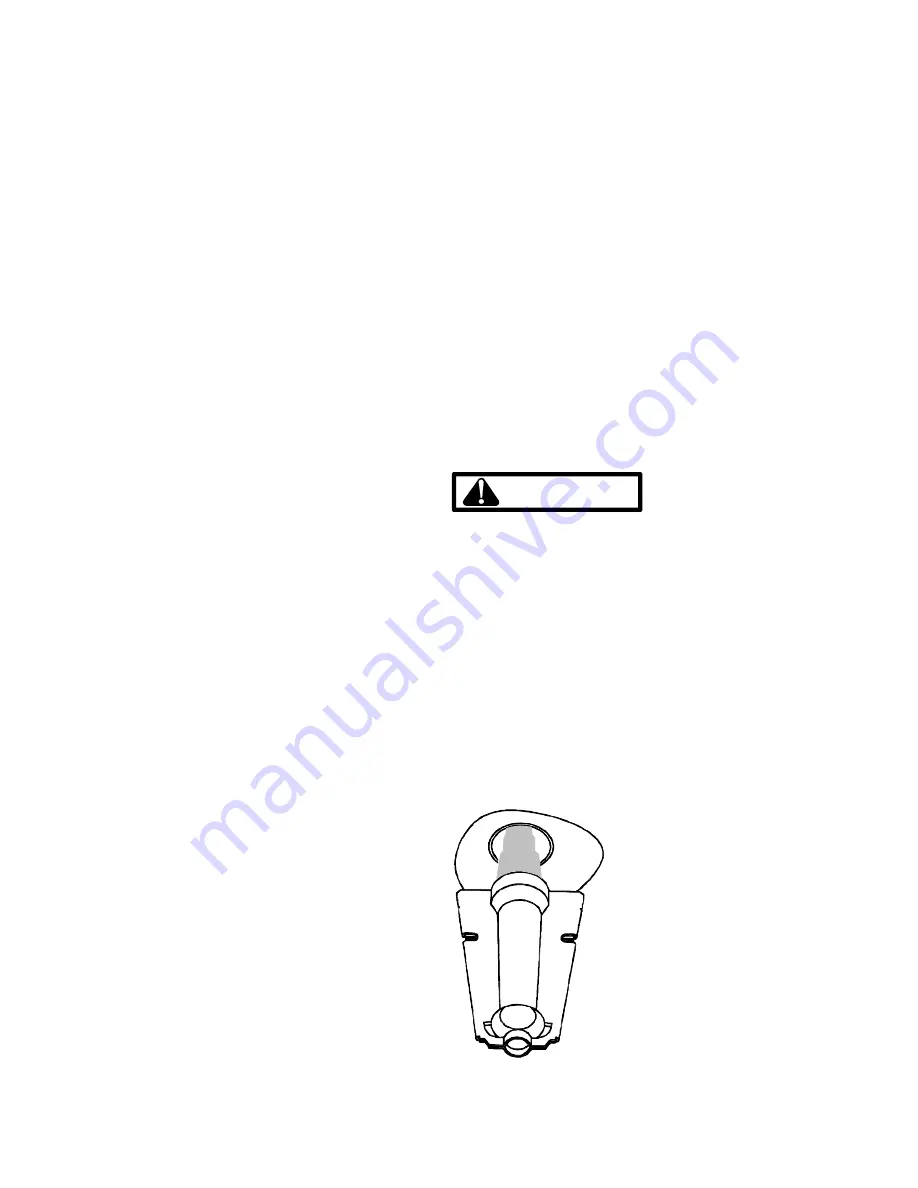
MAINTENANCE
54
Rev. 0
3. Remove filters
4. Remove blower compartment door. Vacuum compart-
ment. Replace blower compartment door.
5. Replace filters opposite of removal.
6. Replace access door in ductwork.
Horizontal Unit Filter Removal
Filters in horizontal installations are located in the central
return register.
INDUCED DRAFT AND CIRCULATION BLOWERS
The bearings in the induced draft blower and circulator
blower motors are permanently lubricated by the manufac-
turer. No further lubrication is required. Check motor wind-
ings for accumulation of dust which may cause overheat-
ing. Clean as necessary.
CONDENSATE DRAINAGE SYSTEM (QUALIFIED
SERVICER ONLY)
The drain tubes, standpipe, and field supplied drain line
must be checked annually and cleaned as often as neces-
sary to ensure proper condensate drainage.
FLUE PASSAGES (QUALIFIED SERVICER ONLY)
At the start of each heating season, inspect and, if neces-
sary, clean the furnace flue passages.
CLEANING FLUE PASSAGES (QUALIFIED SERVICER
ONLY)
1. Turn OFF the electrical power and gas supply to the
furnace.
2. Disconnect the gas line and remove the burner/ mani-
fold assembly by removing the screws securing the as-
sembly to the partition panel.
3. Disconnect the flue pipe system from the induced draft
blower.
4. Remove the induced draft blower and, drain and pres-
sure tap hoses from the recuperator coil front cover.
5. Remove the recuperator coil front cover to expose the
coil tubes and turbulators.
6. Remove the recuperator coil turbulators individually by
slowly pulling each turbulator forward firmly.
7. Clean the recuperator coil tubes using a long handle
wire brush, such as a gun cleaning brush.
8. Clean the primary heat exchanger tubes using a wire
brush attached to a length of high grade stainless steel
cable, such as drain cleanout cable. Attach a variable
speed reversible drill to the other end of the cable. Slowly
rotate the cable with the drill and insert it into one of the
heat exchanger tubes. While reversing the drill, work
the cable in and out several times to obtain sufficient
cleaning. Repeat for each tube.
9. Clean residue from furnace using a vacuum cleaner.
10. Replace the parts removed in the previous steps in re-
verse order.
11. Turn on electrical power and gas to furnace. Check for
leaks and proper unit operation.
12. Severe heat exchanger fouling is an indication of an
operational problem. Perform the checks listed in
Start-
up Procedure and Adjustments section to reduce the
chances of repeated fouling.
FLAME SENSOR (QUALIFIED SERVICER ONLY)
Under some conditions, the fuel or air supply can create a
nearly invisible coating on the flame sensor. This coating
acts as an insulator, causing a drop in the flame sensing
signal. If this occurs, a qualified servicer must carefully clean
the flame sensor with emery cloth or steel wool. After clean-
ing, the flame sensor output should be as listed on the speci-
fication sheet.
BURNERS
WARNING
ELECTRICAL COMPONENTS ARE CONTAINED IN
BOTH COMPARTMENTS. TO AVOID ELECTRICAL
SHOCK, INJURY OR DEATH, DO NOT REMOVE ANY
INTERNAL COMPARTMENT COVERS OR ATTEMPT
ANY ADJUSTMENT. CONTACT A QUALIFIED SERVICE
AGENT AT ONCE IF AN ABNORMAL FLAME APPEAR-
ANCE SHOULD DEVELOP.
Periodically during the heating season make a visual check
of the burner flames. Turn the furnace on at the thermo-
stat. Wait a few minutes, since any dislodged dust will alter
the normal flames appearance. Flames should be stable,
quiet, soft and blue with slightly orange tips. They should
not be yellow. They should extend directly outward from
the burner ports without curling downward, floating or lifting
off the ports.
Check the burner flames for:
1. Good adjustment
2. Stable, soft and blue
3. Not curling, floating, or lifting off.
Burner Flame