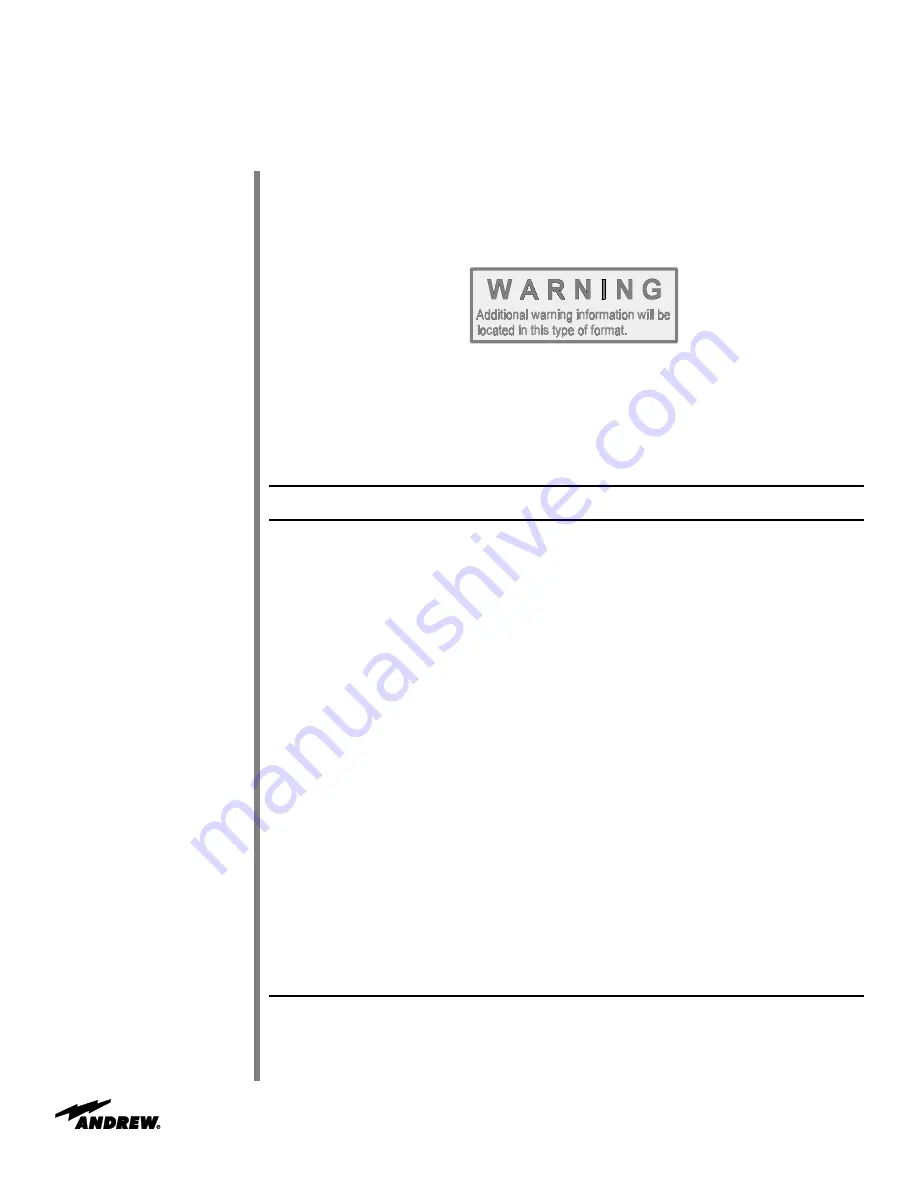
Recommended
Tools
NOTE:
Failure to follow an installation procedure could result in damage to equipment
or personal injury.
Additional warnings will be displayed throughout this manual for your awareness. These
warnings can be identified in warning boxes as shown in the following sample.
Andrew disclaims any liability or responsibility for the results of improper or unsafe
installation, operation, or maintenance practices.
Andrew supplies all appropriate hardware/parts required for the installation of your 3.7-
Meter Earth Station Antenna. All tools necessary for the installation process should be
provided by the installation crew. Andrew recommends the following tools to be used for
a proper installation of the 3.7-Meter Earth Station Antenna.
Tool
Size
Quantity
Open End or Combination Wrenches
5/16 Inch
2
7/16 Inch
2
9/16 Inch
2
7/8 Inch
2
3/4 Inch
2
1/2 Inch
2
1-1/4 Inch
1
Crane
1 Ton Minimum Capacity, extended end
1
Nylon Web Slings (2000 pound breaking strength) 3 Inch by 14 Foot
2
Rope or Cord (2000 pound breaking strength)
50 Foot
1
Shackles
5/8 Inch
2
Ladder
10 Foot Extension
1
Drive Sockets
1/16 Inch
1
9/16 Inch
1
7/8 Inch
1
3/4 Inch
1
1-1/4 Inch
1
Breaker Bar
1/2 Inch
1
Spud Wrenches
1-1/16 Inch
1
1-1/4 Inch
1
Screw Driver
Standard
1
Phillips
1
Allen Wrench
7/64 Inch
1
3/16 Inch
1
1/4 Inch
1
Tape Measure (or other measuring device)
Standard
1
Felt-tip Marker (or other marking device)
Standard
1
Hammer
Standard
1
Rubber Mallet
Standard
1
Pry Bar
Standard
1
Tin Snips
Standard
1
Safety Gloves (each installer)
Standard
1
Table 2-1. Recommended Tools
7
Getting Started