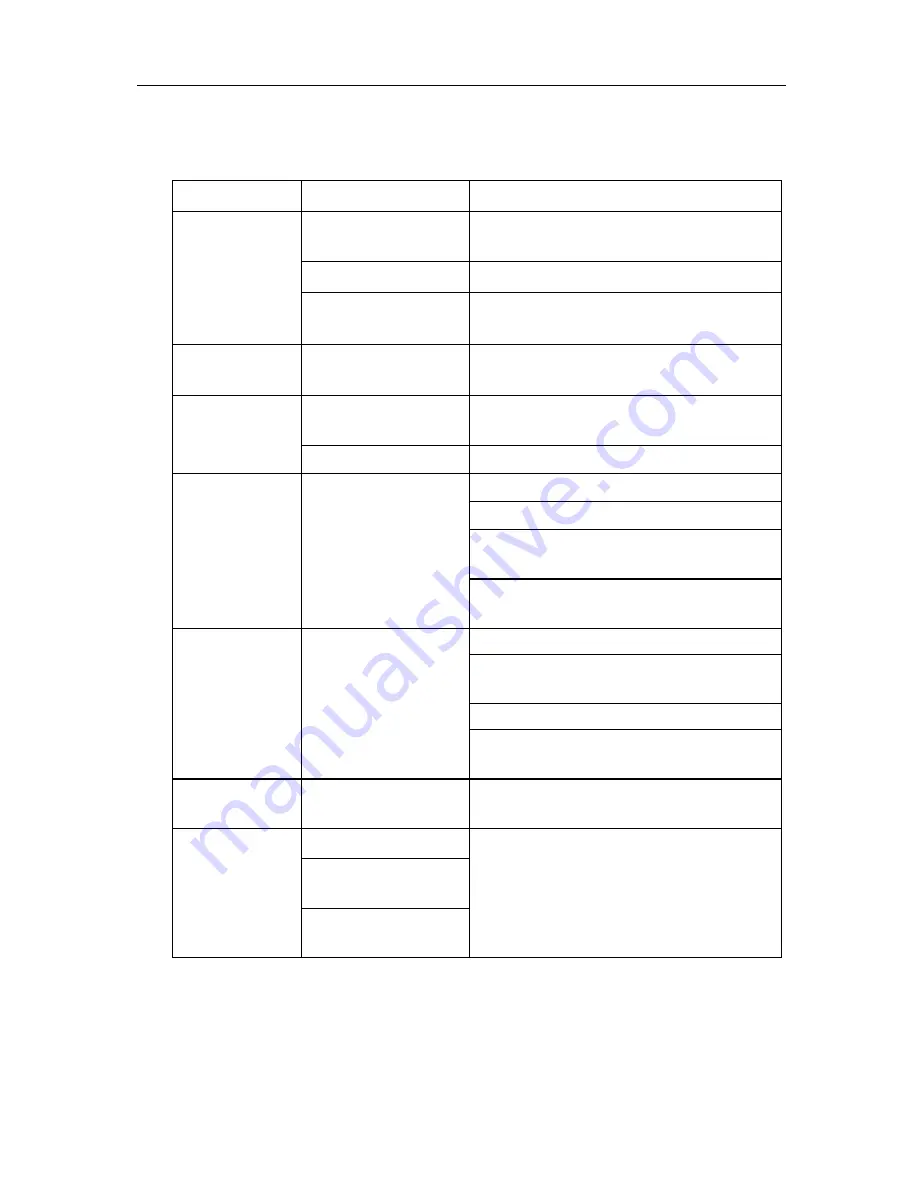
OPERATION MANUAL FOR SCD( AN-350) SERIES CAPACITOR DISCHARGE STUD WELDING MACHINES
10/2000 ANTECH ELECT.LTD.
26
9. Diagnostics and Repairing:
The following table provides a guide for troubleshooting the welding machine:
Symptom
Cause
Solution
Faulty input power
Check supply voltage if it is 220V
± 15%? 50/60Hz
Loose power plug Connect the power socket
‘ POWER’ LED
does not turn
on
Loosen or broken
power wires
Open the power plug and re-connect the
power wires
Faulty controller Replace defective AN350 controller
AN-350/SCR driver
wires open-circuit
Check wiring between AN350 and the SCR
driver, ensure good connections
AN-350 shows
E01 error
SCR over-heated
Check SCR and associated assembly
Check discharge SCR assembly
Replace faulty SCR (thyrister)
Check X5-5 ? X5-6 on SCR driver for
wirings to discharge SCR
AN-350 shows
E03 error
Discharge fault
Replace faulty AN-350 controller or
SCR driver board
Check charging SCR assembly
Check X6-2 , X6-3 on SCR driver for
wirings to the charging SCR
Replace charging SCR or resistor
AN-350 shows
E04 error
Charging fault
Replace faulty AN-350 controller or
SCR driver board
AN-350 shows
E05 error
Over-voltage fault
Replace faulty AN-350 controller or
SCR driver board
Broken control wire
Faulty stun gun
solenoid
Malfunction
Stud Gun
Faulty mechanical
parts
Inspect wiring and/or replace stun
gun assembly
□
Note: 1. The power must be disconnected for diagnostics and repairing in
order to prevent accidents!
2.Contact our technical service department immediately for
technical advice, service, repairing and spare parts.