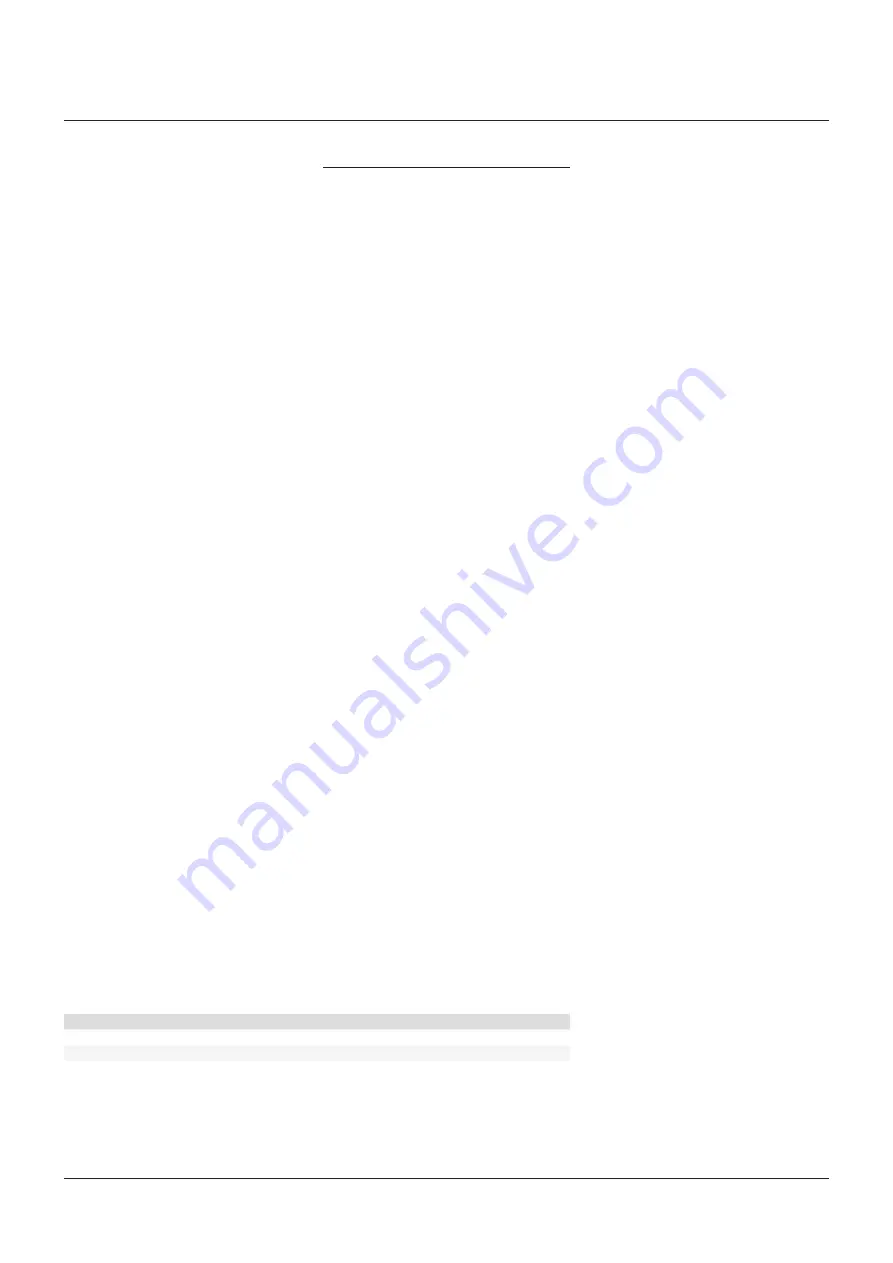
2
Anderson Greenwood
SerieS 5200 POSrV
InstallatIon and MaIntenance InstructIons
1.4 Maintenance
recommended main valve and pilot
maintenance procedures, including pilot set
pressure adjustment and valve assembly
testing, are described in the following
paragraphs. Following these procedures in
a regular pressure relief valve maintenance
program is recommended, to ensure
satisfactory valve performance and provide
optimum service life.
Should the pressure/media requirements of a
pilot operated pressure relief valve be outside
the capabilities of the repair facility, contact
emerson for specific instructions before
starting any maintenance activity.
This manual is provided as a general guide for
the maintenance of the safety valves described
herein. it does not include procedures
covering all valve configurations and variations
manufactured by emerson. The user is advised
to contact emerson or one of our authorized
representatives for assistance with valve
configurations and variations not covered in this
manual.
TAble 1 - dIsC InserT ThreAded hole sIzes
orifice size
Thread size
F, G, H, J, K, L
¼-20 UNC
M, N, P, Q, r, T
⅜-16 UNC
remove the nozzle (3) from the valve body (1).
Although it is possible to recondition the nozzle
seat without removing it from the valve body,
the nozzle must be removed in order to fully
inspect its condition, including measuring
critical dimensions. To remove the nozzle,
turn the valve body over taking care not to
damage the cap studs (15). Turn the nozzle
counterclockwise by using the wrench flats on
the nozzle flange or a nozzle wrench designed
to clamp onto the nozzle flange.
All parts should be inspected visually for
signs of damage, erosion or corrosion. Moving
parts should be inspected for any signs of
galling. Guide iD, piston OD and liner iD
must be measured to verify dimensions per
Table 3, 'internal Parts Critical Dimensions'.
2 MAIn VAlVe MAInTenAnCe
2.1 Main valve disassembly
refer to Figures 1 and 2 for main valve parts
description and location.
remove the pilot valve (B), condensate trap (e),
bracket (16), sense ring (20, if installed),
associated tubing (C) and fittings (D) from the
main valve. Loosen the body drain fitting (17)
from the main valve body (1) and discard the
gasket (22). Loosen the nuts (14) holding the
cap (2) to the body (1). Lift the main valve
cap (2) from the body (1), exposing the liner (7),
piston (6) and guide (5). remove the main valve
internal parts (4 thru 13 and 18) and discard
the organic fiber upper guide gasket (18), the
liner O-ring (11) and the piston O-ring (12). The
stainless steel lower guide gasket (10) and
PTFe wedge ring (13) typically can be cleaned
and re-used.
The disc insert (8) can be removed from the
disc holder (4) by threading a small bolt (see
Table 1 for thread size) into the disc insert (8)
and then pulling on the two parts to separate.
For the valve sizes with N and P orifices, it
would be difficult to pull out the disc insert
by hand. Contact the factory for special
instructions/tool to remove the disc insert from
the disc holder.
1.3 start-up
There must be pressure at the valve inlet (or at
the pilot inlet/sense port for valves with remote
sense) to establish a differential force across
the piston/disc assembly and 'load' it in the
closed position. Pressure must pass through
the pilot and exert force on the top of the piston.
On normal plant start up the valve will close
itself as pressure increases.
in certain circumstances, block valves may be
used under pressure relief valves to isolate
them when maintenance is required. When
putting the safety valve in service, be sure the
block valve is opened fully. if the block valve is
opened after system start up, the safety valve
may vent briefly before the volume above the
piston gets pressurized to close the piston/
disc assembly. Opening the isolation valve very
slowly, at the valve crack point, will introduce
heat slowly to the POSrV and will avoid the
inadvertent lifting of the MV seat.
if measurements are out of range, parts need
to be replaced. Damaged valve parts should
be repaired and need to be replaced if beyond
repair.
Do not remove the pitot tube (21) from the
sense ring (20).