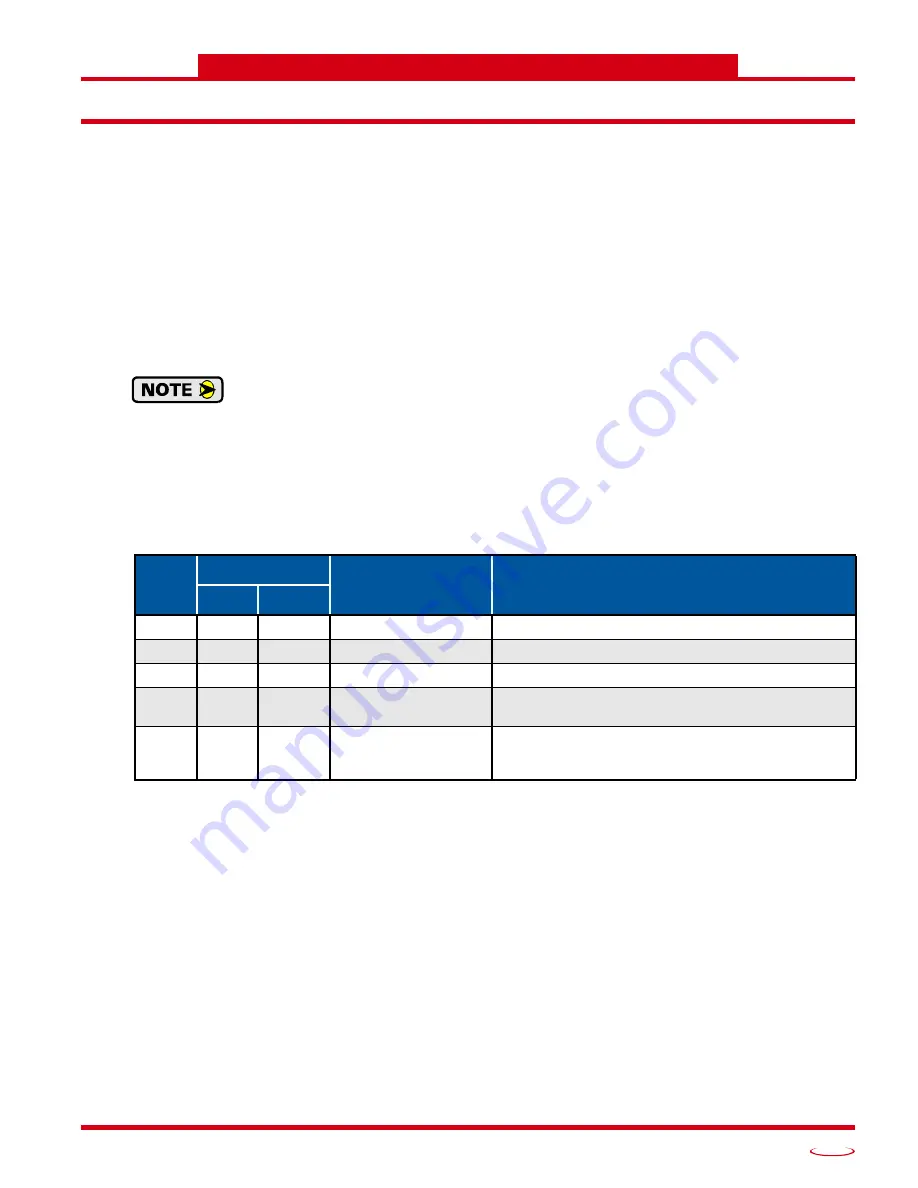
20 Gear Drive, Plymouth Ind. Park, Terryville, CT 06786
Tel: (860) 585-1254 Fax: (860) 584-1973 http://www.amci.com
67
EtherNet/IP Reference
CIP P
OSITION
S
ENSOR
O
BJECT
Common Industrial Protocol
EtherNet/IP is a protocol stack that implements the Common Industrial Protocol (CIP) over Ethernet using
TCP/IP. The CIP is sponsored by the Open DeviceNet Vendors Association (ODVA) and is implemented
over a variety of networks. The NR60E2 follows the Encoder Device Profile that is defined in the CIP speci-
fication. The Configuration and Programming instances in previous chapters are actually custom instances
that simplify configuring and programming the encoder.
In addition to these custom instances, the NR60E2 implements the Position Sensor Object, which is a manda-
tory object for every product that implements the Encoder Device Profile as defined in the specification. The
explicit messages that are used to preset the position value and save the programmed parameters are two com-
mands defined in the Position Sensor Object.
The NR60E2 implements the CIP revision 2 definition of the Position Sensor Object.
Using the Position Sensor Object to communicate with the NR60E2 is
completely optional
.
Most applications should communicate with the NR60E2 using the custom instances as
explained in the previous chapters because it will greatly simplify your PLC programming.
The only reasons to use the Position Sensor Object is if you need extremely fine grain control
over communications with the NR60E2 or if you use EtherNet/IP encoders from multiple ven-
dors and you decide to write code that can be used with any of these sensors.
Supported Services
The following table lists the common services implemented by the NR60E2 for the Position Sensor Object.
The services that are implemented only on the Class level (not on the Instance) should address Instance 0.
Table R3.1 Supported Services
Service Code 16#0E,
Get_Attribute_Single
is used to read data from the Position Sensor Object class.
Service Code 16#10,
Set_Attribute_Single
is used to write data to the Position Sensor Object class.
Supported Class Attributes
The only supported Class attribute is 1 and it returns the revision number of the definition of the object.
Because the NR60E2 implements the CIP revision 2 definition of the Position Sensor Object, this attribute
will always return a value of “2”.
Service
Code
Implemented
Service Name
Description of Service
Class
Instance
16#05 Yes
No
Reset
Resets all parameter values to the factory default
16#0E Yes
Yes
Get_Attribute_Single
Returns the contents of the specified attribute
16#10 No
Yes
Set_Attribute_Single
Modifies an attribute value
16#15 Yes
No
Restore
Restores all parameter values from non-volatile
storage
16#16 Yes
No
Save
Saves all programmable parameters to the non-vola-
tile storage including the position offset derived
from setting the Preset Value, (Attribute 16#13)
Summary of Contents for NR60E2
Page 1: ...MICRO CONTROLS INC ADVANCED U s e r M anual E2 Technology E2 Technology Manual 940 0D161...
Page 6: ...TABLE OF CONTENTS NR60E2 User Manual ADVANCED MICRO CONTROLS INC 6 Notes...
Page 20: ...NR60 SPECIFICATIONS NR60E2 User Manual ADVANCED MICRO CONTROLS INC 20 Notes...
Page 44: ...PROTOCOL SPECIFIC INFORMATION NR60E2 User Manual ADVANCED MICRO CONTROLS INC 44 Notes...
Page 52: ...IMPLICIT COMMUNICATIONS WITH AN EDS EtherNet IP Protocol ADVANCED MICRO CONTROLS INC 52 Notes...
Page 58: ...IMPLICIT COMMUNICATIONS WITHOUT EDS EtherNet IP Protocol ADVANCED MICRO CONTROLS INC 58 Notes...
Page 70: ...CIP POSITION SENSOR OBJECT EtherNet IP Protocol ADVANCED MICRO CONTROLS INC 70 Notes...
Page 90: ...PROFINET CYCLIC DATA FORMATS PROFINET Protocol ADVANCED MICRO CONTROLS INC 90 Notes...
Page 98: ...LEADERS IN ADVANCED CONTROL PRODUCTS ADVANCED MICRO CONTROLS INC...