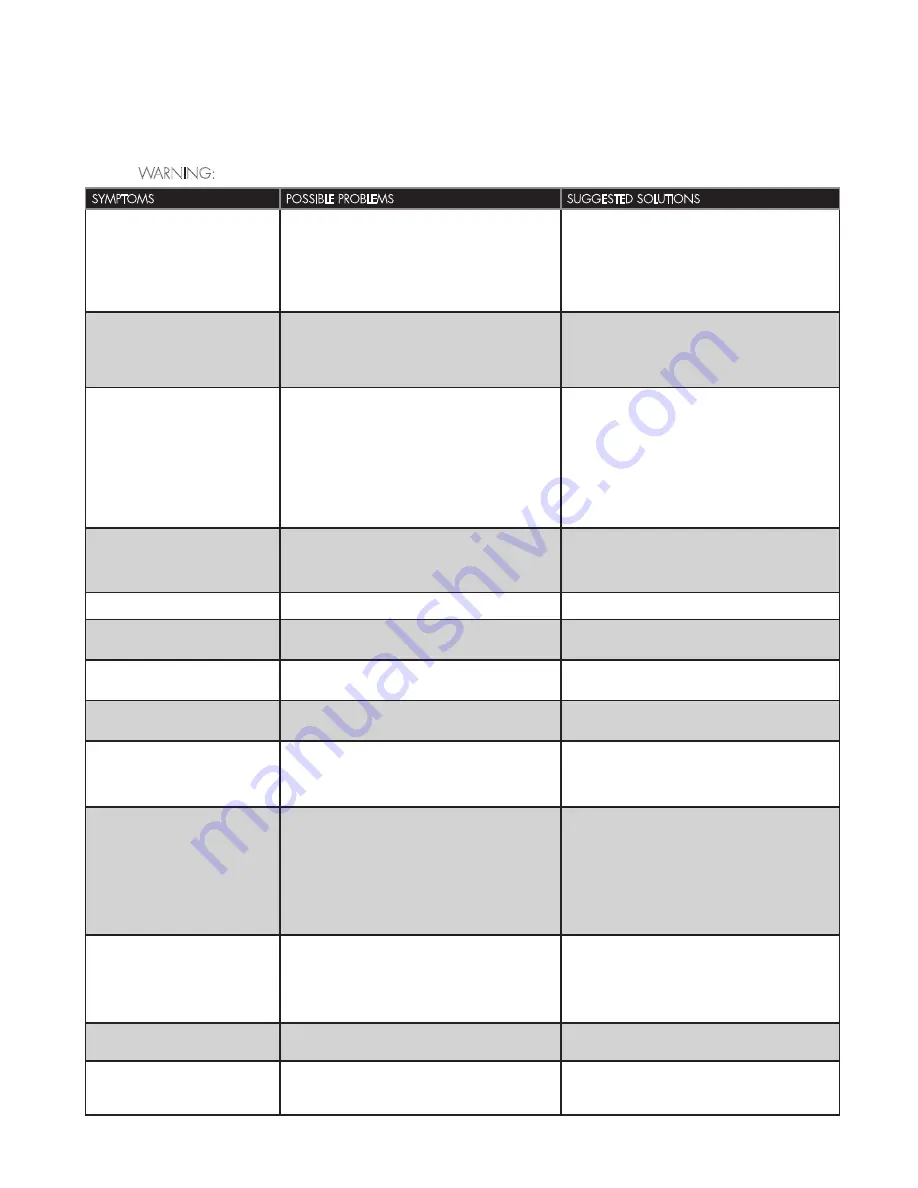
23 Aquatic
Elements Series Owner's Manual & Installation Guide
TROUBLESHOOTING GUIDE
WARNING: Always turn off power at the main electrical service panel when servicing your whirlpool.
SYMPTOMS
POSSIBLE PROBLEMS
SUGGESTED SOLUTIONS
Pump does not start:
1) GFCI or circuit breaker in OFF position.
2) Fuses blown or thermal overload open.
3) Locked motor shaft.
4) Motor windings burned out.
5) Defective starting switch inside single-phase motor.
6) Disconnected or defective wiring.
7) Low voltage.
1) Reset GFCI.
2) Contact your electrician.
3) Contact Aquatic.
4) Contact Aquatic.
5) Contact Aquatic.
6) Check and reconnect if needed.
7) Contact your electrician.
Motor does not reach full speed:
1) Low voltage.
2) Motor windings connected for wrong voltage.
3) Wiring too small.
4) Suction or discharge line partly plugged.
5) Impeller clogged.
1) Contact your electrician.
2) Contact Aquatic.
3) Contact your electrician.
4) Clean and unplug.
5) Clean and unplug.
Pump runs, water not circulating:
1) Leakage of air into suction system.
2) Faulty suction line check valve.
3) Suction screen may be clogged.
4) Impeller may be clogged.
1) Check suction screen for clogs.
2) Contact Aquatic.
3) Replace suction screen before operating. While
motor is off, unscrew safety suction cover and
remove any accumulated debris. If necessary,
call a plumber to check the suction line. If problem
persists, notify Warranty Services at (800) 945-
2726 to arrange a repair service call.
4)
Contact Aquatic.
Noisy pump and motor:
1) Worn motor bearings.
2) Pumps touching a stationary object.
3) Suction line partly plugged.
4) Pump not supported properly.
1) Contact Aquatic.
2) Refer to installer/dealer.
3) Clean and unplug.
4) Contact Aquatic.
Leakage of water at shaft:
1) Shaft seal requires replacement.
1) Contact Aquatic.
Leaking unions:
1) O-ring missing or damaged.
2) Loose unions.
1) Contact Aquatic.
2) Tighten unions.
Vibration noise:
1) Tub or tub plumbing is touching tile/wall.
2) Pump is touching framing.
1) Refer to installer/dealer.
2) Refer to installer/dealer.
Whirlpool jets emit water outside of
bathtub:
1) Insufficient water in bathtub.
1) Ensure water level is at least 3" above the highest
whirlpool jet.
Water leakage:
1) Call a plumber to determine and correct source of
leak. If plumber determines that whirlpool system is
at fault, notify Aquatic Technical Services at (800)
928-3707 to arrange a repair service call.
Motor overheats (protector trips):
1) Low voltage.
2) Motor windings connected for wrong voltage.
3) Wiring too small.
4) Suction or discharge line partly plugged.
5) Pump running at reduced speed.
6) Impeller clogged.
7) Pump located in a small space.
1) Contact your electrician.
2) Contact Aquatic.
3) Contact your electrician.
4) Clean and unplug.
5) Reference “SYMPTOMS: Motor does not reach full
speed.”
6) Clean and unplug.
7) Ensure pump has adequate ventilation and no
objects are blocking air flow.
Pump runs and there is water flow,
but no heat:
1) Limited water flow will NOT build up enough
pressure to allow the heater to come on.
2) System screen may be clogged.
1) Make sure all jets are open to allow a full flow of
water through the system.
2) While motor is off, clean the suction screen to
assure maximum water flow. Do not operate
whirlpool without replacing suction screen.
Pump does not shut off manually:
1) Defective on/off button.
2) Disconnected air hose.
1)
Shut off circuit breaker. Contact Aquatic.
2)
Shut off circuit breaker. Contact Aquatic.
Circuit breaker trips repeatedly:
1)
Defective breaker.
2)
Short circuit between bath and breaker box.
3) Other items are connected to the same circuit.
1)
Contact electrician.
2)
Contact electrician.
3)
Contact electrician.