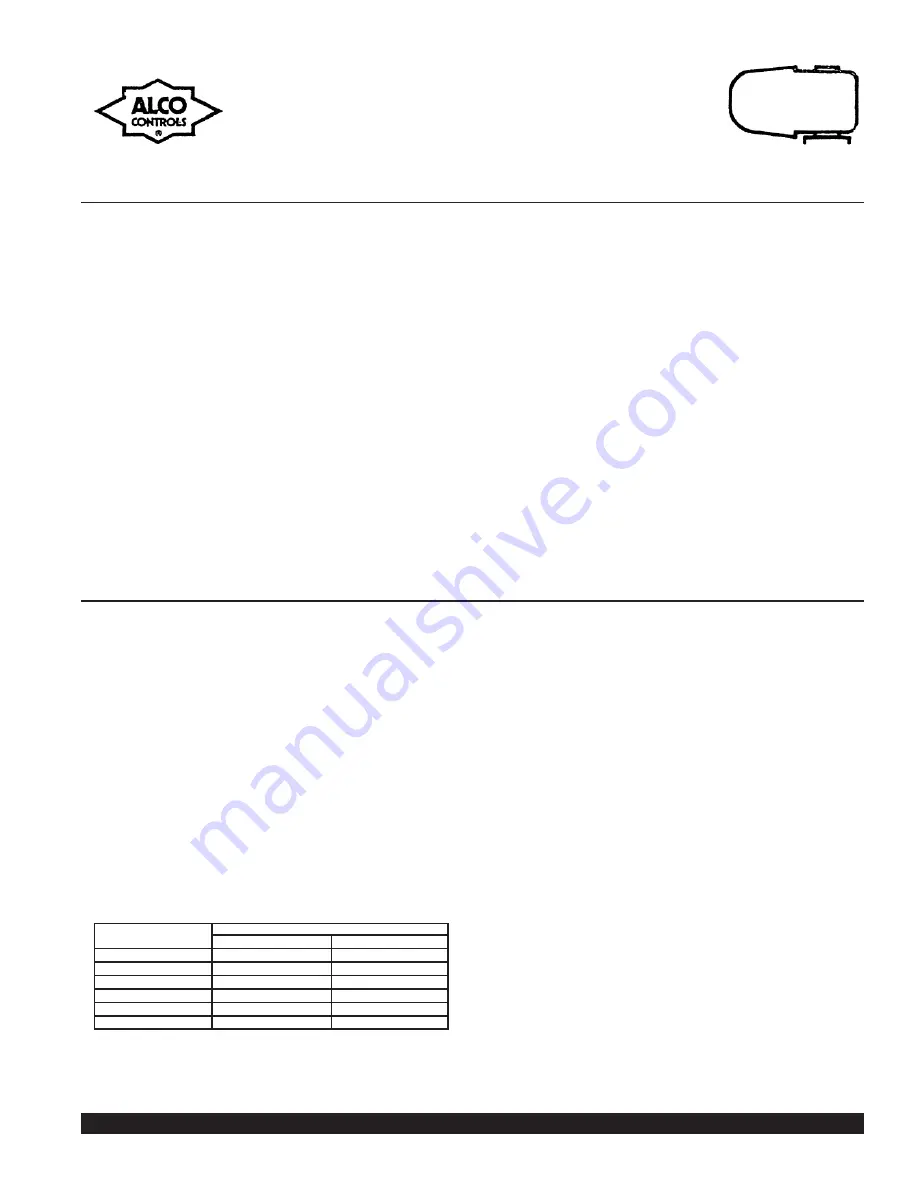
Page 11
American Metal Ware Hot Water Boiler
Read installation instructions- thoroughly. Failure to comply can
result in valve failure or system damage or personal injury.
Do not use solenoid valves on applications or fluid media not
specifically cataloged without prior approval of Alco Engineering
Department.
WARNING: DO NOT USE WITH FLAMMABLE OR EXPLOSIVE
FLUIDS OR GASES. DO NOT USE IN EXPLOSIVE
ATMOSPHERES.
