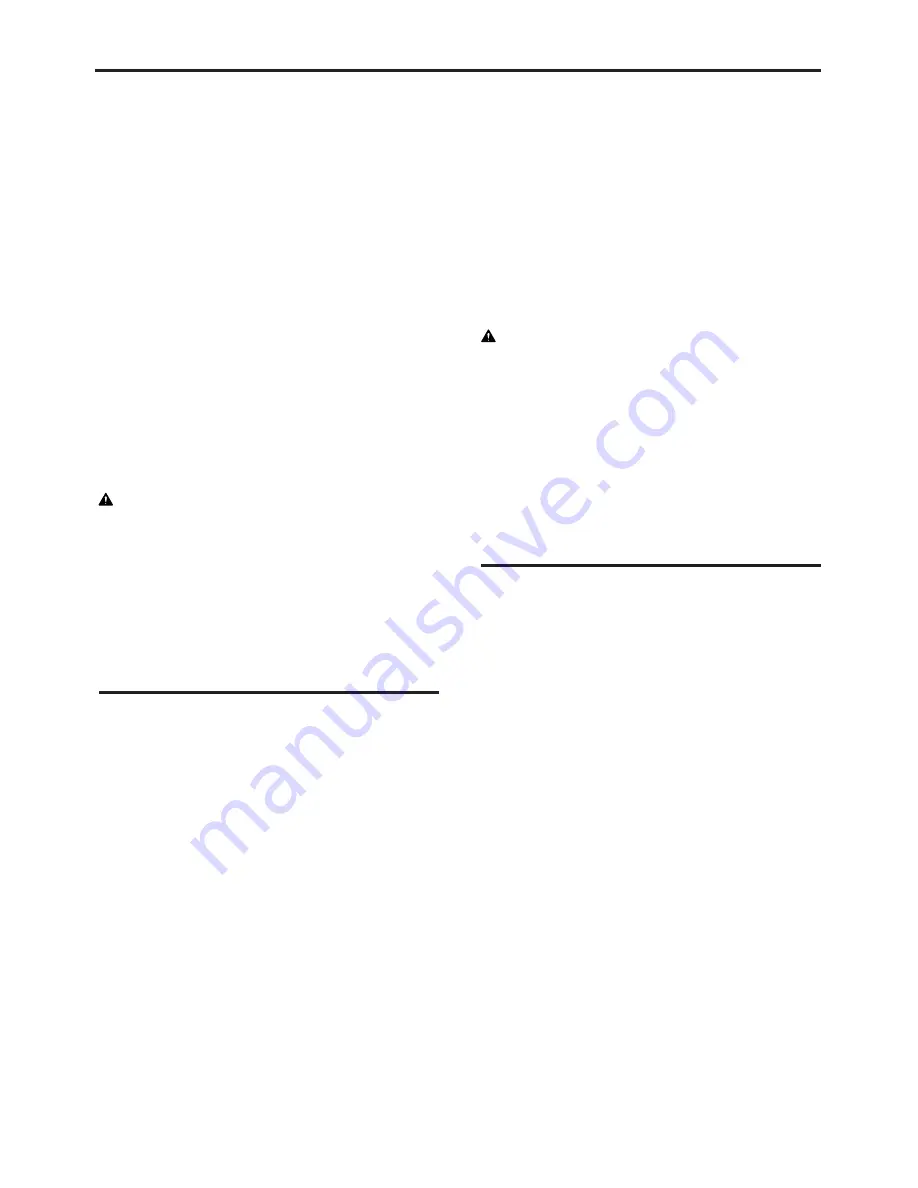
AWP 2, AWP 3
11
(doc no.)
SAFETY & OPERATING INSTRUCTIONS
Standard mineral or synthetic oil can be used. Make
sure to only use clean oil and filling equipment.
