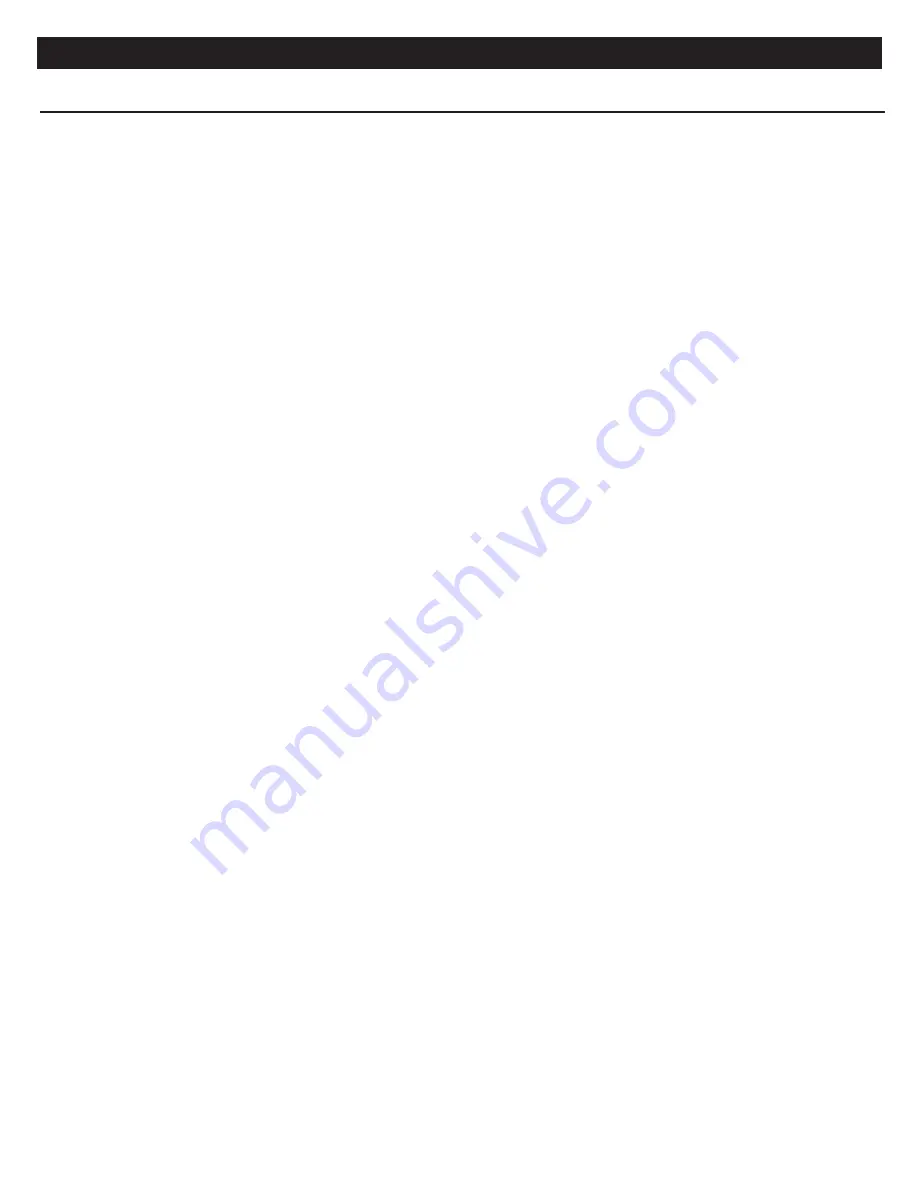
Specifications Information and Repair Parts Manual
25FP Series
25FP-250-00
2
10/2017
Fuel Tank Frame Assembly: [25FP23AR]
1. Position fuel tank frame (A32) on roll frame.
2. Align holes in tank frame ears with holes in roll frame tubes and cross
member.
3. Install mounting bolts (A33 & A34) and nuts (A35) securing tank frame to
roll frame.
4. Install fuel line from bottom of tank to fuel pump on engine with hose
clamp provided.
5. Install purge line from top of tank to engine purge line with connector and
hose clamp.
INSTALLATION
Review all safety information located in pump safety manual.
