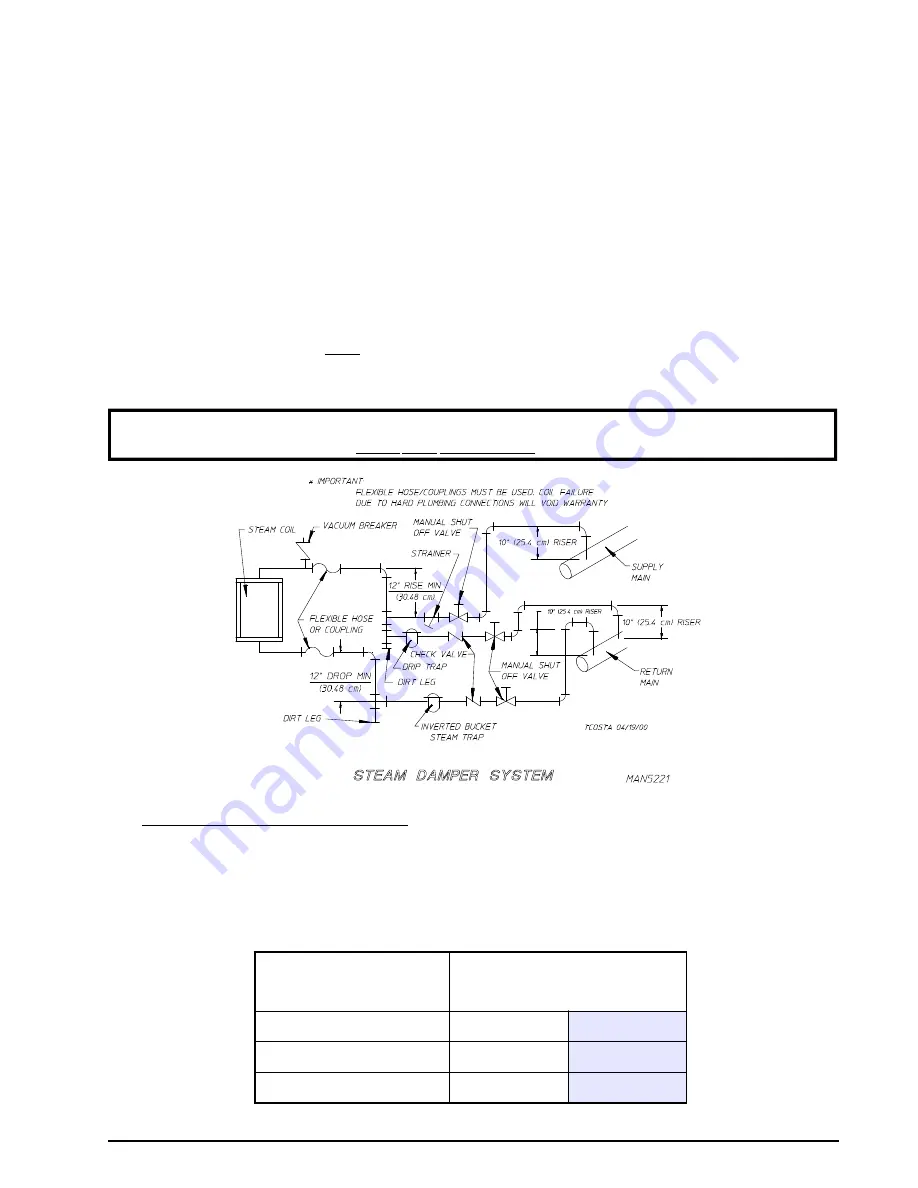
113159-2
www.amdry.com
23
d. Shutoff valves for each dryer
should be
installed in the supply, return, and drip trap return lines. This
will allow the dryer to be isolated from the supply and return mains if the dryer needs maintenance
work.
e. Install an inverted bucket steam trap and check valve for each unit at least 12-inches (30.48 cm) below
steam coil as close to the coil as possible. A trap with a capacity of 1,000 lbs (454 kg) of condensate per
hour at 125 psi (8.62 bar) is needed for each unit.
f. A vacuum breaker
should be
installed for each unit in the piping. This will prevent the condensing
steam from causing a vacuum inside the coil and possibly damaging the coil.
g. The supply and return lines
should be
insulated. This will save energy and provide for the safety of the
operator and maintenance personnel.
h. Water pockets in the supply line, caused by low points, will provide wet steam to the coil possibly
causing coil damage.
ALL
horizontal runs of steam supply piping
should be
pitched 1/4-inch
(6.35 mm) for every 1 foot (0.30 meters) back towards the steam supply header causing any condensate
in the line to drain to the header. Install a bypass trap in any low point to eliminate wet steam.
IMPORTANT:
Flexible hoses and couplings
must be
used. Coil failure due to hard plumbing
connections will VOID THE WARRANTY.
3. Steam Damper Air System Connections
This dryer is manufactured with a pneumatic (piston) damper system, which requires an external supply of
compressed air. The air connection is made to the steam damper solenoid valve, which is located at the
rear inner top area of the dryer just above the electric service relay box.
a. Air Requirements
Shaded areas are stated in metric equivalents
Compressed
Air Supply
Air Pressure
Normal
80 psi
5.51 bar
Minimum Supply
70 psi
4.82 bar
Maximum Supply
90 psi
6.21 bar
Summary of Contents for AD-81 III
Page 46: ...ADC113159 2 05 05 04 25 ...