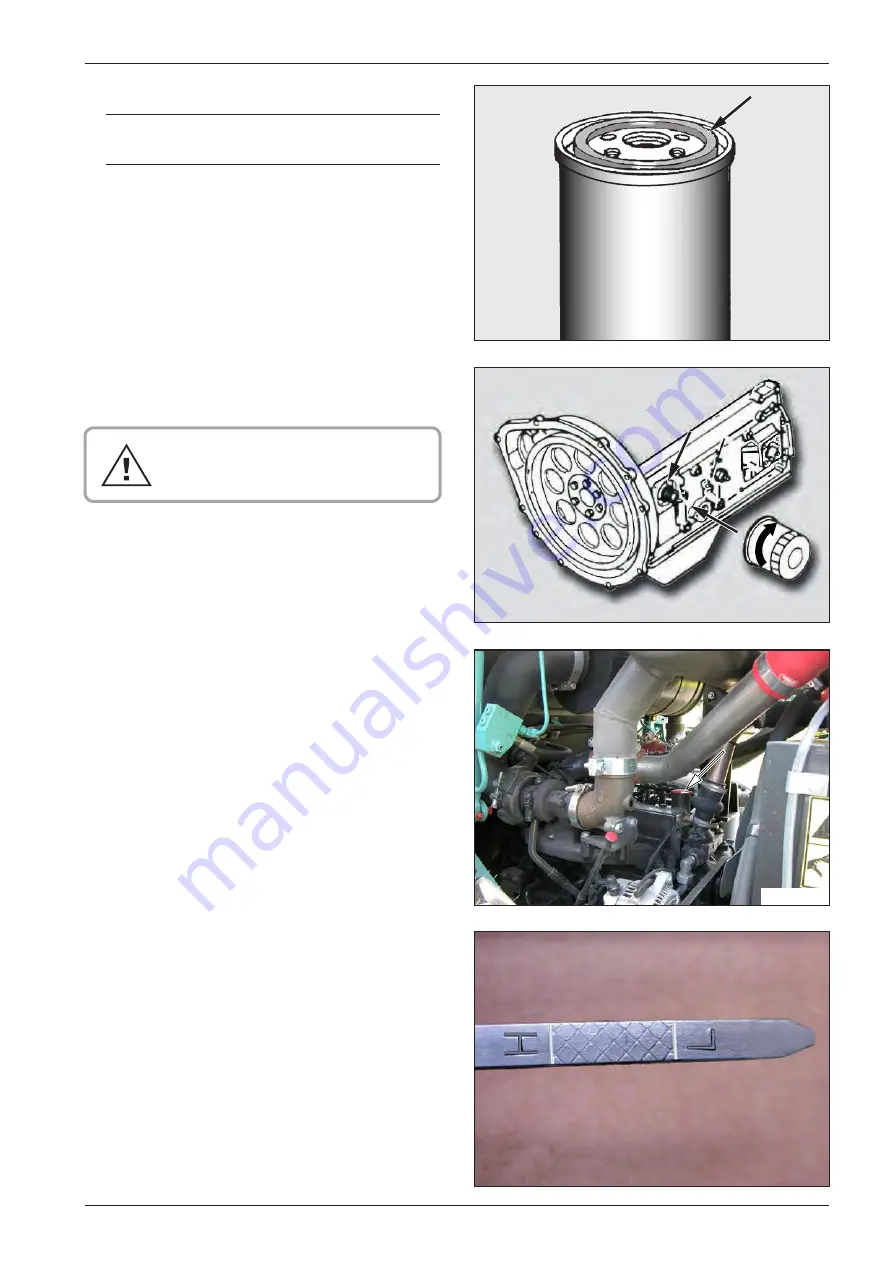
115
ASC 70
396203B
396222
396246
396247
MAINTENANCE MANUAL
• Clean the contact surface for filter gasket. Install the filter
and tighten properly with your hand.
Do NOT overtighten the filter, its thread
and gasket may get damaged.
• Use filler neck to fill the engine.
• Fill oil to the upper division line of H dipstick. The oil filling
is of 7 l (7.4 qt). The amount between division lines L and H
is 1,5 l (1.6 qt).
• Spread oil over the gasket of new filter.
Engine oil filter
Order number: 4-9501000307
Summary of Contents for ASC 70
Page 2: ......
Page 4: ...iv ASC 70...
Page 12: ...8 ASC 70...
Page 13: ...9 ASC 70 SPECIFICATION MANUAL 1 SPECIFICATION MANUAL ASC 70 Cummins Tier 3...
Page 22: ...18 ASC 70 Notes...
Page 23: ...19 ASC 70 OPERATION MANUAL 2 OPERATION MANUAL ASC 70 Cummins Tier 3...
Page 24: ...20 ASC 70...
Page 97: ...93 ASC 70 OPERATION MANUAL Notes...
Page 98: ...94 ASC 70 Notes...
Page 99: ...95 ASC 70 MAINTENANCE MANUAL 3 MAINTENANCE MANUAL ASC 70 Cummins Tier 3...
Page 100: ...96 ASC 70...
Page 158: ...154 ASC 70...
Page 164: ...160 ASC 70 3 8 Annexes...
Page 179: ...175 ASC 70 MAINTENANCE MANUAL Notes...
Page 180: ...176 ASC 70 3 8 Annexes Notes...
Page 181: ...177 ASC 70 MAINTENANCE MANUAL Notes...
Page 182: ...178 ASC 70 3 8 Annexes Notes...
Page 183: ......