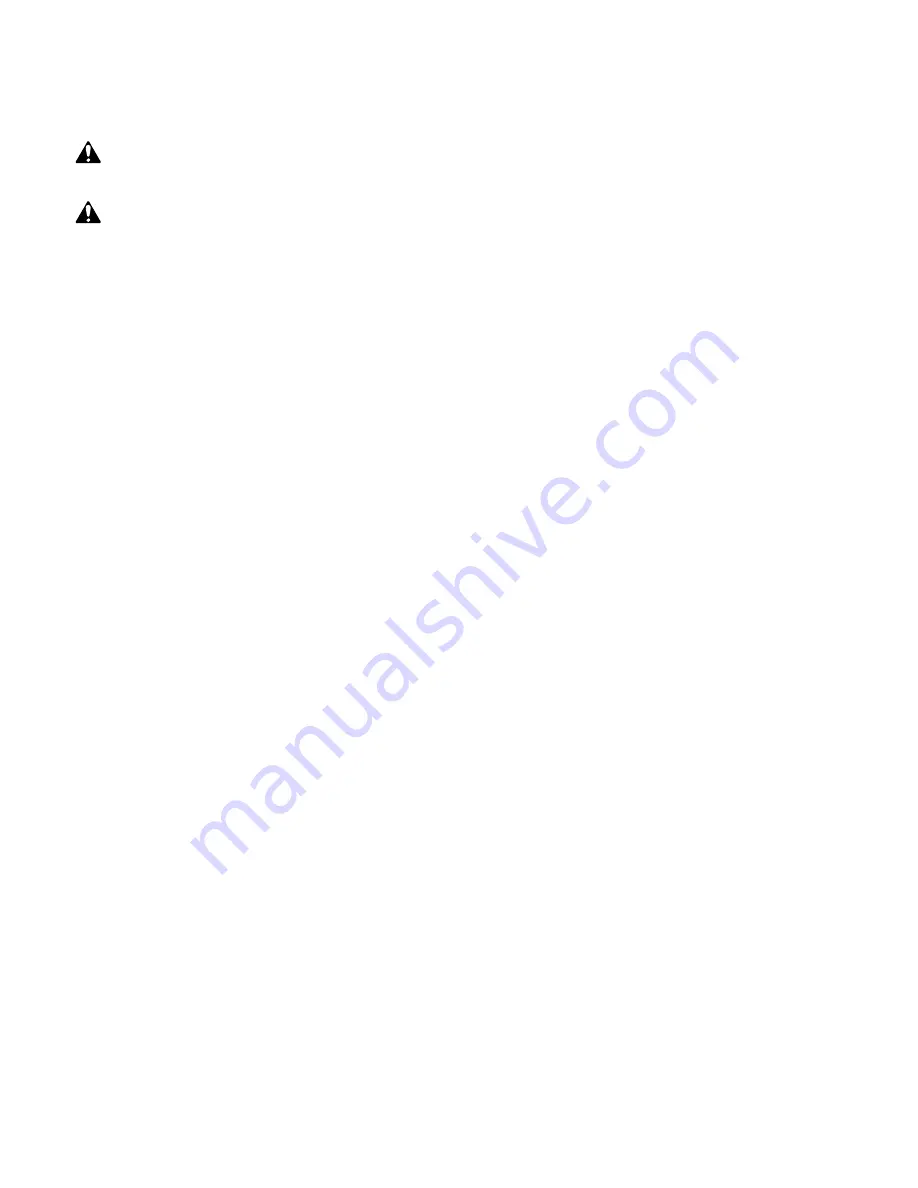
Read and understand safety and operating
instructions in this manual before doing any work
on pump!
Only qualified personnel should electrically test
pump motor!
FAILURE TO PUMP; REDUCED CAPACITY OR DIS-
CHARGE PRESSURE
Suction leaks/lost prime:
1. Pump must be primed; make sure that pump volute
and trap are full of water. See priming instructions,
Page 6.
2. Make sure there are no leaks in suction piping.
3. Make sure suction pipe inlet is well below the
water level to prevent pump from sucking air.
4. Suction lift of 1 to 2 feet (.3-.6M) will reduce per-
formance. Suction lift of more than 2 feet (.6M) will
prevent pumping and cause pump to lose prime. In
either case, move pump closer (vertically) to water
source. Make sure suction pipe is large enough.
Clogged pipe/trap/impeller, worn impeller:
1. Make sure suction trap is not clogged; if it is, clean
trap and strainer.
2. Make sure impeller is not clogged (follow instruc-
tions under “Removing Old Seal”, Page 8; check
impeller for clogging; follow instructions under
“Installing New Seal”, above, for reassembly).
3. Impeller and diffuser may be worn. If so, order
replacement parts from Repair Parts List, Pages 10
and 11.
Inadequate Circulation or Jet Action:
1. Check for blocked fittings. Blocked fittings will
cause poor flow and poor jet action.
2. Check trap basket; if plugged, turn pump off and
clean basket. Check and clean skimmer basket.
3. Check that gate valves are fully open.
4. Suction/discharge piping is too small.
5. Check and clean pool filter.
6. Check for clogged pipe/trap/impeller, Page 8.
7. Consult dealer/installer or service representative.
Circuit Breaker In Home Panel Trips Repeatedly:
1. Breaker must be of adequate capacity.
2. For GFCI breaker, test according to GFCI manufac-
turer’s instructions.
3. Be sure no other lights and appliances are on cir-
cuit.
4. Consult dealer/installer or service representative.
5. Voltage too high or too low. See “Voltage”, Page 5.
Electrical:
1. Pump may be running too slowly; check voltage at
motor terminals and at meter while pump is run-
ning. If low, see wiring instructions or consult
power company. Check for loose connections.
2. Pump may be too hot.
A. Check line voltage; if less than 90% or more
than 110% of rated voltage consult a licensed
electrician.
B. Increase ventilation.
C. Reduce ambient temperature.
D. Tighten any loose wiring connections.
3. Motor internal termal overload protector is open.
Motor runs too hot. Turn power to motor off. Check
for proper voltage. Check for proper impeller or
impeller rubbing.
4. Consult dealer/installer or service representative.
Mechanical Troubles and Noise:
1. If suction and discharge piping are not adequately
supported, pump assembly will be strained. See
“Installation”, Page 3.
2. Do not mount pump on a wooden platform!
Securely mount on concrete platform for quietest
performance.
3. Air leak in suction line (bubbles in water returning
to pool). Repair leak. Tighten trap lid.
4. Foreign matter (gravel, metal, etc.) in pump
impeller. Disassemble pump, clean impeller,
follow pump service instructions on Page 8 for
reassembly.
5. Cavitation.
Improve suction conditions.
Increase pipe size.
Decrease number of fittings.
Increase discharge pressure.
Reducer flow by throttling discharge gate valve.
9
TROUBLESHOOTING GUIDE