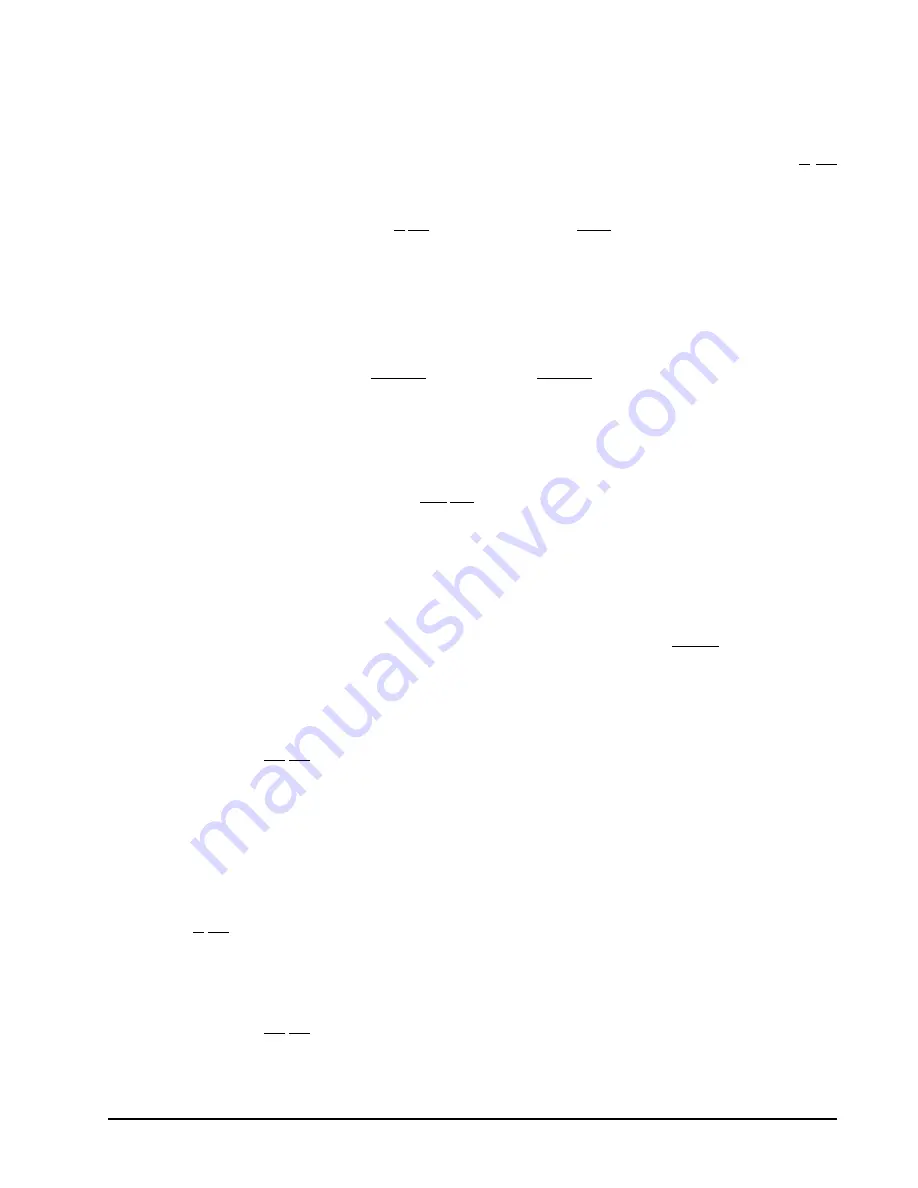
113047 - 21
37
H. Microprocessor controller (computer) L.E.D. display reads “SEFL”...
The “SEFL” display condition indicates a rotational sensor circuit failure which means that there is a fault
somewhere in the basket (tumbler) rotation detection circuit...or...the microprocessor controller (computer)
program related to this circuit (PL01) is set incorrectly in the active mode (“SEn”) where the dryer is not
equipped with the optional rotation sensor and should be set in the nonactive mode (“nSEN”).
If the dryer is equipped with the optional rotational sensor and for whatever reason the microprocessor controller
(computer) detects that the basket (tumbler) is not turning, it will disable ALL of the dryer outputs (shut the dryer
down), and the L.E.D. display will read “SEFL.” The L.E.D. display will continue to read “SEFL” until the
microprocessor is manually reset by closing and opening the Program Switch (PS).
Possible causes:
1. Loose/slipping (out of proper adjustment) basket (tumbler) and/or idler belt.
2. Broken basket (tumbler) and/or idler belt.
3. Failed motor (refer to Item B on page 35 and Item D on page 36).
4. Failure in the rotational sensor circuit...
a. Failed rotational sensor.
b. Loose connection or break between the rotation sensor and the microprocessor controller (computer).
I.
Microprocessor controller (computer) will not accept any, or only accept certain keypad entries...
1. Failed keypad label assembly.
2. Failed microprocessor controller (computer).
J.
Microprocessor controller (computer) locks up and the light emitting diode (L.E.D.) display
reads erroneous message(s) or only partial segments...
1. Transient power voltage (spikes)...disconnect power to the dryer, wait 1 minute (NOTE: for dryer models
with the optional battery backup...disconnect battery), then reestablish power to the dryer. If the problem
is still evident, proceed to Item J2 thru Item J4 below.
2. Failed keypad label assembly.
3. Improper grounding of the dryer or the microprocessor controller (computer) ground connections to the
panel or the dryer are not proper.
4. Failed microprocessor controller (computer).
K. Dryer stops during a cycle and the microprocessor controller (computer) L.E.D. display returns
to “FILL”...
If the dryer is equipped with optional battery backup...
1. Refer to Item J1, Item J3, or Item J4 above.
If the dryer is not equipped with optional battery backup...
1. Loose connection somewhere in the power source to the dryer.
2. Loose connection in main power circuit to the microprocessor controller (computer).
3. Improper grounding of the dryer or the microprocessor controller (computer) ground connections to the
panel or the dryer are not proper.
4. Failed microprocessor controller (computer).
Summary of Contents for AD-236
Page 26: ...22 American Dryer Corp 113047 21...
Page 48: ...ADC Part No 113047 21 11 13 15...