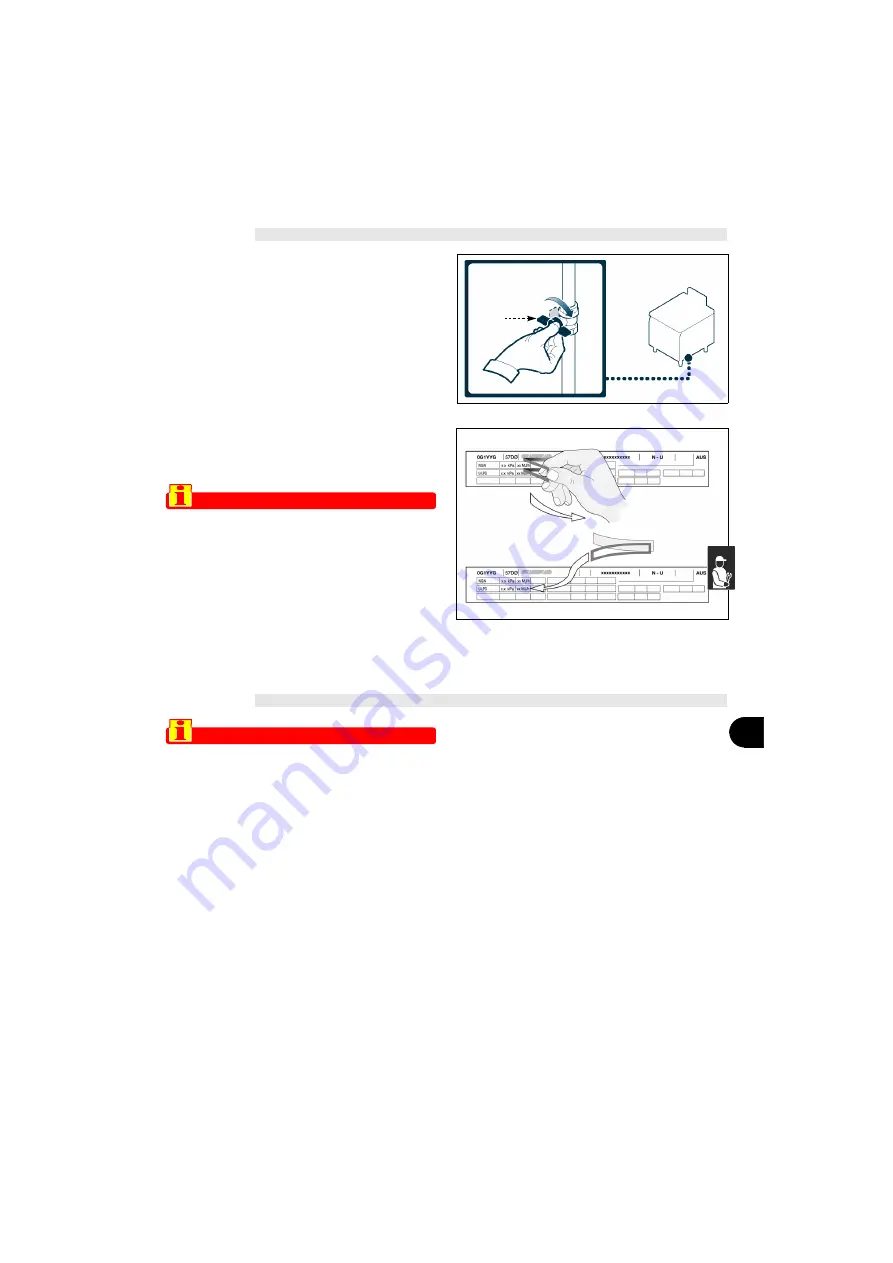
C1
39
60
330
0_
1.f
m
- 13 -
IT
AUS
DE
FR
ES
CONVERSION OF THE GAS SUPPLY
The constructor has tested the appliance with its own
mains gas, identified by the sticker applied to the
nameplate.
If the type of gas to be connected is different from that
used for testing, proceed as follows.
1 - Turn off the gas supply tap (
A
).
2 - Change the burner nozzle (see page 16).
3 - Change the pilot light nozzle (see page 16).
4 - Adjust the minimum setting on the gas control
valve (see page 14).
5 - If necessary, adjust the burner primary air (see
6 - Remove the sticker from the nameplate and ap-
ply the new one to identify the gas being used.
Important
On completion of the operation, make sure
that there are no gas leaks or malfunc-
tions.If converting from Natural Gas to Uni-
versal LPG make sure the Natural Gas
Regulator is removed.
TESTING OF THE APPLIANCE
Important
Before it is put into service, the system
must be tested to check the operating con-
ditions of every single component and
identify any malfunctions. In this stage, it is
important to check that all health and safety
requirements have been complied with in
full.
To test the system, make the following checks:
1 - turn on the gas supply tap and check that the con-
nections are right;
2 - check that the mains gas is the same as that
used for commissioning of the appliance, and
carry out the conversion procedure if neces-
sary (see page 13);
3 - check that the burner is switching on correctly and
its combustion;
4 - check the gas pressure and flow-rate at minimum
and maximum settings and adjust if necessary
(see page 14);
5 - check that the safety thermocouple is working
correctly;
6 - check that there are no gas leaks;
7 - check that the nameplates specify the correct gas
for the country of use.
After testing, if necessary instruct the user in all the
skills necessary for putting the appliance into opera-
tion in conditions of safety, in accordance with legal
requirements.
A
IDM-3960200240.tif
A.po_Convers_gas_aus.tif