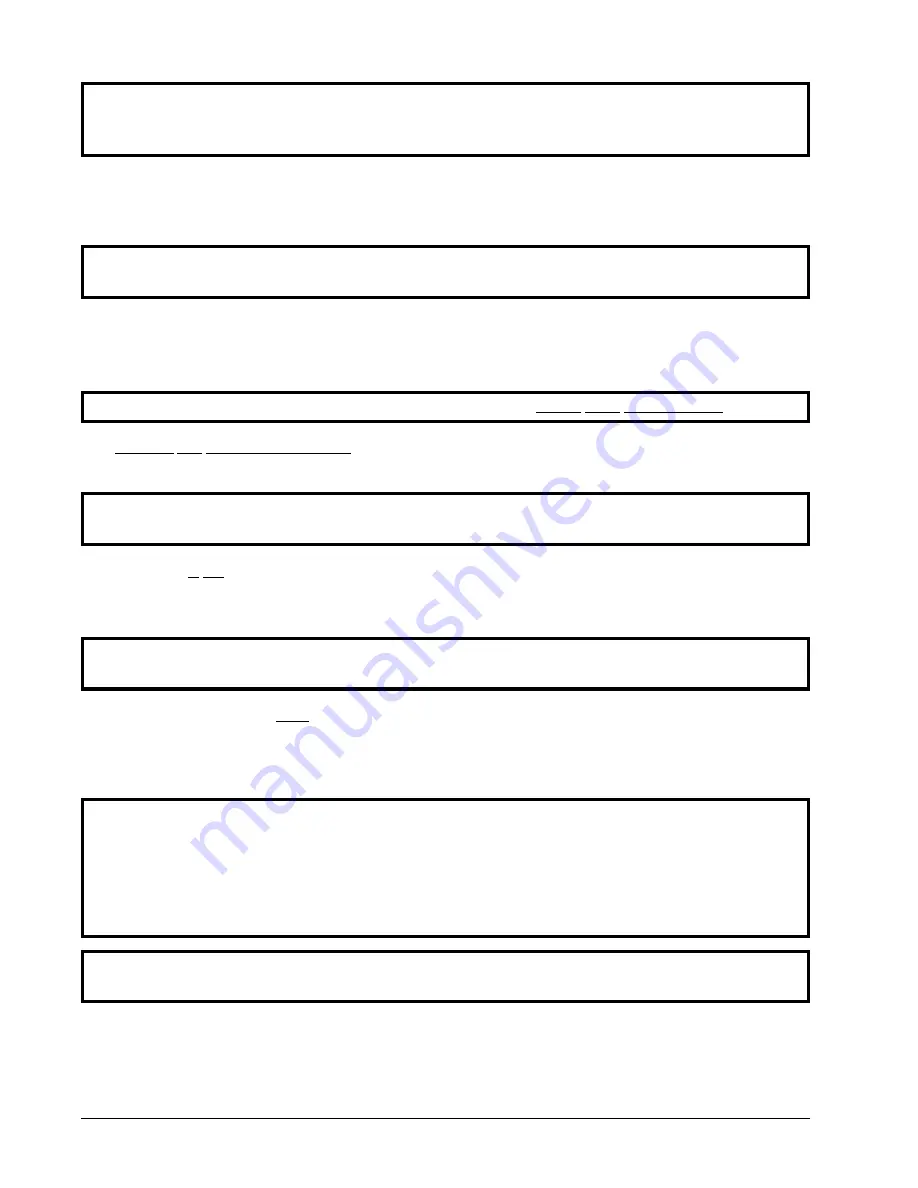
4
American Dryer Corp.
113235 - 5
WARNING:
DO NOT
use heat for drying articles that contain plastic, foam, sponge rubber, or
similarly textured rubberlike materials. Drying in a heated basket (tumbler) may
damage plastics or rubber and may be a fire hazard.
7. A program
should be
established for the inspection and cleaning of lint in the burner area, exhaust ductwork,
and area around the back of the dryer. The frequency of inspection and cleaning can best be determined
from experience at each location.
WARNING:
The collection of lint in the burner area and exhaust ductwork can create a potential
fire hazard.
8. For personal safety, the dryer
must be
electrically grounded in accordance with local codes and/or the
National Electrical Code ANSI/NFPA NO. 70-LATEST EDITION, or in Canada, the Canadian Electrical
Codes Parts 1 & 2 CSA C22.1-1990 or LATEST EDITION.
NOTE:
Failure to electrically ground the dryer properly will VOID THE WARRANTY.
9.
UNDER NO CIRCUMSTANCES
should the dryer door switch, lint drawer switch, or heat safety circuit
ever be disabled.
WARNING: PERSONAL INJURY OR FIRE COULD RESULT
should the dryer door
switch, lint door switch, or heat safety circuit ever be disabled.
10. This dryer is not to be used in the presence of dry cleaning solvents or fumes.
11. Remove articles from the dryer as soon as the drying cycle has been completed.
WARNING:
Articles left in the dryer after the drying and cooling cycles have been completed
can create a fire hazard.
12.
READ AND FOLLOW ALL CAUTION AND DIRECTION LABELS ATTACHED TO THE DRYER.
13. For safety, proper operation, and optimum performance, the dryer
must not be
operated with a load less
than sixty-six percent (66%), 20 lb (9.07 kg) of its rated capacity.
WARNING: YOU MUST DISCONNECT AND LOCK OUT THE ELECTRIC SUPPLY
AND THE GAS SUPPLY BEFORE ANY COVERS OR GUARDS ARE
REMOVED FROM THE MACHINE TO ALLOW ACCESS FOR
CLEANING, ADJUSTING, INSTALLATION, OR TESTING OF ANY
EQUIPMENT PER OSHA
(Occupational Safety and Health Administration)
STANDARDS.
IMPORTANT: Dryer
must be
installed in a location/environment, which the ambient
temperature remains between 40º F (4.44º C) and 130º F (54.44º C).