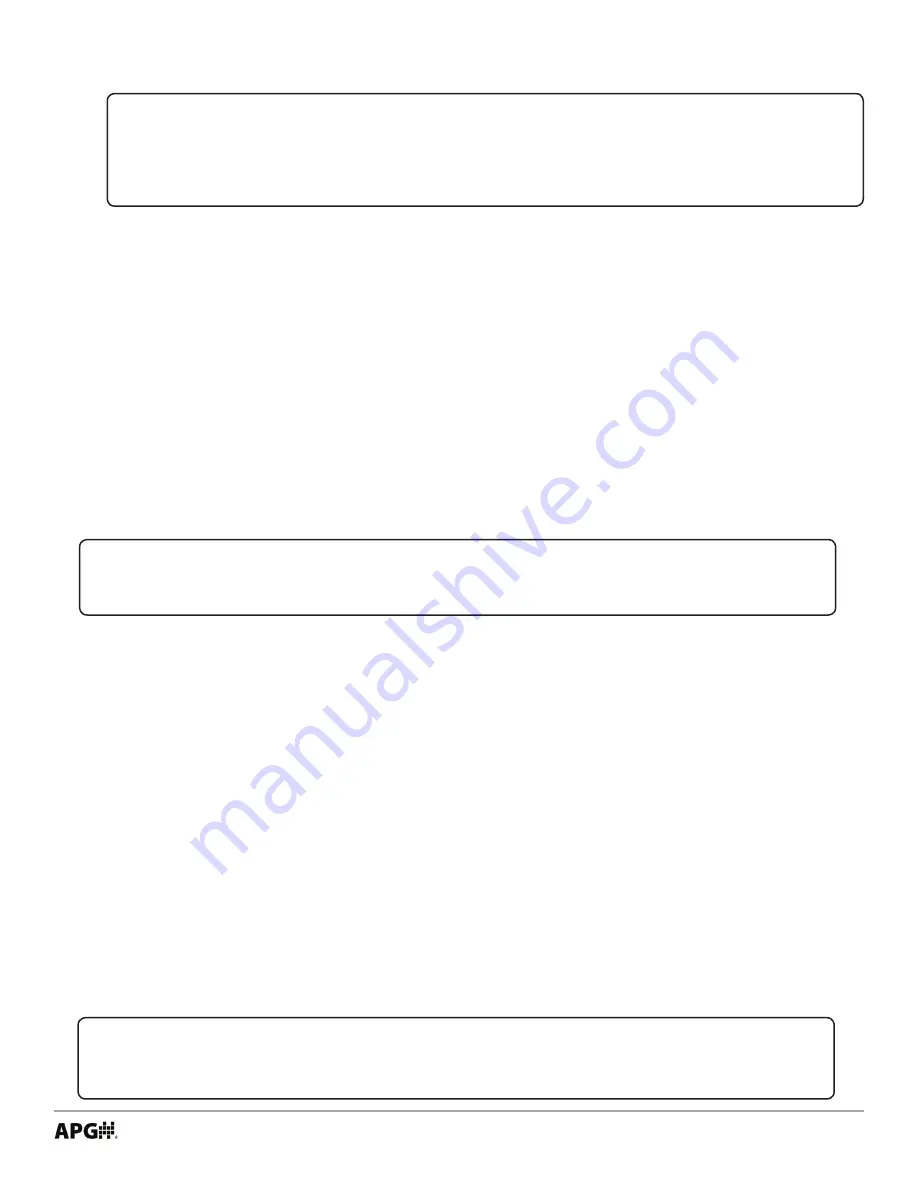
5
Tel: 1/888/525-7300 • Fax: 1/435/753-7490 • www.apgsensors.com • [email protected]
Removing your PT-500 from service must be done with care. It’s easy to create an unsafe situation, or
damage your sensor, if you are not careful to follow these guidelines:
•
For sensors installed via NPT process connection, make sure the pressure is completely removed from
the line or vessel. Follow any and all procedures for safely isolating any media contained inside the line
or vessel.
•
Remove the sensor with an appropriately sized wrench (per your process connection).
•
For suspended sensors, retrieve the sensor from the vessel. Follow any and all procedures for safely
isolating any media contained inside the line or vessel.
•
Carefully clean the sensor’s fitting and diaphragm of any debris (see General Care) and inspect for
damage.
•
Store your sensor in a dry place, at a temperature between -40° F and 180° F.
• Removal Instructions
DANGER
: Removing your process connected PT-500 Pressure Transmitter while there
is still pressure in the line could result in injury or death.
Your PT-500 series pressure transmitter is very low maintenance and will need little care as long as it is
installed correctly. However, in general, you should:
•
For process connected sensors, keep the transmitter and the area around it generally clean.
•
Avoid applications for which the transmitter was not designed, such as extreme temperatures, contact
with incompatible corrosive chemicals, or other damaging environments.
•
Inspect the threads whenever you remove the transmitter from duty or change its location.
•
Avoid touching the diaphragm. Contact with the diaphragm, especially with a tool, could permanently
shift the output and ruin accuracy.
•
Clean the diaphragm or the diaphragm bore only with extreme care. If using a tool is required, make
sure it does not touch the diaphragm.
Chapter 3: Maintenance
• General Care
IMPORTANT
: Any contact with the diaphragm can permanently damage the sensor.
Use extreme caution.
NOTE
: If your PT-500 has a vent tube, do not seal, cover, or close the vent tube with
anything other than an APG-provided venting cap or desiccant drying cartridge (See Fig-
ure 4.1 and 4.2). Unapproved seals or covers will prevent proper sensor operation.