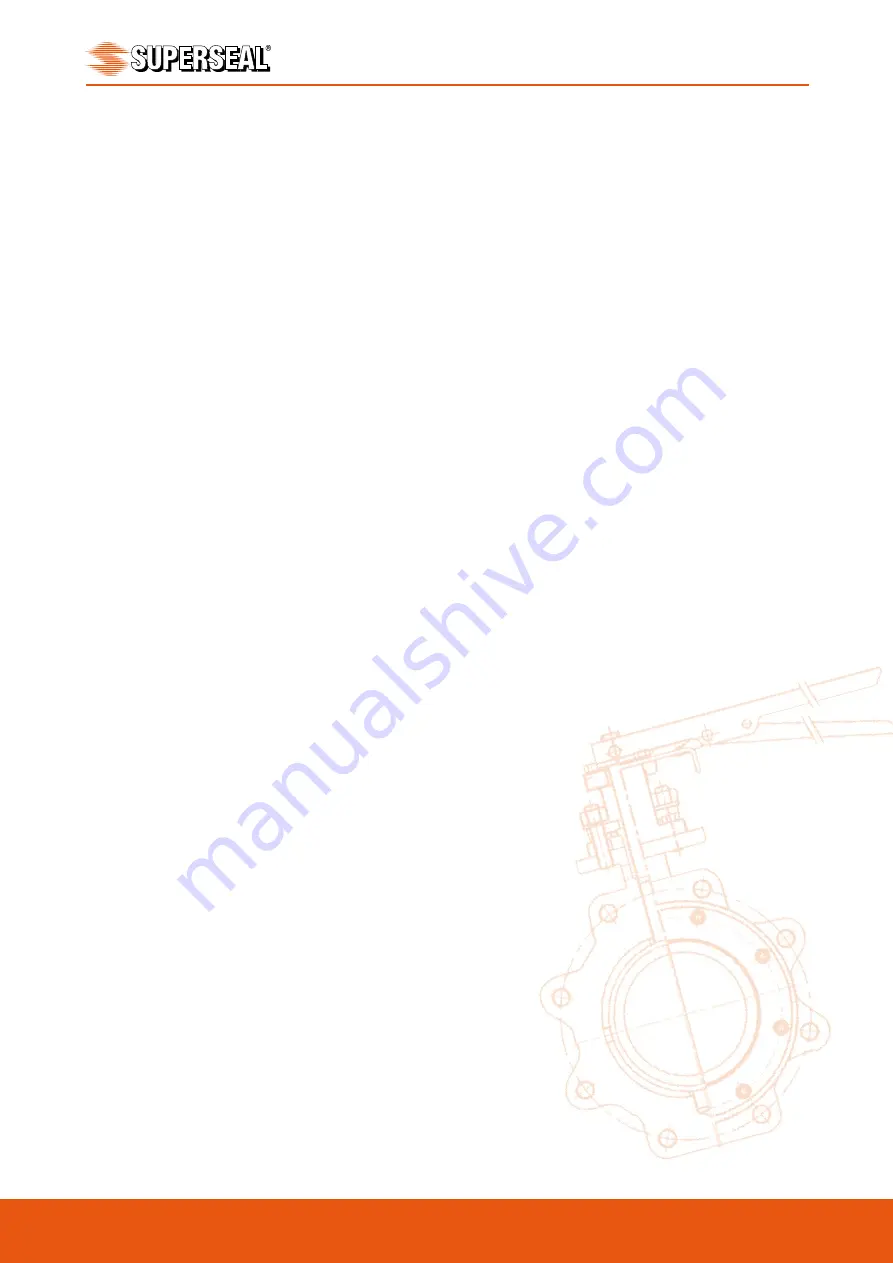
HIGH PERFORMANCE BUTTERFLY VALVES - MODEL SLHBF & SLHBFFS
Australian Pipeline Valve - Installation, Operation and Maintenance Manual
7
2.3 PREPARATION
If storage in the field for a long time before installation is necessary, it is suggested to put valves in a dry
and/or covered place. In this case the packaging and end covers integrity is especially important. All the
valves are supplied with special plastic ends to cover and protect the internal parts. We recommend you
do not remove them during storage period. Valves should be left in open position (unless actuated and set
fail closed).
a) Remove the valve end protection.
b) The inside of the valve should be inspected and blown out with compressed air. Adjacent piping must
be clean and free from debris to prevent damage to the valve.
c) To prevent valve distortion, inefficient operation or early maintenance problems, support piping on
each side of the valve.
d) Make sure the valve is positioned such that there is sufficient space so that the handwheel is easily and
safely reached and there is enough clearance for the stem when the valve is open.
e) Install valve according to the flow indicator on the valve body where applicable.
3 . 0 O P E R A T I O N
The valve operator types include: lever handle, manual gear, pneumatic actuator and electric motor
operated actuator. By rotating or closing the valve’s disc flow can be controlled through the pipeline by
regulating the flow or shutting it off.
(Generally, on-off direction is indicated on the operator).
For control
valve use, valves must be ‘metal to metal’ seated and throttling too far closed or at a small percentage of
open will dramatically reduce seat & disc and valve body life, even more so at higher pressures and if
service is not clean.