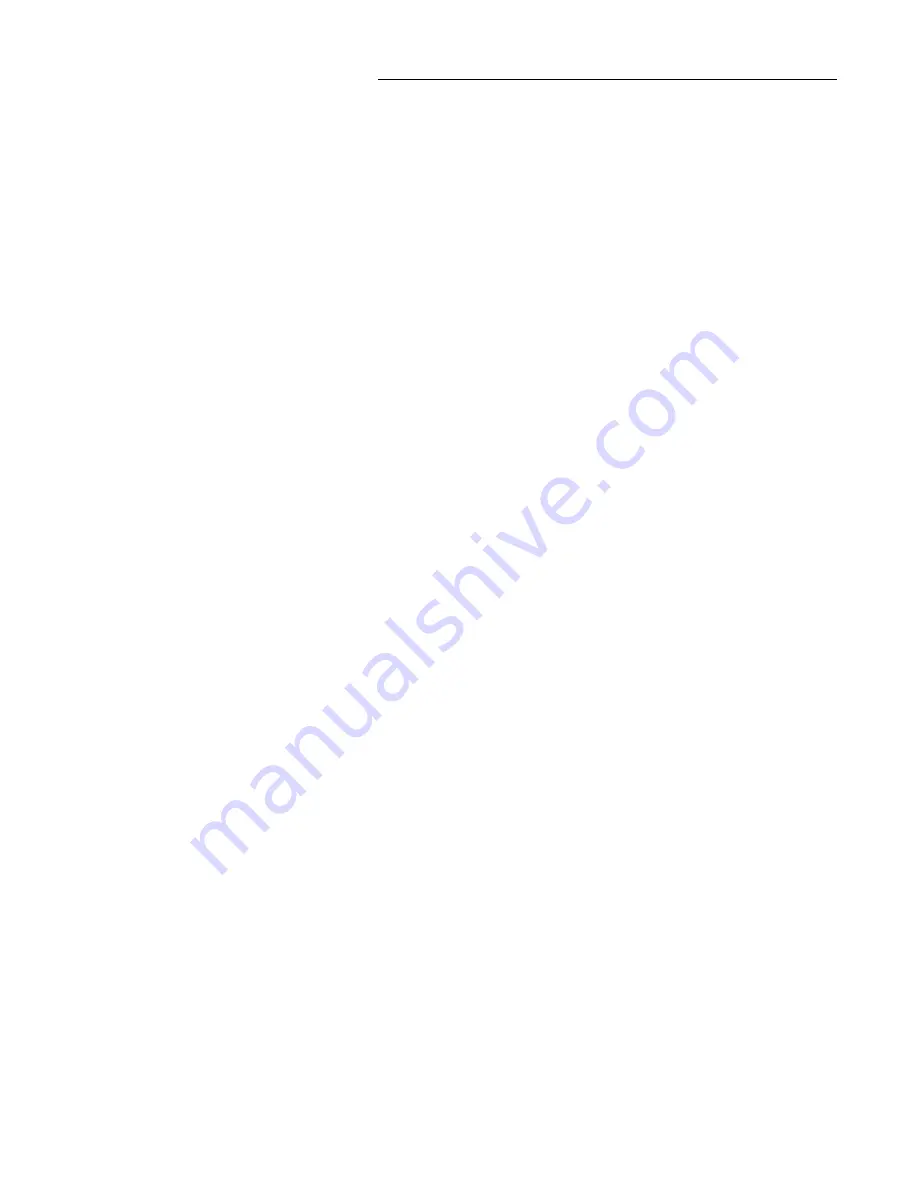
5
General Information
Active - AFF (Active Fan Failure) When the fan proving
switch is connected across terminals J5-3 & J5-4 on the
unit economizer module (UEM), if air flow through the unit
is not proven by the differential pressure switch (factory
set point 0.05 “ w.c.) within 40 seconds nominally, the
UCP will shut off all mechanical operations, lock the sys-
tem out, send a diagnostic to ICS, and the SERVICE LED
will flash. The system will remain locked out until a reset
is initiated either manually or through ICS.
