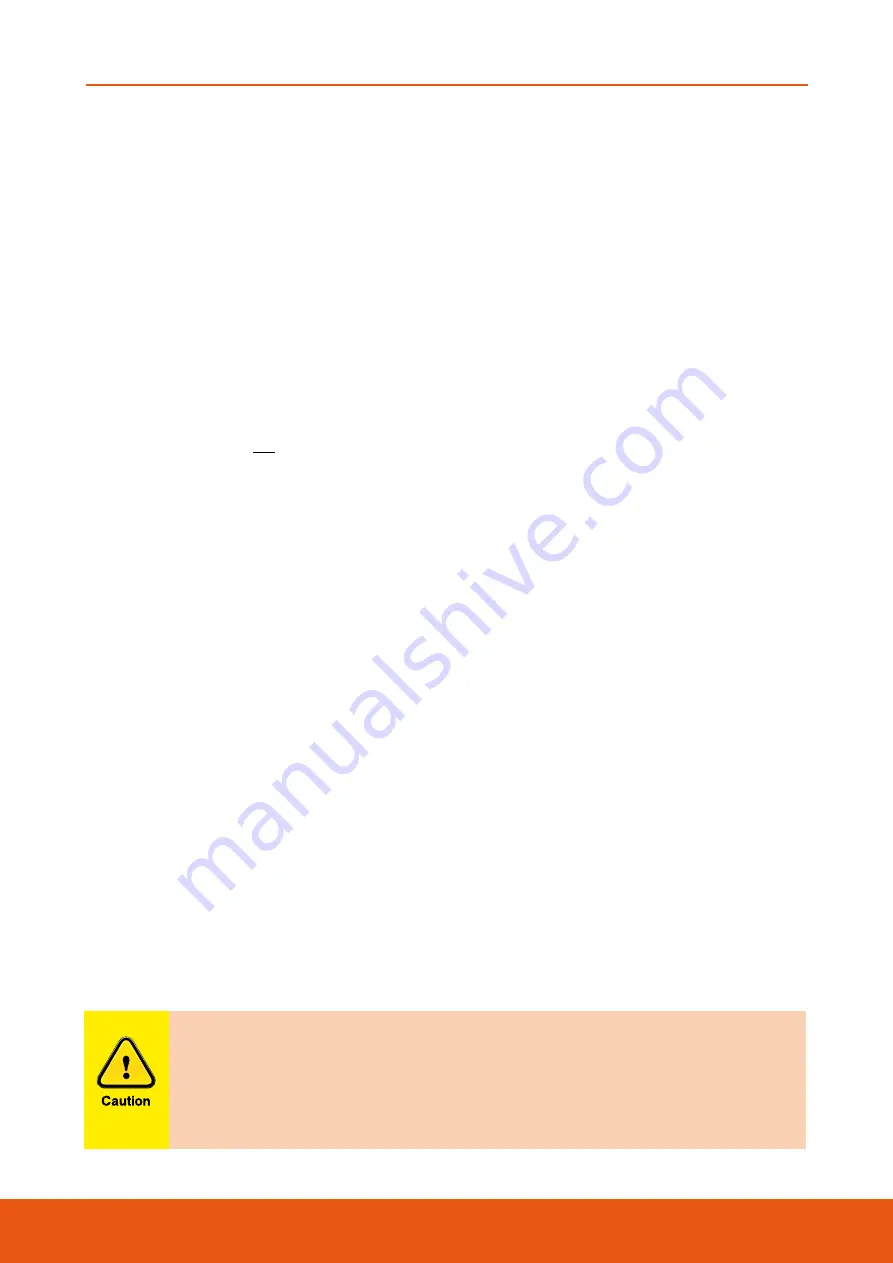
2.3 MAINTENANCE PRIOR TO FLUSHING
a- If the period between installation and flushing of the of the pipeline is longer than six months a
preventative maintenance operation is suggested.
• Lubricate the stem with fluid protective oil through the stem injector (if applicable). Do not grease
lubricate seats as grease may attract debris and damage seats.
• Remove valve from line and remove any debris and reflush.
2.4 FLUSHING THE PIPELINE
Flushing washes away all welding slag, dirt, sand, solids and debris collected in the pipelines during
construction prior to turning the valve and potentially damaging the seat. Flushing where deemed
necessary is the most dangerous activity for the valve, and it happens before they are put into service.
Ball valves are normally not lubricated, however, should it be required to flush potential debris (or
lubricate sticky valves) a different practise to the lubrication of either a gate valve or plug valve should
be employed. We recommend the following: -
1. Find a good grease for natural gas or your service. The grease must be insoluble. It must be resistant to
breakdown or shearing of the gel structure under high pressure injection and under the pressure
between seating surfaces. It must be stable over a wide range of temperatures, and not freeze. It must
not react chemically with the fluid and become solid, or rubber like (i.e. polymerize). Depending on the
service, the best greases are fully synthetic; if you have any doubt or concern, consult a valve
maintenance expert. Field experience has shown that greases and sealants may cause severe problems
with the seat and seal arrangement if used regularly during preventative maintenance. If a non-leaking
ball valve is lubricated with an adhesive grease/sealant, the floating, spring loaded seats can become
stuck within their seat pockets. When the ball floats due to a pressure differential across the valve, the
seals cannot track the ball and leakage can occur. Grease manufacturers produce low viscosity
synthetic ball valve lubricants such as Clare UK “601-Fluid”. Such light greases offer the following
advantages to heavier emergency sealant greases and cheaper brands of light greases:
• Enhanced resistance to hydrocarbon fluids and gases.
• Will not dry out or form a gum like some other greases when used within its application temperature
range.
• Will not disrupt the operation of the seat and seal arrangement.
Of course, be warned any type of grease, especially synthetic grease can become hard or sticky causing
torque problems and seat spring jamming in which case a line flushing agent like Clare 601 Valve Cleaner
may be required. Of course, for leaking seats a heavier sealant like Clare 601 lubricant must be used for
temporary emergency sealing.
Australian Pipeline Valve - Installation, Operation and Maintenance Manual
8
SIDE ENTRY 3P TRUNNION BALL VALVES API6D STANDARD - BVF100 SERIES
Beware of greases made of synthetic oil with a mineral thickener. The natural gas
(or storage prior to use) washes away the oil, leaving the thickener behind. The
thickener is like a powder that caulks or bakes hard on the seats, increasing the
operating torque. Always wipe the seats clean as much as possible prior to
installation. The increased torque may effect pneumatic actuated valves.