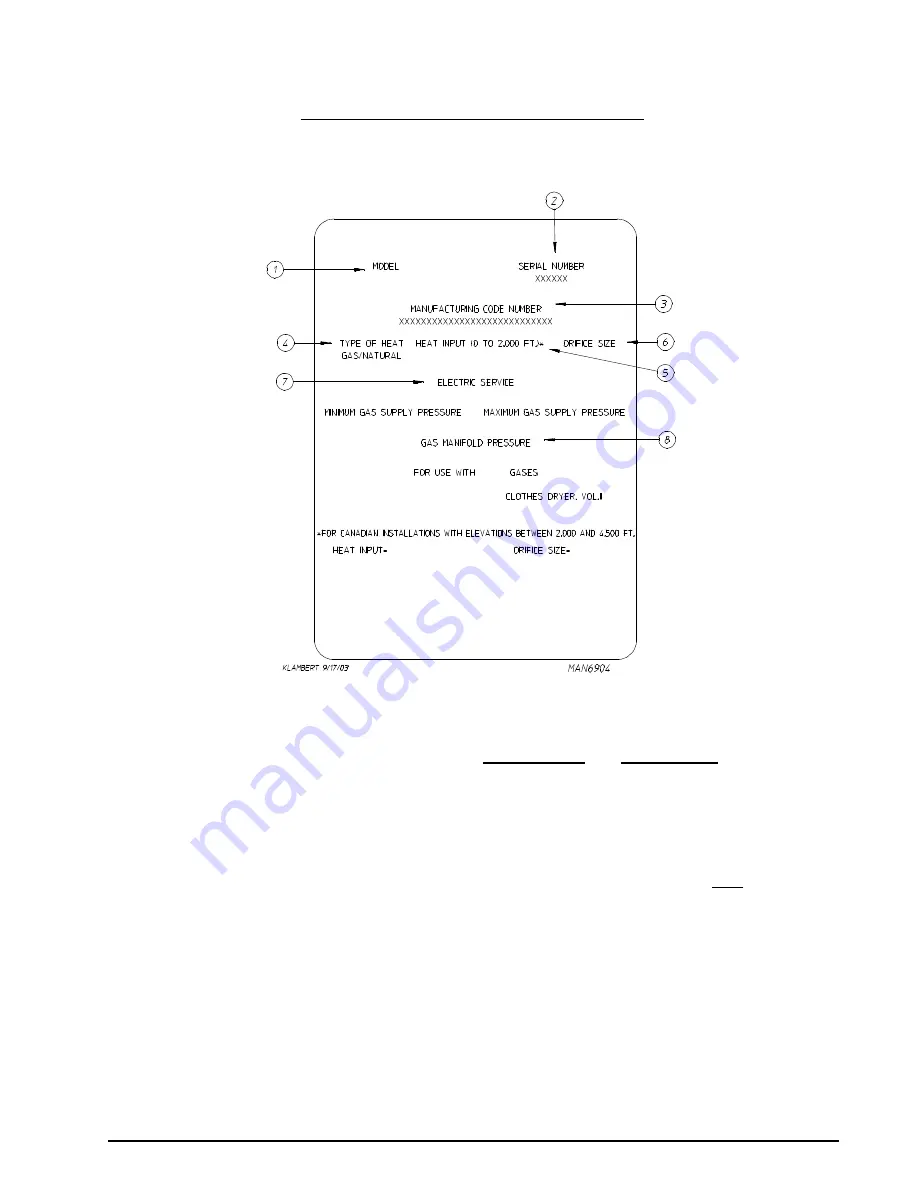
113159-2
www.amdry.com
37
SECTION VII
DATA LABEL INFORMATION
When contacting
American Dryer Corporation
, certain information is required to insure proper service/parts
information from
ADC
. This information is on the data label located on the left side panel area behind top control
(access) door. When contacting
ADC
, please have the
model number
and
serial number
available.
1.
MODEL NUMBER
– Describes the style of dryer and type of heat (gas, electric, or steam).
2.
SERIAL NUMBER
– Allows the manufacturer to gather information on your particular dryer.
3.
MANUFACTURING CODE NUMBER
– The number issued by the manufacturer
,
which describes
ALL
possible options
on your particular model.
4.
TYPE OF HEAT
– This describes the type of heat for your particular dryer, gas (either natural gas or liquid propane [L.P.]
gas), electric, or steam.
5.
HEAT INPUT
(for GAS DRYERS) – This describes the heat input in British Thermal Units per Hour (Btu/hr).
6.
ORIFICE SIZE
(for GAS DRYERS) – Gives the number drill size used.
7.
ELECTRIC SERVICE
– This describes the electric service for your particular model.
8.
GAS MANIFOLD PRESSURE
(for GAS DRYERS) – This describes the manifold pressure taken at the gas valve tap.
Summary of Contents for AD-81 III
Page 46: ...ADC113159 2 05 05 04 25 ...