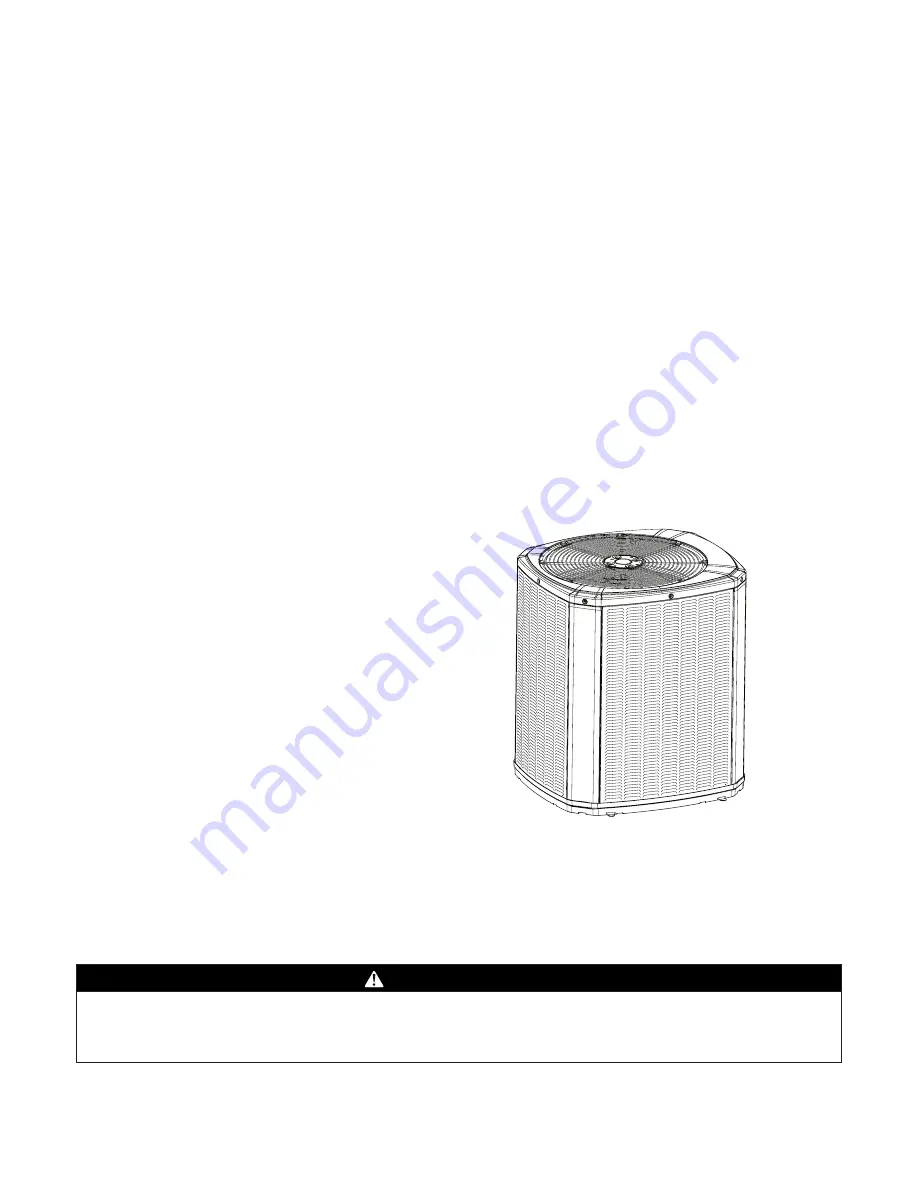
Installer’s Guide
April 2020
88-M4PW004-1B-EN
SAFETY WARNING
Only qualified personnel should install and service the equipment. The installation, starting up, and servicing of heating, ventilating,
and air-conditioning equipment can be hazardous and requires specific knowledge and training. Improperly installed, adjusted or
altered equipment by an unqualified person could result in death or serious injury. When working on the equipment, observe all pre-
cautions in the literature and on the tags, stickers, and labels that are attached to the equipment.
M4HP6018A1000A
M4HP6024A1000A
M4HP6030A1000A
M4HP6036A1000A
M4HP6042A1000A
M4HP6048A1000A
M4HP6060A1000A
Note:
“Graphics in this document are for representation only.
Actual model may differ in appearance.”
Split System Heat Pump
M4HP6