Follow the instructions on all tags, labels and decals attached to the
pump.
Since pump installations are seldom identical, this section offers only general
recommendations and practices required to inspect, position and arrange the
pump and piping.
Most of the information pertains to a standard static lift application where the
pump is positioned above the free level of liquid to be pumped.
If installing in a flooded suction application where the liquid is supplied to the
pump by gravity or under pressure, some of the information such as mounting,
line configuration and priming must be tailored to the specific application. Be
sure to limit the incoming pressure if required, so the maximum casing pressure
does not exceed 180 psi (1240 kPa).
Pre-Installation Inspection
The pump assembly was inspected before shipment from the factory. Before
installation, inspect the pump for damage, which may have occurred during
shipment or in storage.Check as follows:
•
Inspect pump casing for cracks, dents, damaged threads and other
obvious damage.
•
Check for and tighten any loose fasteners.
•
Carefully read all hang tags, labels and markings on the unit. Follow the
instructions indicated.
•
Check oil level in engine. Follow manufacturer’s recommendations listed
in engine manual.
•
If unit has been stored for more than 12 months, replace engine oil.
Drain any fuel and replace with fresh fuel.
•
Check condition of suction strainer, clean if clogged with debris.
Positioning Pump
This pump is light-weight. Pump/engine is mounted in a roll frame that has (4)
four lifting handles built in. Handle has (2) two pins installed. The pivot pin goes
through handle end plates and directly through frame tube. Second is the lock
pin, it goes through handle end plates only.
To raise and lower handles:
•
Remove cotter from lock pin end.
•
Remove lock pin.
•
Swing handle tube up perpendicular to frame tube.
•
Install lock pin, fix with cotter.
•
To lower handle remove lock pin, swing handle down, reinstall lock pin
Lift and carry pump/engine/battery only with handles. Remove suction and
discharge lines and all accessories from pump before lifting.
25FP Fire Pump Series
Mounting
Locate the pump in an accessible area as close as practical to the liquid being
pumped.
Pump should be leveled if possible by shimming under rubber feet. For proper
pump/engine operation unit should be within 15° of level. Continuous operation
outside this limit may cause engine/pump damage.
System Piping/Hose
Flow through the system is reduced by increased suction lift, increased
discharge elevation or discharge nozzle pressure and increased friction losses.
•
Keep suction and discharge lines as short and direct as possible to reduce
friction losses. If elbows are necessary in discharge line, use long-radius
type, when possible.
•
Do not operate with coiled-up suction or discharge hose.
•
Do not use valves in the suction line, unless absolutely necessary.
Suction Lines
The suction line must be as short and direct as possible. When operating pump
under a suction lift condition:
•
To avoid air pockets which could affect pump priming, the line must always
slope upward to the pump from the liquid source. If the line slopes down at
any point along the suction run air pockets will be created.
•
Hose or pipe size must match pump suction size.
•
The maximum vertical lift cannot exceed 20 feet (6.1 meters).
•
If hose is used for the suction line, it must be the rigid wall reinforced type
to prevent collapse under suction.
•
Fittings are not recommended in the suction line.
Strainers
Use a suction strainer with ¼” maximum diameter holes on end of suction
line. A suction strainer will help remove large solids that could clog the pump
impeller and casing.
Discharge Lines
Use hose or piping that is rated above the maximum system line pressure.
To reduce friction head, keep line as short and direct as possible. Make
minimum use of elbows and fittings, since those two items substantially
increase friction loss in the discharge line.
Do not terminate the discharge line at a level lower than that of the liquid being
pumped unless a siphon breaker is used in the line. Otherwise, a siphoning
action causing damage to the pump could result.
Valves
A check valve in the discharge is normally recommended, but it is not necessary
in low discharge head applications.
If a throttling valve is desired in the discharge line, use a valve as large as the
largest pipe to minimize friction losses. Never install a throttling valve in the
suction.
With high discharge heads, it is recommended that a throttling valve and a
system check valve be installed in the discharge line to protect the pump from
excessive shock pressure and reverse rotation when it is stopped.
Summary of Contents for 25FP10YR
Page 15: ......
Page 16: ...www amtpump com...