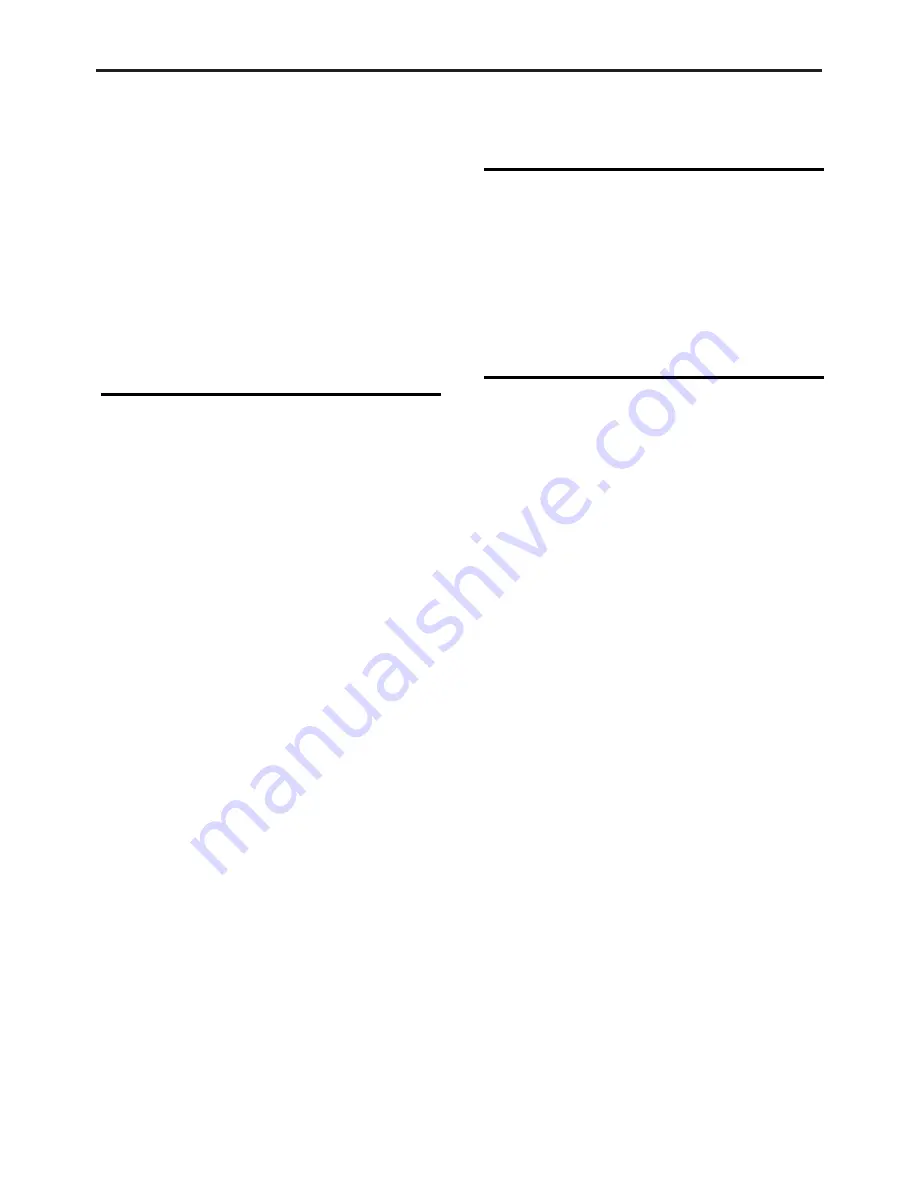
MHC 5
16
(doc no.)
SAFETY & OPERATING INSTRUCTIONS
Starting a cut
♦
Stand steady and make sure that your feet and
hands are at a safe distance from the drill bit.
♦
To start the drilling it is advisable to either turn
the core drill to one side in order to obtain an
initial groove and then slowly return to horizontal
or vertical position as soon as the drill bit has
engaged in the material to be drilled, or provide
a guide to stop the drill bit skidding across the
surface of the material to be drilled.
When taking a break
♦
During all breaks you must place the machine in
such a way that there is no risk for it to be
unintentionally started. Make sure to place the
machine on the ground, so that it can not fall.
♦
In the event of a longer break or when leaving the
workplace: Switch off the power supply and then
bleed the machine by activating the start and stop
device.
Maintenance
Regular maintenance is a basic requirement for the
continued safe and efficient use of the machine.
Follow the maintenance instructions carefully.
♦
Before starting maintenance on the machine,
clean it in order to avoid exposure to hazardous
substances. See “Dust and fume hazards”
♦
Use only authorised parts. Any damage or
malfunction caused by the use of unauthorised
parts is not covered by warranty or product
liability.
♦
When cleaning mechanical parts with solvent,
comply with appropriate health and safety
regulations and ensure there is satisfactory
ventilation.
♦
For major service of the machine, contact your
nearest authorised workshop.
♦
After each service, check that the machine's
vibration level is normal. If not, contact your
nearest authorised workshop.
Every day
♦
Clean and inspect the machine and its functions
each day before the work commences.
♦
Conduct a general inspection for leaks and
damage.
♦
Check the function of the trigger. Make sure that
it returns to its stop position when it is released.
Periodic maintenance
After each operating period of approximately 100
working hours or three times a year the machine
must be dismantled and all parts be cleaned and
checked. This work must be performed by authorized
staff, trained for this task.
Storage
♦
Check that the machine is properly cleaned before
storage.
♦
Store the machine in a dry place.
♦
Keep the machine and tools in a safe place, out
of the reach of children and locked up.
Disposal
A used machine must be treated and disposed of in
such a way that the greatest possible portion of the
material can be recycled and any negative influence
on the environment is kept as low as possible, and
in respect to local restrictions.
3392 5192 90a | Original instructions
16
COR 5, 15
Safety and operating instructions
Summary of Contents for MHC 5
Page 1: ...Safety Operating Instructions Handheld Core Drill MHC 5 AMERICAN PNEUMATIC TOOLS...
Page 2: ...MHC 5 2 doc no SAFETY OPERATING INSTRUCTIONS 3392 5164 01c 2 5 15...
Page 4: ...MHC 5 4 doc no SAFETY OPERATING INSTRUCTIONS...
Page 20: ...AMERICAN PNEUMATIC TOOLS 800 532 7402 fax 800 715 6502 1000 S Grand Ave Santa Ana CA 92705...