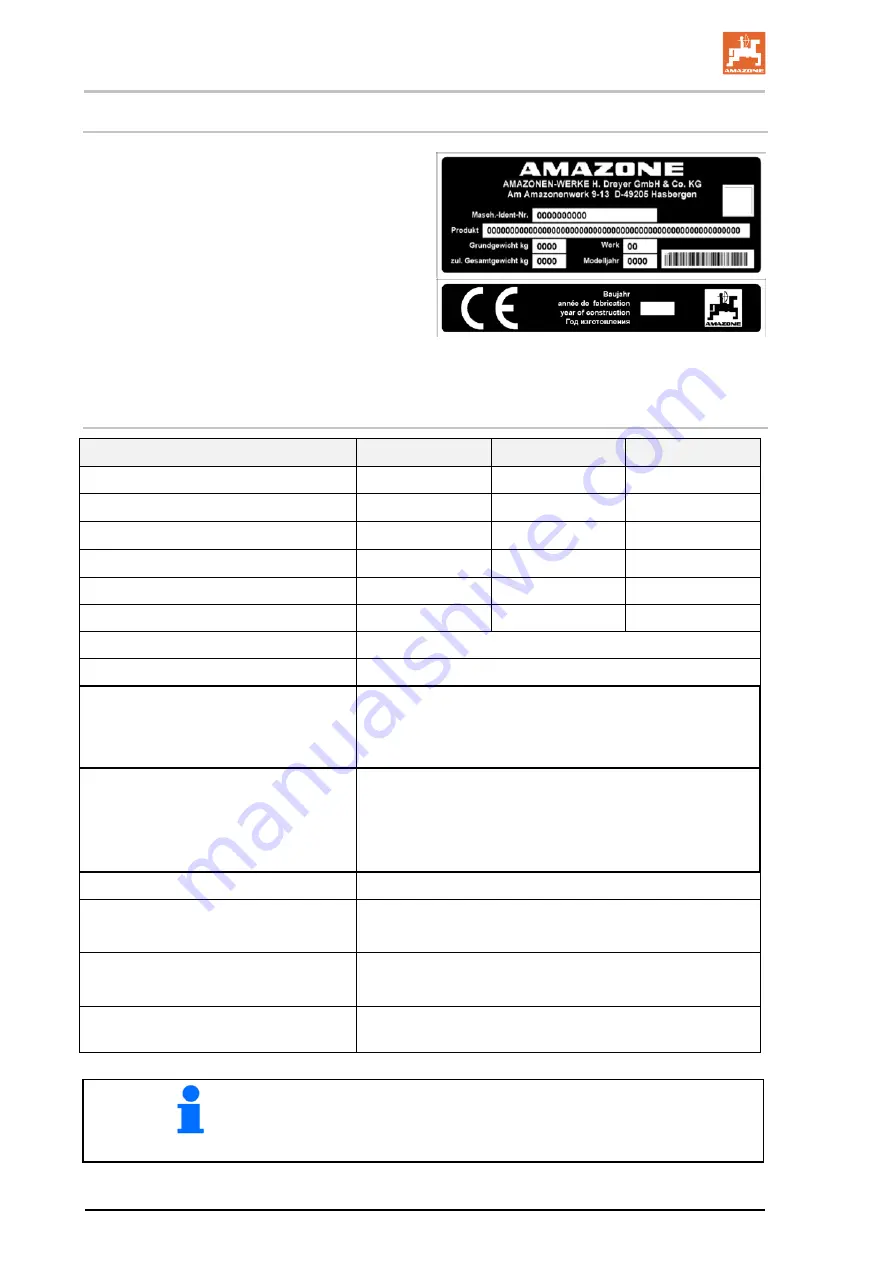
Product description
4.6
Rating plate and CE marking
The rating plate specifies:
•
Implement ID No.
•
Product
•
Basic weight kg
•
Permissible total weight kg
•
Factory
•
Model year
•
Model year
4.7
Technical data
Cenius
3003
3503
4003
Working width
3000 mm
3500 mm
4000 mm
Transport width
3000 mm
3500 mm
4000 mm
with
Double-disc coulter
3050 mm
3550 mm
4050 mm
Wing coulter
3080 mm
3580 mm
4080 mm
Tine spacing
273 mm
292 mm
308 mm
Number of tines
11
12
13
Number of tine rows
3
Maximum working depth
300 mm
Overload protection of the tines:
Cenius Super
tension spring
Cenius Special
shear bolt
Levelling unit:
•
Concave discs
Disc diameter
460
•
Alternative spring tines
Working speed
10-15
Total length
3,80
4,25 (with tandem roller)
Attachment category
Category 2 or 3
Diameter ofbolt: Category 3
Centre of gravity distance (d)
1900 mm
•
You can find the value for the permissible total weight on the
implement rating plate.
•
Weigh the empty implement to determine the basic weight.
32
Cenius 03 BAG0144.5 10.19
Summary of Contents for Cenius 3003
Page 80: ......