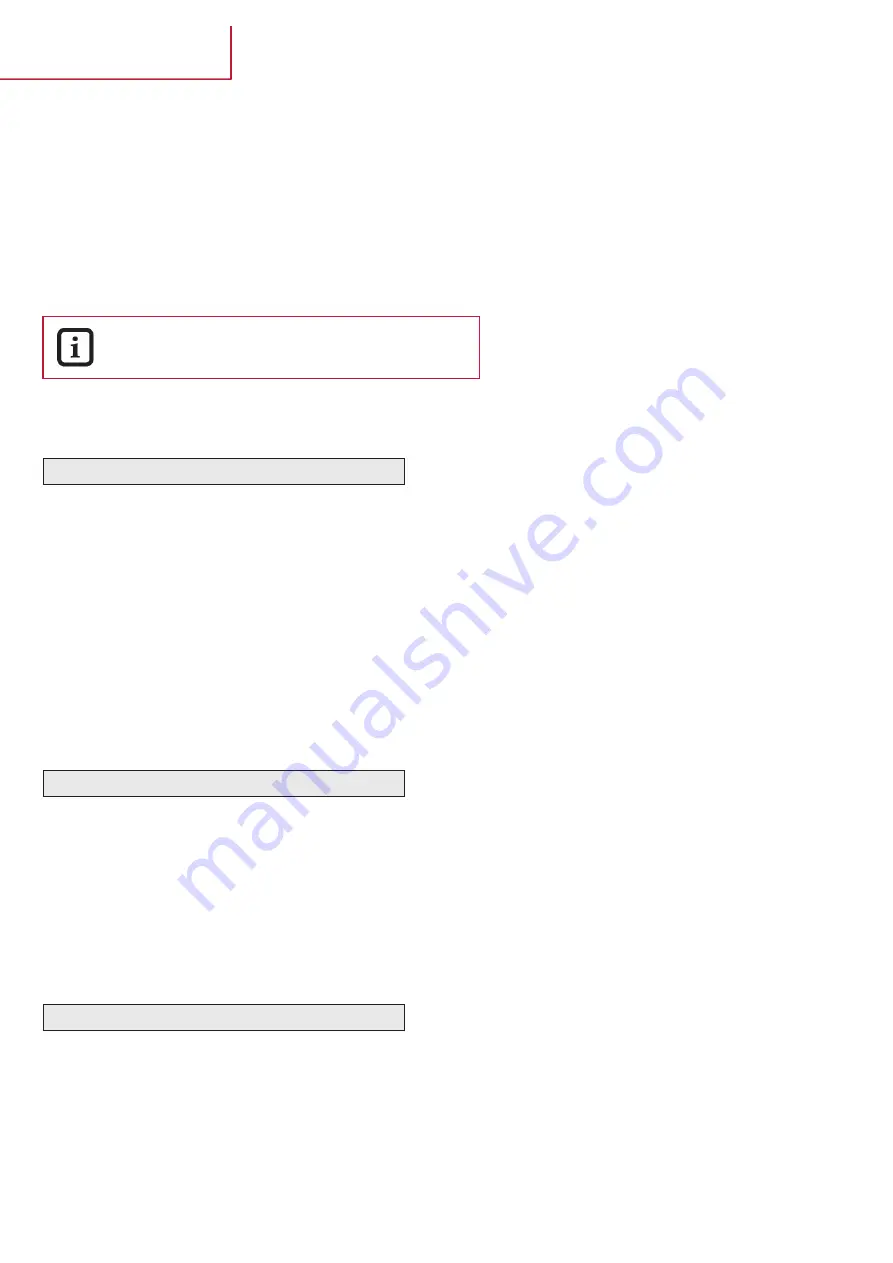
Temposonics
®
MH Digital
Operating Manual
I
14
I
7. CAN Bus protocols
The ISO 11898 international standard CAN bus (Controller Area Network) is a machine level, open field bus for fast serial data transfer between
a central process control system (master) and decentralized intelligent field instruments (slaves). Various protocols, which have been developed
for a variety of applications and by different user groups can be used for data transfer.
Depending on order, Temposonics
®
MH sensors support the following protocols: CANopen, CANopen Safety or SAE J1939. The selected config-
uration affects the integration into the network and the operating characteristics of the sensor. According to the specific version, the following
commissioning and control procedure is required.
8. System description and modes of operation
CANopen
The CANopen version of the Temposonics
®
MH sensor is suitable
for operation as a slave in CAN bus networks using the CiA Stan-
dard DS 301 V3.0 data protocol. The protocol corresponds to the
DS 406 V3.1 encoder profile. The sensor is directly connected to
the bus, thus representing a node in the bus system.
Four different modes of operation that correspond to the states
defined in the CANopen standard are used. Initiated by the control-
ler, these network modes are:
CANopen Safety
For safety-relevant applications, the CANopen safety protocol (EN 50325-5) has been specified as a further development of CANopen. The pro-
tocol corresponds to CiA standard DS 304. Temposonics
®
sensors with CANopen safety implementation are certified according to SIL2 (IEC/EN
61508) and can be used in safety-critical areas. Fundamentally, the protocol is based on the CANopen protocol, however, only certified compo-
nents may be used.
The protocol enables safety oriented devices to be used together with devices that aren‘t safety-oriented in CANopen network. In this way, reli-
able control systems similar to those realized in conventionally wired technology can be implemented. For this purpose, safety-critical data is
transmitted redundantly.
SAE J1939
SAE J1939 is a multi-master protocol developed especially for applications in the mobile field. The specification has been developed by the Soci-
ety of Automotive Engineers and is used for commercial and conveyor vehicles as well as for construction, agricultural and forestry machines.
A network consists of various ECUs (Electronic Control Units), each of which is able to control several CAs (Controller Applications). Messages
are addressed to a CA. After starting the operation, automatic assignment of the bus sharing units takes place. When it has been completed, the
CAN bus sharing units are fully operable.
Initialization:
Sensor starting phase. The sensor undergoes
hardware initialization and loads the standard configuration
which has been saved previously.
Pre-Operational:
In this mode, the sensor can be configured via
the CAN bus.
Operational:
In this mode of operation, the sensor sends process
data. The sensor loads measurement information onto the CAN
bus.
Stopped:
When this mode has been activated, the sensor stops
communicating and waits for further commands.
Please take notice of the following programming instructions:
901 491 SAE J1939, 901 492 CANopen Safety, 901 493 CANopen