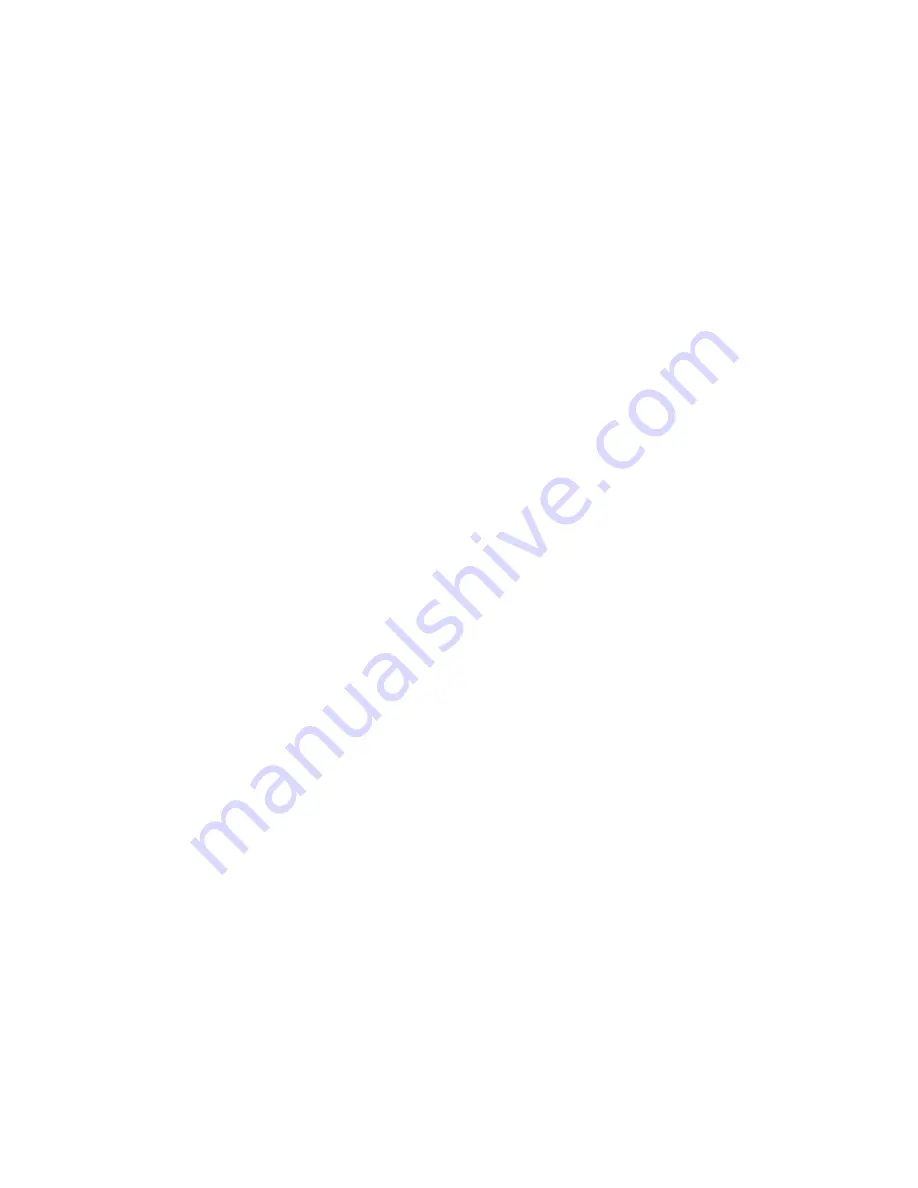
Contents | xi
Product Damage Precautions
Use Proper Power Source
Do not operate this product from a power source that applies more than the
voltage specified.
Do Not Operate with Suspected Failures
If you suspect there is damage to this product, have it inspected by qualified
service personnel.
Use Caution When Lifting
Use caution when lifting the analyzer from its crate.
Use Proper Attire
Equipment is hot, user should wear protective groves while handling the
equipment.
Summary of Contents for Thermox WDG-V UOP
Page 34: ...2 6 Thermox WDG V UOP IECEx ATEX This page intentionally left blank...
Page 65: ...AMEVision Display Installation Guide 4 5 Customer I O Connections...
Page 68: ...4 8 Thermox WDG V UOP IECEx ATEX This page intentionally left blank...
Page 80: ...5 12 Thermox WDG V UOP IECEx ATEX This page intentionally left blank...
Page 96: ...6 16 Thermox WDG V UOP IECEx ATEX This page intentionally left blank...