Use on these elements can result in product damage or
personal injury.
Use of solenoid valves on applications not specifically cataloged
can result in valve failure and/or system damage or personal
injury. Do not utilize a solenoid valve on any system where the
system pressure can exceed the safe working pressure of the
valve.
CAUTION:
Do not utilize a solenoid valve as a safety shut off.
Do not exceed MOPD (Maximum Operating Pressure
Differential) or valve may fail to open when energized.
6.
7.
8.
9.
10.
11.
1.
2.
3.
4.
5.
CAUTION: Always disconnect power source and depressurize
the system before working on solenoid valve or system. If the
power disconnect is out-of-sight, lock it in the open position and
tag to prevent unexpected applications of power.
Direction of flow must correspond to flow Direction Schematics.
Before energizing valve, be sure source voltage and frequency
matches that on coil. Do not energize coil unless coil is securely
attached to valve. See Coil Installation Instructions.
Prolonged use in excessive ambient temperature or humidity
may damage coils.
Do not dent or bend or use enclosing tube as lever. A damaged
enclosing tube may result in coil burnout or inoperative valve.
Foreign matter in the valve may result in seat leakage, sticking
open or closed, or coil burnout. To prolong valve life and ensure
system cleanliness use a strainer.
Safety Instructions
ATTENTION: Read carefully before attempting to install,
operate or service your Alco solenoid valve. Retain for
future reference.
For ease of installation, an Alco solenoid valve can be installed in
any position...gravity does not affect its operation.
NOTE:
Although all valves can be operated in any position,
by mounting the valve upright there is less chance of
malfunction caused by the collection of foreign material.
The solenoid coil can be rotated 360
O
for ease of wiring. If possible
do not reduce thelength of the solenoid coil wire leads, so that if it
becomes necessary to remove coil at a later date (for valve cleanout,
etc), wire leads will not have to be disconnected.
To allow for removal of the solenoid coil without removing the valve from
its piping, allow at least 2 inches of clearance above the solenoid.
Be sure valve is installed so that its flow arrow on valve body corre-
sponds to direction of flow through piping.
1.
2.
3.
4.
Before removing coil from valve, disconnect electrical power
source. Failure to do so will cause coil to burn out.
Verify coil type, voltage and frequency. This information appears
on the coil nameplate.
Place coil over the enclosing tube. Coil may be rotated 360
O
for
easy wiring. It is recommended that coil lead connections be
soldered on D.C. and 24V - 50/60 Hz. applications.
Install valve nameplate. Pull tab on valve nameplate and peel off
paper backing to expose adhesive. Stick nameplate on top of coil
housing and press nameplate down firmly. If installing
replacement coil, use valve nameplate supplied with valve. Press
nameplate down firmly.
Install voltage nameplate and coil retainer. Press coil retainer
down firmly to secure coil.
Be sure your wiring conforms to all local and national electric codes.
For dual voltage coils, refer to the wiring schematic label on side
of coil.
The coil circuit of each solenoid valve should be protected by
adequate fuses.
1.
2.
3.
4.
5.
Wiring
1.
2.
3.
WARNING
If not properly grounded, a hazard of electrical shock may exist.
Install and ground unit in compliance with National, state, and local
electrical codes.
Installation
Valve and Solenoid Position
Coil Installation Instructions
FLUID TEMPERATURE RATING F
O
Elastomer
Code
B
P
N
F
T
V
Coil Code
AMG, AMC
180
250
180
180
250
AHG, AHC
385
Identify valve elastomer code and coil code from valve model
number and reference rating from table.
Valves are rated for use on air or other non-hazardous, non-toxic
fluids, water and other aqueous, non-hazardous fluids, and steam.
INSTALLATION AND SERVICE
INSTRUCTIONS
FOR
202CB and 204CD Series
General Purpose Solenoid Valve
53.20.10
May 1983
Supd’s 3-80