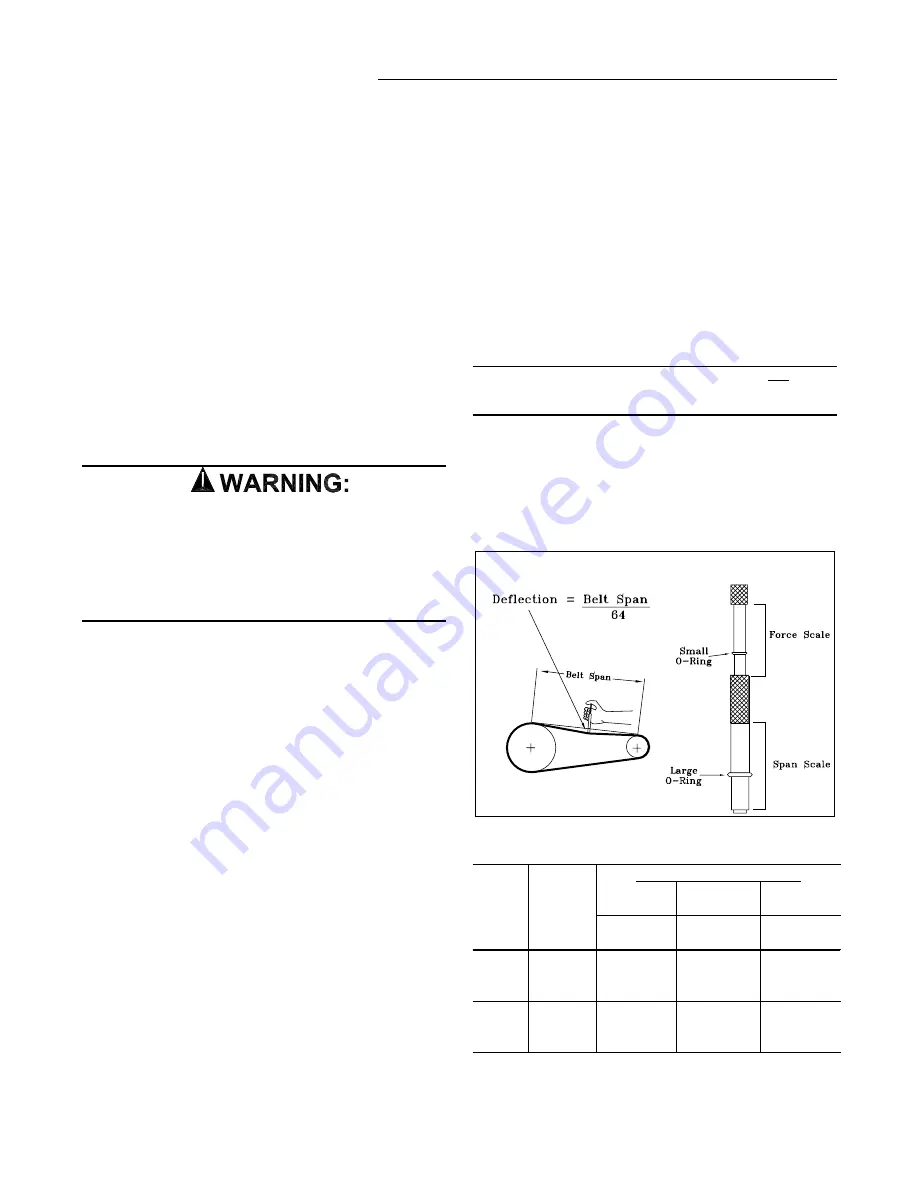
27
Final System Setup
After completing all of the pre-start and start-up procedures
outlined in the previous sections (i.e., operating the unit in
each of its Modes through all available stages of cooling &
heating), perform these final checks before leaving the unit:
[ ] Program the Night Setback (NSB) panel (if applicable) for
proper unoccupied operation. Refer to the programming
instructions for the specific panel.
[ ] Verify that the Remote panel “System” selection switch,
“Fan” selection switch, and “Zone Temperature” settings
for automatic operation are correct.
[ ] Inspect the unit for misplaced tools, hardware, and debris.
[ ] Verify that all exterior panels including the control panel
doors and condenser grilles are secured in place.
[ ] Close the main disconnect switch or circuit protector
switch that provides the supply power to the unit’s termi-
nal block or the unit mounted disconnect switch.
HAZ A R D O U S V O L TA G E
R O T A T I N G P A R T S !
UNIT STARTS AUTOMATICALLY
Make sure all personnel are standing clear of the unit
before proceeding. The system components will start
when the power is applied.
Fan Belt Adjustment
The fan belts must be inspected periodically to assure
proper unit operation.
Replacement is necessary if the belts appear frayed or worn.
Units with dual belts require a matched set of belts to ensure
equal belt length.
When removing or installing the new belts, do not stretch
them over the sheaves. Loosen the belts using the belt
tension adjustment bolts on the motor mounting base.
Once the new belts are installed, using a Browning or Gates
tension gauge (or equivalent) illustrated in Figure 6-1; adjust
the belt tension as follows;
1. To determine the appropriate belt deflection;
a. Measure the center-to-center shaft distance (in
inches) between the fan and motor sheaves.
b. Divide the distance measured in Step 1a by 64; the
resulting value represents the amount of belt
deflection that corresponds to the proper belt tension.
2. Set the large O-ring on the belt tension gauge at the de-
flection value determined in Step 1b.
3. Set the small O-ring at zero on the force scale of the
gauge plunger.
4. Place the large end of the gauge at the center of the belt
span; then depress the gauge plunger until the large O-
ring is even with the top of the next belt or even with a
straightedge placed across the fan and motor sheaves.
Refer to Figure 6-1.
5. Remove the belt tension gauge. The small O-ring now in-
dicates a number other than zero on the plunger’s force
scale. This number represents the force (in pounds) re-
quired to give the needed deflection.
6. Compare the “force” scale reading (Step 5) with the appro-
priate “force” value listed in Table 6-1. If the “force” read-
ing is outside the range, readjust the belt tension.
Note: Actual belt deflection “force” must not
exceed the maximum “force” value shown in
Table 6-1.
7. Recheck the belt tension at least twice during the first 2 to
3 days of operation. Belt tension may decrease until the
new belts are “run in”.
Figure 6-1
Belt Tension Gauge
Table 6-1
Belt Tension Measurement and Deflection Ranges
Deflection Force (Lbs.)
Belts
Super
Steel Cable
Cross Small P.D
Gripbelts
Gripnotch
Gripbelts
Section
Range
Min. Max.
Min.
Max.
Min.
Max
3.0 - 3.6
3
4 1/2 3 7/8
5 1/2 3 1/4
4
A
3.8 - 4.8
3 1/2
5
4 1/2
6 1/4 3 3/4 4 3/4
5.0 - 7.0
4
5 1/2
5
6 7/8 4 1/4 5 1/4
3.4 - 4.2
4
5 1/2 5 3/4
8
4 1/2 5 1/2
B
4.4 - 5.6
5 1/8 7 1/8 6 1/2
9 1/8 5 3/4 7 1/4
5.8 - 8.8
6 3/8 8 3/4 7 3/8 10 1/8
7
8 3/4
Unit Start-up