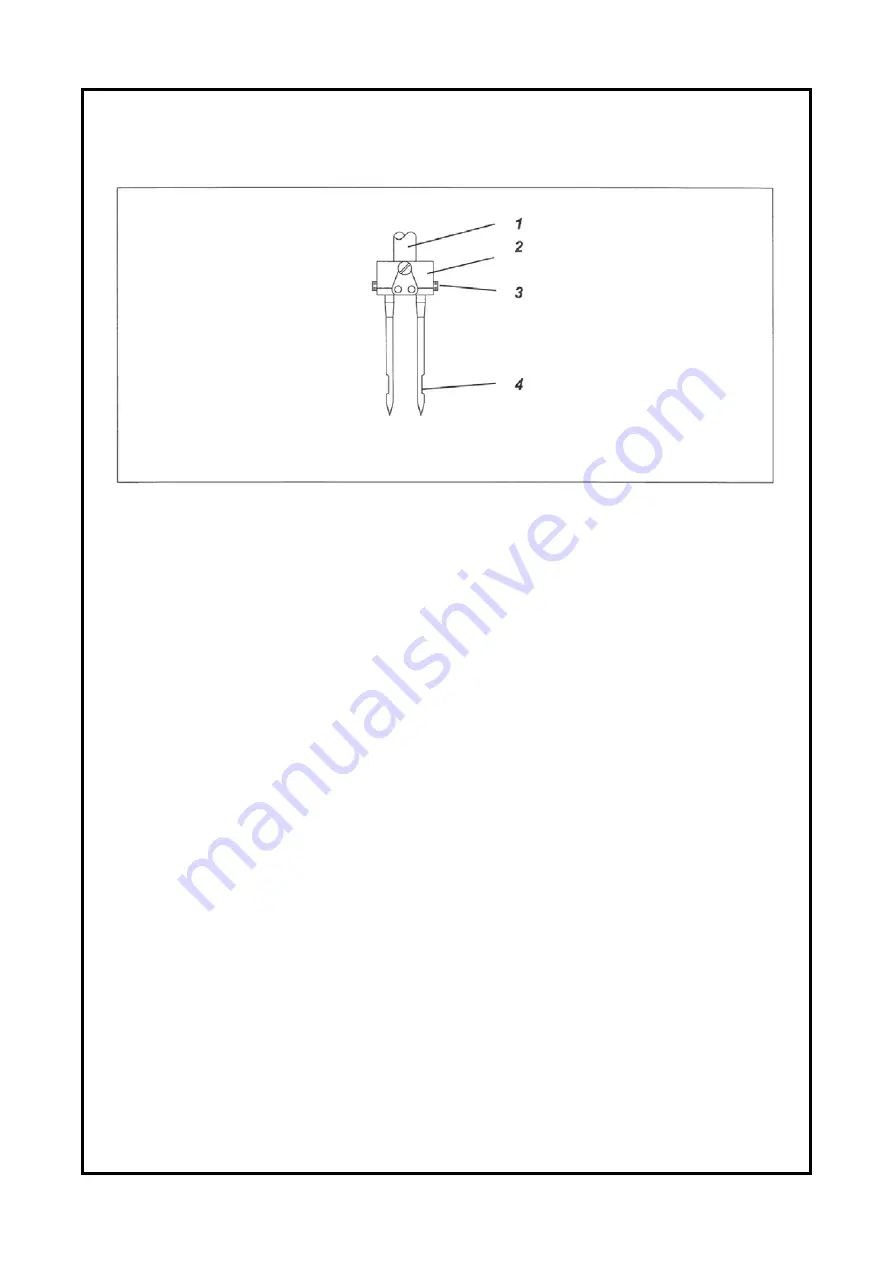
ANITA ©
GP-137-448 MH/L33, GP-237-448 MH/L33
18
13. CHANGING THE NEEDLE IN 2-NEEDLE MACHINES
Turn off the main switch. Needle may only be changed if the machine is switched off. Turn
the handwhell until the needle bar 1 reached its upper end position. Loosen screw 3. Take out
needle from the needle bar holder 2. Insert the new needle properly into the needle bar hole 2,
aligning it so that from view of operator the right needle groove 4 points to the right and left
needle groove to the left (see picture above). Tighten screw 3.
If needle with a different size is inserted, distance between hook and needle must be adjusted,
otherwise following faults can occur:
If thinner needle is used:
-
Missing stitches
-
Thread damage
If thicker needle is used:
-
Damage of hook tip
-
Damage of needles
www.garudan.cz