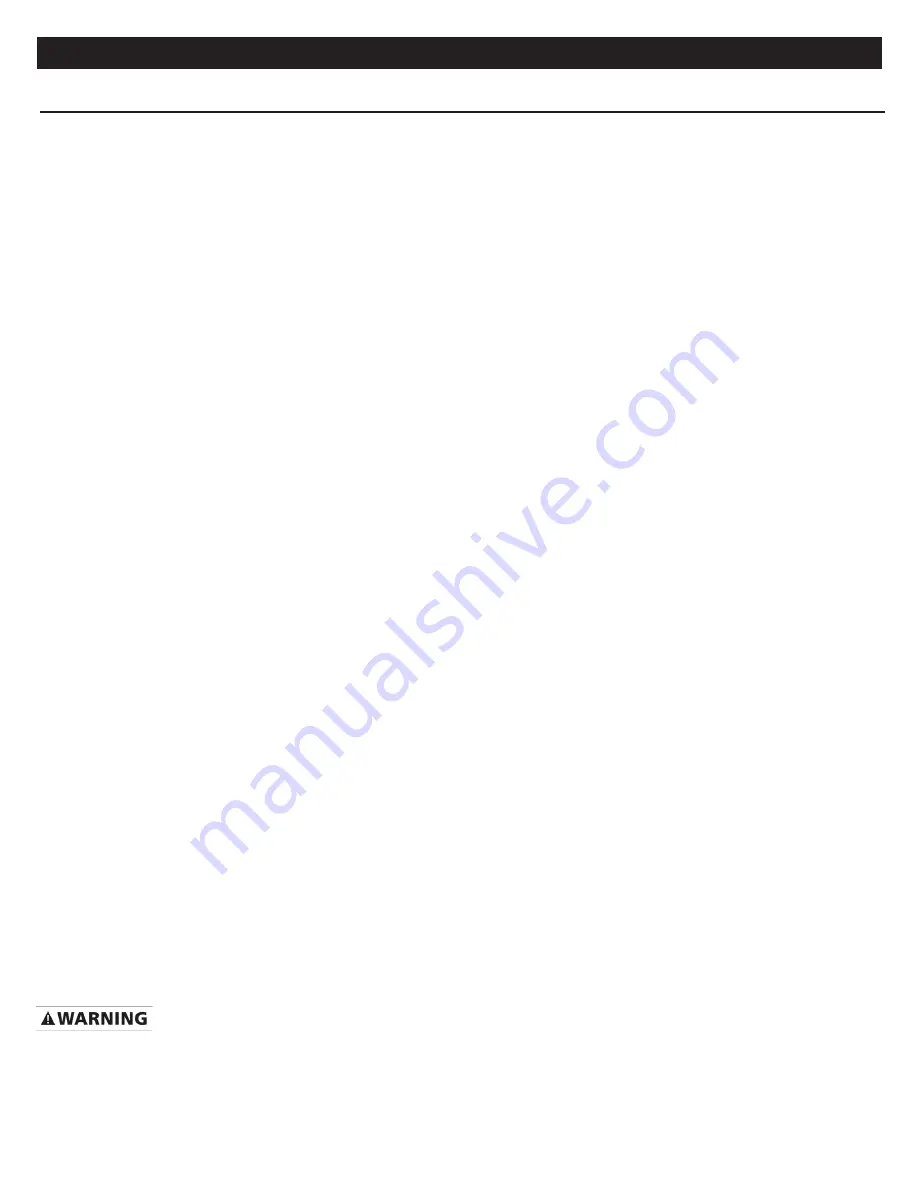
Specifications Information and Repair Parts Manual
25FP Series
25FP-250-00
4
10/2017
25FP Fire Pump Series
MAINTENANCE
Preventative Maintenance
Since pump applications are seldom identical and pump wear is directly
affected by such things as the abrasive qualities, pressure and temperature
of the liquid being pumped, this section is intended only to provide general
recommendations and practices for preventive maintenance. Regardless of
the application, following a routine preventive maintenance schedule will help
assure trouble free performance and long life from your pump.