Clogged Filter Switch (Optional)
The unit mounted clogged filter switch monitors the pressure
differential across the return air filters. It is mounted in the fil-
ter section and is connected to the UCP. A diagnostic SER-
VICE signal is sent to the remote panel if the pressure differ-
ential across the filters is at least 0.5" w.c.. The contacts will
automatically open when the pressure differential across the
filters decreases to approximately 0.4" w.c.. The switch dif-
ferential can be field adjusted between 0.17" w.c. to 5.0" w.c.
± 0.05" w.c. to correspond to the desired dirty filter condition.
The clogged filter output is energized when the supply fan is
operating and the clogged filter switch has been closed for at
least 2 minutes. The system will continue to operate regard-
less of the status of the filter switch.
Compressor Disable (CPR1/2)
This input incorporates the low pressure control (LPC) of
each refrigeration circuit and can be activated by opening a
field supplied contact installed in series with the LPC.
If this circuit is open before the compressor is started, the
compressor will not be allowed to operate. Anytime this cir-
cuit is opened for 5 continuous seconds during compressor
operation, the compressor for that circuit is immediately
turned “Off”. The compressor will not be allowed to restart for
a minimum of 3 minutes should the LPC close.
If four consecutive open conditions occur during the first
three minutes of operation, the compressor for that circuit will
be locked out, a diagnostic communicated to the remote
panel (if installed), and a manual reset will be required to re-
start the compressor.
Low Pressure Control
This input incorporates the low pressure and can be acti-
vated by opening a field supplied contact.
Anytime this circuit is opened for 5 continuous seconds, the
compressor for that circuit is turned off immediately. The
compressor will not be allowed to restart for a minimum of 3
minutes.
If four consecutive open conditions occur during the first
three minutes of operation, the compressor will be locked
out, a diagnostic communicated to ICS
TM
if applicable, and a
manual reset will be required to restart the compressor.
High Pressure Control
The high pressure controls are wired in series between the
compressor outputs on the UCP and the compressor
contactor coils. If the high pressure control switch opens, the
UCP senses a lack of current while calling for cooling and
locks the compressor out.
On dual circuit units, if the high pressure control opens, the
compressor on the affected circuit is locked out. A manual re-
set for the affected circuit is required.
Power Exhaust Control (Optional)
The power exhaust fan is started whenever the position of
the economizer dampers meets or exceed the power ex-
haust set point when the indoor fan is on.
The set point panel is located in the return air section and is
factory set at 25%.
Lead/Lag Control (Dual Circuit Only)
Lead/Lag is a selectable input located on the UCP. The UCP
is configured from the factory with the Lead/Lag control dis-
abled. To activate the Lead/Lag function, simply cut the wire
(52F) connected to J1-7 at the UCP. When it is activated,
each time the designated lead compressor is shut off due to
the load being satisfied, the lead compressor or refrigeration
circuit switches. When the UCP is powered up, i.e. after a
power failure, the control will default to the number one cir-
cuit compressor.
Remote Zone Sensor (BAYSENS016A)
This bullet type temperature sensor can be used for; outside
air (ambient) sensing, return air temperature sensing, supply
air temperature sensing, remote temperature sensing (un-
covered. Wiring procedures vary according to the particular
application and equipment involved. Refer to the unit’s wiring
diagrams for proper connections.
Remote Zone Sensor (BAYSENS017B)
This electronic sensor can be used with BAYSENS006B,
008B, 010B, 019A, 020A, or 021A Remote Panels. When
this sensor is wired to a BAYSENS019A or BAYSENS020A
Remote Panel, wiring must be 18 AWG Shielded Twisted
Pair (Belden 8760 or equivalent). Refer to the specific Re-
mote Panel for wiring details.