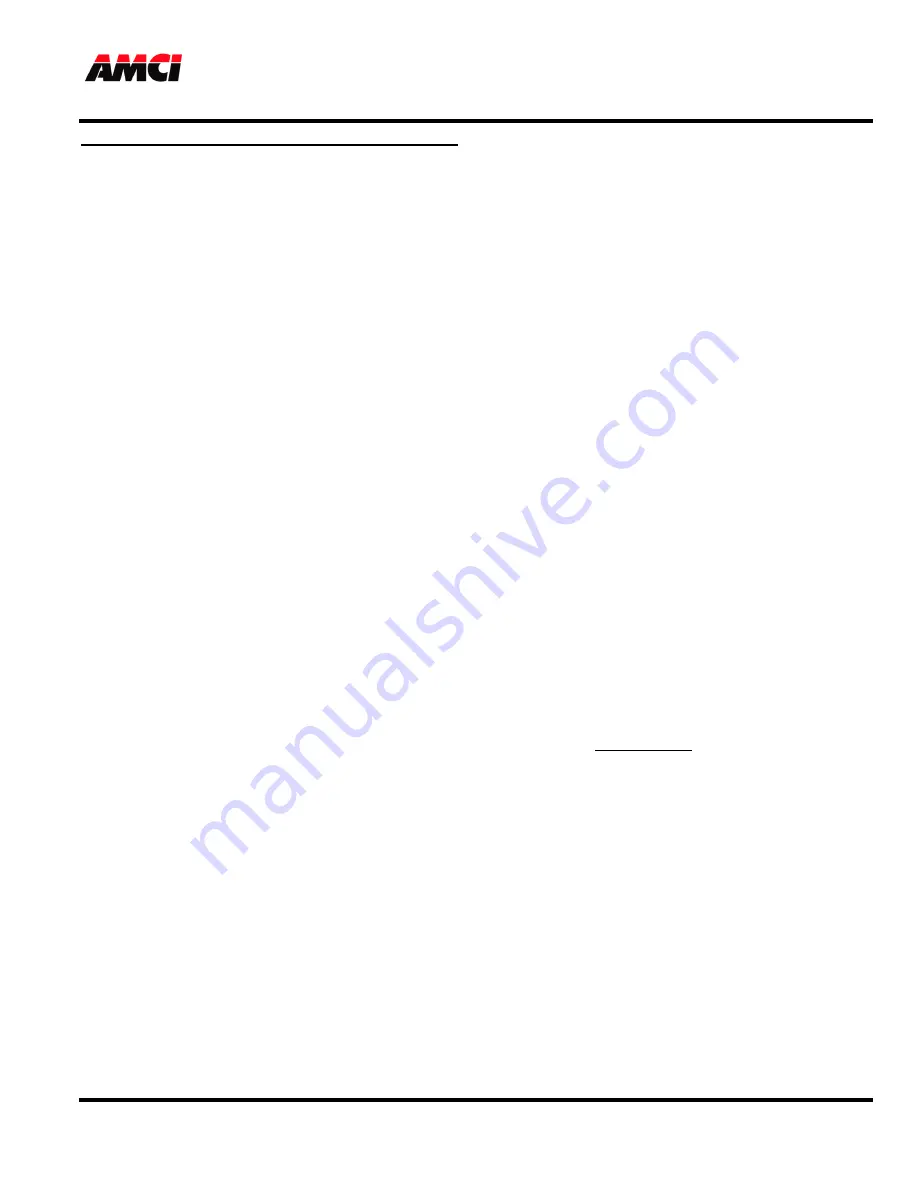
20 Gear Drive, Plymouth Industrial Park, Terryville, CT 06786 page: 11
Tel: (860) 585-1254 Fax: (860) 584-1973 Web: www.amci.com
ControlLogix 7252 LDT Interface Manual
Revision 1.5
Chapter 3: Programmable Parameters
The 7252 is configured by programming its Programmable Parameters. These parameters are broken down into three
groups, Module Setup, LDT Setup, and Data Setup parameters.
The 7252 uses two methods for the programming and monitoring of data. Input and Output registers are used to
program and monitor data that occurs on a regular schedule, such as reading the data value and status information or
setting the system time. Message instructions are used for operations that occur less frequently, such as programming
the module set up parameters or reading back the set up data for trouble shooting purposes.
Transducer Fault Latch - Transducer faults can be caused by improper wiring, electrical noise, or a damaged
transducer. When the unit detects a fault condition, it reports this fault over the backplane. Normally, a transducer fault
is not latched by the 7252 module and the Transducer Fault conditions will be cleared as soon as the 7252 module
detects valid LDT signals. If you have a situation where electrical noise is causing spurious transducer faults that you
can safely ignore, leave this parameter in its default condition. However, if you want to reliably capture these transient
faults, then you must enable the Transducer Fault Latch parameter. In this case, you must send a Clear Error command
to the 7252 module to clear the fault.
The default Transducer Fault Latch value is set to Self Clearing.
Count Direction: This parameter gives you the ability to reverse the direction of motion needed to increase the
position count. For simplicity’s sake, the two values for this parameter are called Positive Direction and Negative
Direction. When this parameter is set to its default of Positive, the Data Value is not changed. When this parameter is
set to Negative, the Data Value is multiplied by -1 before it is reported. For linear transducers, this has the effect of
reversing the direction of motion needed to increase the count. When using LDT’s and the Count Direction is set to
Positive, the Data Value usually increases as the magnet moves away from the head of the LDT. When the Count
Direction is set to Negative, the Data Value increases as the magnet moves towards the head of the LDT. You will
need probably need to Apply the Preset to the Data Value after you program the Count Direction parameter.
Velocity Update Time: The Velocity Update Time parameter sets the amount of time between Rate of Change
information updates to the PLC. Its can be set to either 60 milliseconds or 120 milliseconds, with 120 milliseconds
being the default. Decrease the time between updates for faster response to changes in this value. Increase the time
between updates for better averaging of this value. The Velocity update time does not affect the rate at which the
position data is updated.
The Velocity data is measured in Counts/Second. For example, if you have programmed the 7252 module for 0.001
inch resolution, and if the magnet is moving at a rate of two inches per second, then the 7252 module will report a
velocity value of 2000 counts / second.
Measurement Unit - Specifies the measurement unit for the Full Scale Length parameter and affects
the values that can be entered for Full Scale Count. This bit will indicate whether the unit of measurement is in inches
or mm (millimeters).
•
When this bit is set to ‘1’, the position and velocity data is reported back in mm with a maximum resolution of
0.1mm
•
When this bit is set to ‘0’, the unit of measurement will be reported back in inches with a maximum resolution
of 0.001 in
•
The default Measurement Unit parameter is inches