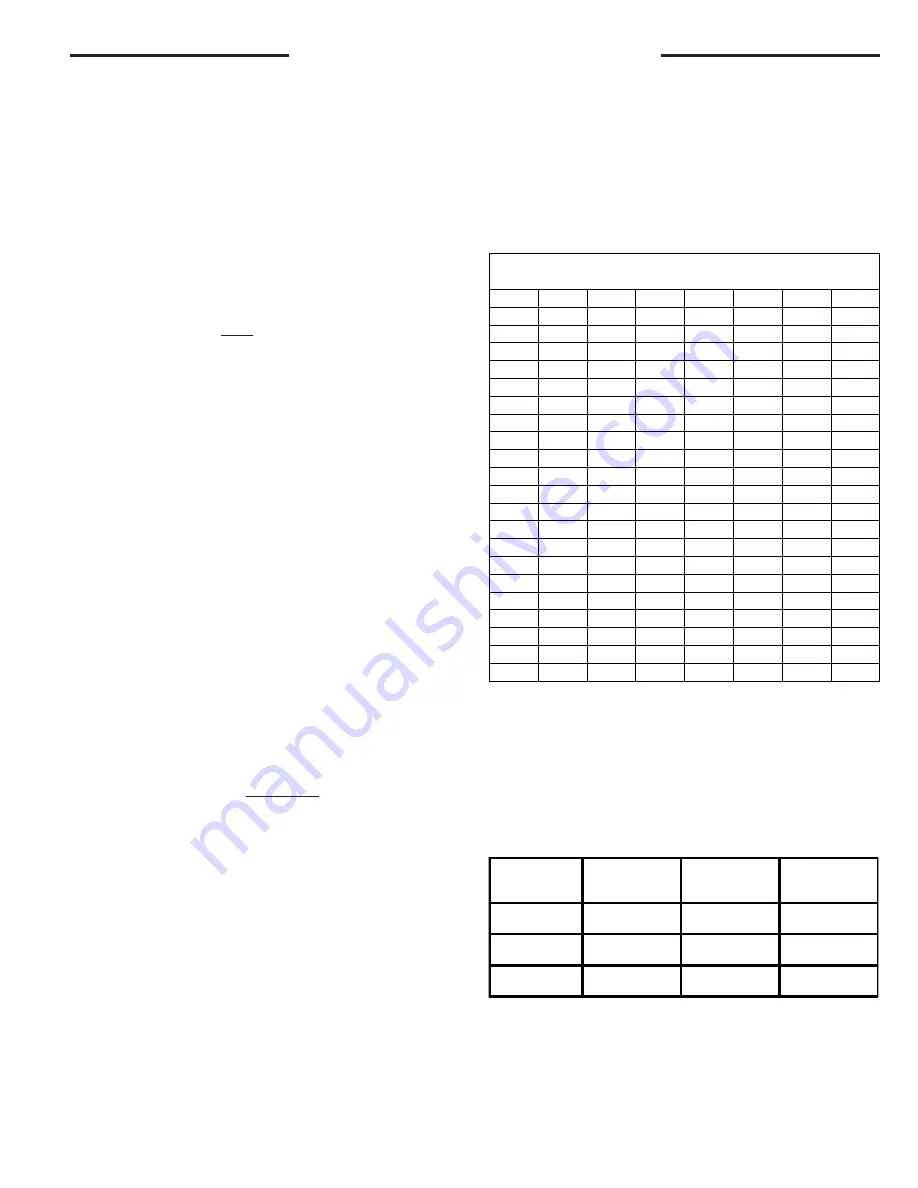
Dwg. No. X664209 P01
Page 15
FIRING RATE SELECTION
GAS FLOW IN CUBIC FEET PER HOUR
2 CUBIC FOOT DIAL
Sec.
Flow
Sec.
Flow
Sec.
Flow
Sec.
Flow
8
900
29
248
50
144
82
88
9
800
30
240
51
141
84
86
10
720
31
232
52
138
86
84
11
655
32
225
53
136
88
82
12
600
33
218
54
133
90
80
13
555
34
212
55
131
92
78
14
514
35
206
56
129
94
76
15
480
36
200
57
126
96
75
16
450
37
195
58
124
98
73
17
424
38
189
59
122
100
72
18
400
39
185
60
120
104
69
19
379
40
180
62
116
108
67
20
360
41
176
64
112
112
64
21
343
42
172
66
109
116
62
22
327
43
167
68
106
120
60
23
313
44
164
70
103
124
58
24
300
45
160
72
100
128
56
25
288
46
157
74
97
132
54
26
277
47
153
76
95
136
53
27
267
48
150
78
92
140
51
28
257
49
147
80
90
144
50
TABLE 3
All units are capable of firing at a low or high rate. Check the unit
name-plate, to verify the firing rate of the unit as shipped from the
factory.
If the other input rate is desired, the conversion is made as follows:
1. Be sure the unit disconnect is open.
2. Be sure the gas valve is closed.
3. Remove furnace access panel.
4. Remove the presently installed gas orifices and replace with
the new gas orifices from the low fire kit. The orifices should extend
1/4 inch out of the manifold for burner support.
5. For low fire operation an OUTLET FLUE RESTRICTOR
(packed in the low fire kit) must be installed (see Figure 16 on page
14). For high fire operation on a few models a different OUTLET
FLUE RESTRICTOR may have been required.
6. Reinstall the furnace access panel.
7. Open the gas valve.
8. Close the unit disconnect.
9. Follow the heating cycle instructions to test unit’s function.
10. Mark an “X” below the new input column on unit nameplate.
Attach conversion label to the unit below the nameplate.
NOTE: Do not convert to high fire when the units are applied above
2000 feet above seal level.
INPUT CHECK AND ADJUSTMENT
1. Make sure all gas appliances are off except the furnace.
2. Clock the gas meter with the furnace operating (determine the
dial rating of the meter) for one revolution.
3. Match the “Sec” column in the gas flow (in cfh) Table 3 with the
time clocked.
4. Read the “Flow” column opposite the number of seconds
clocked.
5. Use the following factors if necessary.
For 1 Cu. Ft. Dial Gas Flow CFH =
Chart Flow Reading / 2
For 1/2 Cu Ft. Dial Gas Flow CFH =
Chart Flow Reading / 4
For 5 Cu. Ft. Dial Gas Flow CFH =
10X Chart Flow Reading / 4
6. Multiply the final figure by the heating value of the gas obtained
from the utility company and compare to the nameplate rating.
This must not exceed the nameplate rating.
7. Changes can be made by adjusting the manifold pressure.
a. Attach a manifold pressure gauge.
HIGH ALTITUDE INSTALLATION
Unit nameplate ratings are based on equipment operation from sea
level to 2000 feet elevation above sea level. If the unit installation
is from 2000 - 4500 feet elevation, it will be necessary to change the
burner orifices to the noted sizes, (ref. National Fuel Gas Code, sec
8.1.2, Appendix F, Table F4).
b. Remove the slot screw on top of the gas valve for 1st stage
manifold pressure adjustment.
c. Turn the adjustment nut IN to increase the gas flow rate, and
OUT to decrease the gas flow rate using a 3/32" hex wrench.
GAS
TYPE
MANIFOLD
PRESSURE
( in. W.C. )
ORIFICE SIZE
0 - 2000 ft
ORIFICE SIZE
2000 - 4500 ft
NATURAL
( high input )
3.3
42
*
43
NATURAL
( low input )
3.3
44
45
PROPANE
10.0
54
55
*
FACTORY SHIPPED