Record keeping is an essential component of a good preventive maintenance
program. Changes in suction and discharge gauge readings (if so equipped)
between regularly scheduled inspections can indicate problems that
can be corrected before system damage or catastrophic failure occurs. The
appearance of wearing parts should also be documented at each inspection for
comparison as well. Also, if records indicate that a certain part (such as the shaft
seal) fails at approximately the same duty cycle, the part can be checked and
replaced before failure occurs, reducing the unscheduled down time. For new
applications, a first inspection of wearing parts at 250 hours will give insight into
the wear rate for your particular application. Subsequent inspections should be
performed at regular intervals. Critical applications should be inspected more
frequently.
•
General condition (temperature, unusual noises or vibrations, cracks,
leaks, loose hardware, etc)…DAILY
•
Pump performance (gauges, speed, flow)…DAILY
•
Impeller wear rings (excessive wear, poor performance)...SEMI-
ANNUALLY 25FP Fire Pump Series
•
Mechanical shaft seal (excessive wear, heat damage, leakage, etc)…
SEMI-ANNUALLY
•
Discharge check valve/gasket (excessive wear)…SEMI-ANNUALLY
•
Engine lubrication – See Engine Manufacturer’s Service Manual. Inspect,
clean, and replace components as needed.
PUMP/SEAL DISASSEMBLY & REASSEMBLY
Review all SAFETY information provided in this manual and pump
General Safety Manual.
Follow the instructions on all tags, labels and decals attached to the
pump.
This pump requires little service. When it becomes necessary to inspect or
replace the wearing parts, follow these instructions that are keyed to the repair
part lists and repair part explosions.
This manual will alert personnel to known procedures that require special
attention, could damage equipment or be dangerous to personnel. However,
this manual cannot possibly anticipate and provide detailed precautions for
every situation that might occur during maintenance of the unit. Therefore, it is
the responsibility of the owner/maintenance personnel to ensure that only safe,
established shop procedures are used and that any procedures not addressed
in this manual are performed only after establishing that neither personal safety
nor pump integrity are compromised by such practices.
Before attempting to service the pump, switch off the engine ignition and
remove the spark plug or take other precautions to ensure that it will
remain inoperative. Close all valves in the discharge lines.
Before attempting to service the pump:
•
Familiarize yourself with this manual.
•
Shut down the engine and remove the spark plug wires to ensure that the
pump will remain inoperative.
•
Allow the pump to completely cool if overheated.
•
Check the temperature before opening any covers, plates or plugs.
•
Close the discharge valve.
•
Vent the pump slowly and cautiously.
•
Drain the pump.
For engine disassembly and repair, consult the literature supplied with the
engine or contact your local engine service representative.
PUMP DISASSEMBLY
First Step:
1.
Disconnect the priming vacuum hose (C31) female SAE fitting (C34) from
the male SAE fitting (B33) installed in the ball valve (B32).
2. Remove the casing drain plug (B9) and drain the pump casing. Clean and
reinstall the plug.
Remove Casing:
For access to the impeller (B15) and shaft seal assembly (B19 & B20):
1. Remove the nuts (B12) securing the pump casing (B8) to the intermediate
(B3).
2. Remove the casing from the intermediate.
3. Remove the casing o-ring (B21) and clean all mating surfaces.
Inspect the casing wear ring/inlet (B13) for excessive wear or damage. The
wear ring is secured in the casing with a press fit. If replacement is required ,
remove existing worn ring and replace with a new replacement ring. Be careful
not to damage the casing ring bore when removing existing ring.
Remove Discharge Check Valve Body:
1. Remove the nuts (B27) and separate the check valve body (B24) from
the pump casing.
2.
Pull the flange gasket (B22) from the flange studs (B26) and pull the
check valve arm (B25) from the check valve body.
Clean the mating surfaces of both flanges and inspect all parts for wear or
damage.
Remove Impeller:
To remove the impeller (B15):
1. Insert a steel bar or drift pin between the vanes and turn the impeller
in a counter-clockwise direction (when facing the impeller) while holding
the engine crankshaft stationary. Be careful not to damage the impeller
vanes.
Seal Removal and Disassembly:
1. Remove the impeller shims if so equipped, not all pumps will require
shims. Tie and tag the shims or measure and record their thickness for
ease of reassembly.
2. Remove the seal spring and then slide the shaft sleeve (B16) and rotating
portion (B19) of the seal off the engine shaft as a unit.
3.
Slide the rotating portion of the seal off the sleeve.
4. Remove the stationary seal ring (B20) from the intermediate, see following
section.
Summary of Contents for 25FP10YR
Page 15: ......
Page 16: ...www amtpump com...