When the machine is used continuously, the oil
temperature will stabilise at a level which is called
the working temperature. This will, depending on
the type of work and the cooling capacity of the
hydraulic system, be between 20-40°C (68-104°F)
above the ambient temperature. At working
temperature, the oil viscosity must be within the
preferred limits. The viscosity index indicates the
connection between viscosity and temperature. A
high viscosity is therefore preferred, because the oil
can then be used within a wider temperature range.
The machine must not be used, if oil viscosity fails
to remain within the permitted area, or if the
working temperature of the oil does not fall between
20°C (68°F) and 70°C (158°F).
Operation
WARNING Involuntary start
Involuntary start of the machine may cause injury.
►
Keep your hands away from the start and stop
device until you are ready to start the machine.
►
Learn how the machine is switched off in the event
of an emergency.
►
Stop the machine immediately in all cases of
power supply interruption.
Preparation before starting
The following checks should be made each time you
start to use the pump. All these checks concern the
serviceability of the pump. Some concern your
safety:
>
Clean all safety stickers. Replace any that are
missing or cannot be read.
>
Inspect the hoses generally for signs of damage.
>
Remove the protective caps from the quick-release
couplings.
>
Clean the quick-release couplings if needed and
connect the tail-hose to the extension hoses of
the power source.
>
Connect the tool.
>
Ensure that the hydraulic couplings are clean and
fully serviceable.
>
The correct rotation is counter clockwise seen
from below. If rotation is clockwise, check the
hoses. Incorrect connection may result in leaks
and damage to the hydraulic motor.
>
Grease the bearing in the pump housing through
the grease nipple in the bearing housing (3
strokes). All quality types of grease are applicable.
>
The suction strainer and base plate must always
be fitted to the pump.
>
Ensure that any power source you plan to use is
compatible with the pump model used, see the
"Technical data". Atlas Copco recommends using
an LFD oil flow divider, if the flow from the power
source can exceed the maximum allowed oil flow.
WARNING Whipping hydraulic hose
Hydraulic hoses under pressure can whip
uncontrollably if screws loosen or are loosened. A
whipping hydraulic hose can cause severe injuries.
►
Depressurise the hydraulic system before
loosening the connection of a hydraulic hose.
►
Tighten the nuts on the connections of the
hydraulic hoses to the required torque.
►
Check that the hydraulic hose and the connections
are not damaged.
Start and stop
Starting the pump
>
Start the power source and allow it to run for a
few minutes to warm up the hydraulic oil.
>
WAP 3 pump only: Attach a rope or other device
to the handle of the pump and lower the pump
into the water.
>
Activate the control valve of the power source to
start the hydraulic oil flow.
Stopping the pump
>
When pumping is complete, activate the control
valve to stop the hydraulic oil flow.
>
Stop the engine of the power source.
>
Disconnect the hoses and fit the protective caps
to the quick-release couplings.
Connecting hoses
Inspect the couplings
♦
Make sure the couplings are clean and serviceable.
Connect the hoses
♦
Attach the return line hose.
♦
Attach the feed line hose.
♦
Rotate the collar on the female coupling to secure
the coupling.
Check the hydraulic oil level
Safety and operating instructions
Summary of Contents for AWP 2
Page 2: ...AWP 2 AWP 3 2 doc no SAFETY OPERATING INSTRUCTIONS...
Page 4: ...AWP 2 AWP 3 4 doc no SAFETY OPERATING INSTRUCTIONS...
Page 17: ...AWP 2 AWP 3 17 doc no SAFETY OPERATING INSTRUCTIONS...
Page 18: ...AWP 2 AWP 3 18 doc no SAFETY OPERATING INSTRUCTIONS...
Page 19: ...AWP 2 AWP 3 19 doc no SAFETY OPERATING INSTRUCTIONS...
Page 20: ...AMERICAN PNEUMATIC TOOLS 800 532 7402 fax 800 715 6502 1000 S Grand Ave Santa Ana CA 92705...