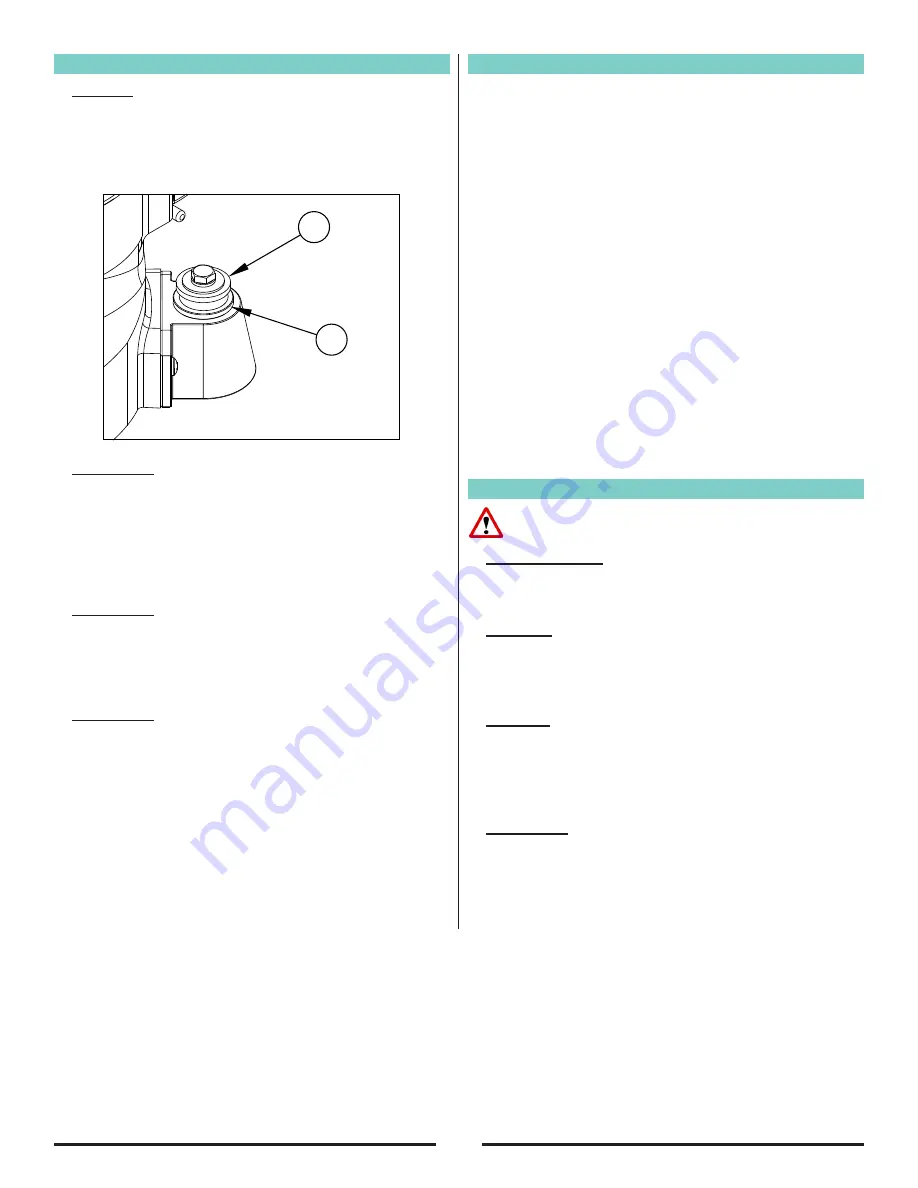
12
A
B
Adjustment Procedures
Leveling
To level machine: Grasp caster adjusting screw “A”
with an appropriate tool (pliers etc.). Using a similar
tool, loosen locknut “B” with a counter clockwise
motion. (Figure 6).
Condition 1
: Pad creates ridges on both edges or a
“hop” is experienced.
Rotate both adjusting screws equal amounts
clockwise. Tighten locknut’s and test on a piece
of plywood. Repeat procedure until condition is
corrected. We recommend you not exceed 1/8”
rotation for each attempt.
Condition 2
: Pad creates a ridge on the tip of the pad.
Rotate both adjusting screws counter clockwise,
tighten locknut’s and test. Repeat procedure until
condition is corrected. Use only 1/8 rotation for each
attempt.
Condition 3
: Pad creates a ridge on only one side of the
pad.
Either rotate the adjusting screw of the side effected
clockwise or rotate the adjusting screw opposite
counterclockwise, depending on whether the ridge
terminates beyond the tip of the pad or prior to it. If it
is prior to the tip, adjust the side effected, otherwise
adjust the opposite side.
Sanding Cuts & Sandpaper
Initial Cut
:
The purpose of the initial cut is to remove old finish and
gross imperfections on the floor surface. Use a course
(20-36 grit) grain abrasive.
If glazing, loading, or burning takes place
immediately into an initial cut, select a coarser
abrasive. If this should occur during an initial cut, the
abrasive has dulled and must be replaced.
Final Cuts
:
The purpose of a finishing cut is to remove the
scratches produced during the initial cut. Use a fine (60-
80 grit) grain abrasive.
If the surface remains rough after a finishing cut, it may
be necessary to use an even finer grain of abrasive (80-
100grit). Care should be taken in selecting the grit size
of the abrasive. A very fine grain will close the pores
on a wood floor making admission of a stain difficult. If
glazing or burning should occur the abrasive has dulled
and must be replaced.
Routine Maintenance
CAUTION
: Failure to perform maintenance at
recommended intervals may void warranty.
Carbon Brushes
Have the carbon brushes replaced at least every 500
hours and more frequently under heavy use.
Dust Bag
Periodically the dust bag should be turned inside out,
shaken vigorously and machine washed in cold water
to prevent pore blockage and loss of dust control.
Bearings
To insure reliable performance, have armature and
pad driver bearings inspected for wear or damage
after every 1500 hours. If used heavily, have the
bearings replaced seasonally.
Lubrication
The machine comes fully lubricated. The gears in the
gear box have enough lubrication for approximately
six months of normal operation. Have the lubricant
changed at least every 6 months or more frequently
under heavy use.
Figure 6
Summary of Contents for American Sanders Super 7R 240V
Page 1: ...Edger Super 7R 240V Operator s Manual...
Page 2: ......
Page 15: ...Electrical Schematic 15...
Page 22: ......