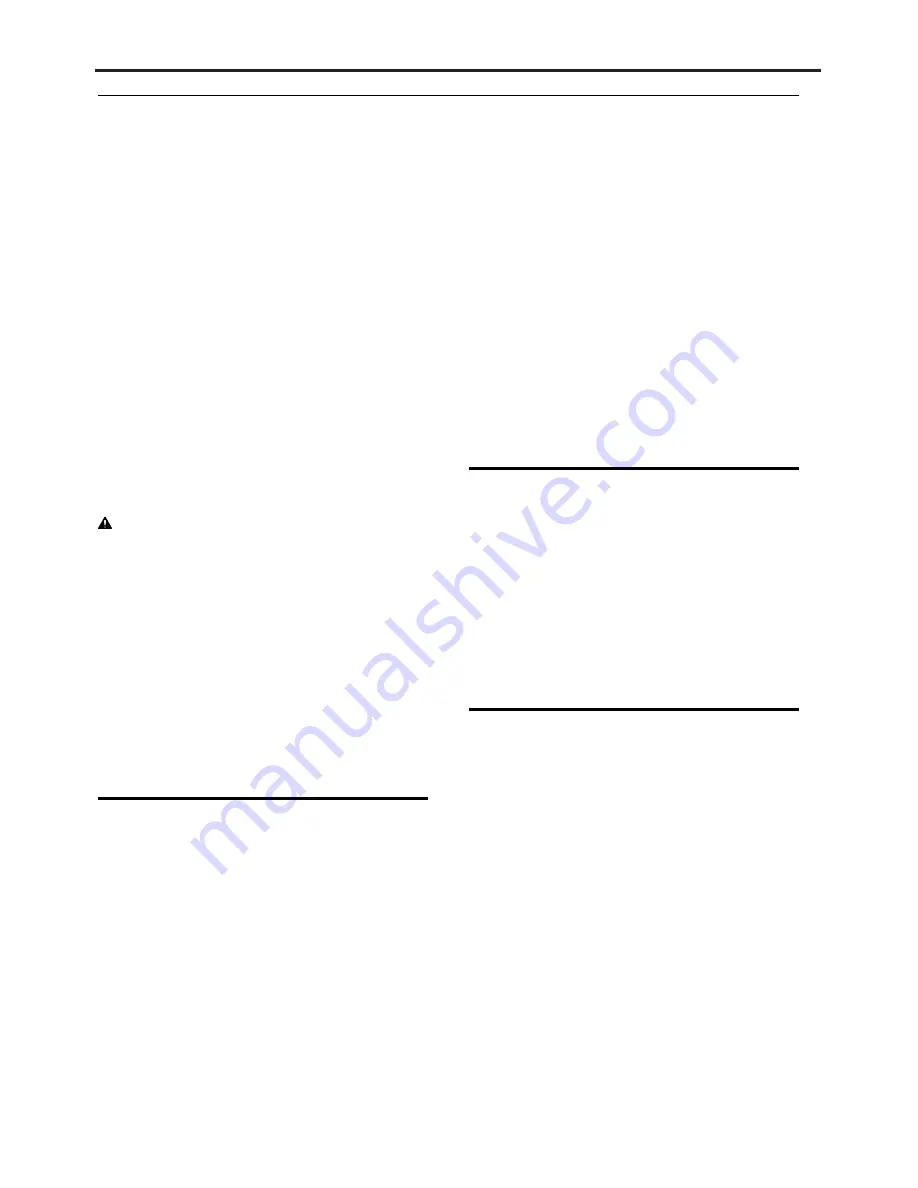
MHC 5
15
(doc no.)
SAFETY & OPERATING INSTRUCTIONS
Fitting and removing the drill bit
Smaller diameter drill bits are fitted directly into the
machine drive shaft (½" BSP). For larger diameter
drill bits, use an ½" BSP male x 1¼ UNC male drive
adaptor, which is included with the machine.
To prevent an accidental start:
1)
Switch off the power supply and disconnect
the machine from the power source.
2)
Screw the drill bit into the machine.
3)
Lock the spindle using a spanner and tighten
the drill bit.
4)
Bleed the machine by pressing the start and
stop device.
NOTICE
Never cool a hot insertion tool in water,
it can result in brittleness and early failure.
Operation
WARNING Involuntary start
Involuntary start of the machine may cause injury.
►
Keep your hands away from the start and stop
device until you are ready to start the machine.
►
Learn how the machine is switched off in the event
of an emergency.
►
Stop the machine immediately in all cases of
power supply interruption.
NOTICE
Never exceed the maximum flow for the
machine, as this might lead to failure of the drill bit
and damage to the machine.
Preparations before starting
Check the drilling equipment
♦
Check that all of the drilling equipment is in a
good condition.
♦
Inspect the hoses generally for signs of damage.
♦
Check that the drill bit is in a good condition and
has the correct diameter for the size of the core
drill.
♦
Clean all safety labels. Replace any that are
missing or cannot be read.
♦
Ensure that the hydraulic couplings are clean and
fully serviceable.
♦
Ensure that the fittings are tight and leak-proof.
♦
Always use the core drill with a front handle
mounted, to absorb the reaction torque.
♦
Screw the drill bit into the nose end drive of the
shaft and tighten by means of the spanner flats
provided.
♦
Check that the core drill is not blocked and that
water flows through without obstruction.
♦
Ensure that the power source to be used is
compatible with the machine model, see the
"Technical data".
♦
Atlas Copco recommends using an LFD oil flow
divider, if the flow from the power source can
exceed the maximum allowed oil flow.
Start and stop
♦
Start the machine by pressing the trigger while
firmly holding the handle. By gradually applying
pressure on the trigger, the speed may be reduced
to obtain a soft start.
♦
Stop the machine by releasing the trigger. The
trigger returns automatically to the stop position.
When the work is done, stop the power source.
Disconnect the hoses and fit the protective caps
to the quick-release couplings.
Operating
Before drilling
1. Connect the hydraulic hoses.
2. Connect the water hose to the water tap.
3. Screw the handle lightly into the handle ring and
place the handle in a position that is comfortable
for the operator.
4. Lock the handle ring in this position by
tightening the handle to grip the bearing
housing. Ensure that the handle remains locked
throughout the drilling operation.
5. Start the power source.
6. Activate the water supply.
15
3392 5192 90a | Original instructions
Safety and operating instructions
COR 5, 15
Summary of Contents for MHC 5
Page 1: ...Safety Operating Instructions Handheld Core Drill MHC 5 AMERICAN PNEUMATIC TOOLS...
Page 2: ...MHC 5 2 doc no SAFETY OPERATING INSTRUCTIONS 3392 5164 01c 2 5 15...
Page 4: ...MHC 5 4 doc no SAFETY OPERATING INSTRUCTIONS...
Page 20: ...AMERICAN PNEUMATIC TOOLS 800 532 7402 fax 800 715 6502 1000 S Grand Ave Santa Ana CA 92705...