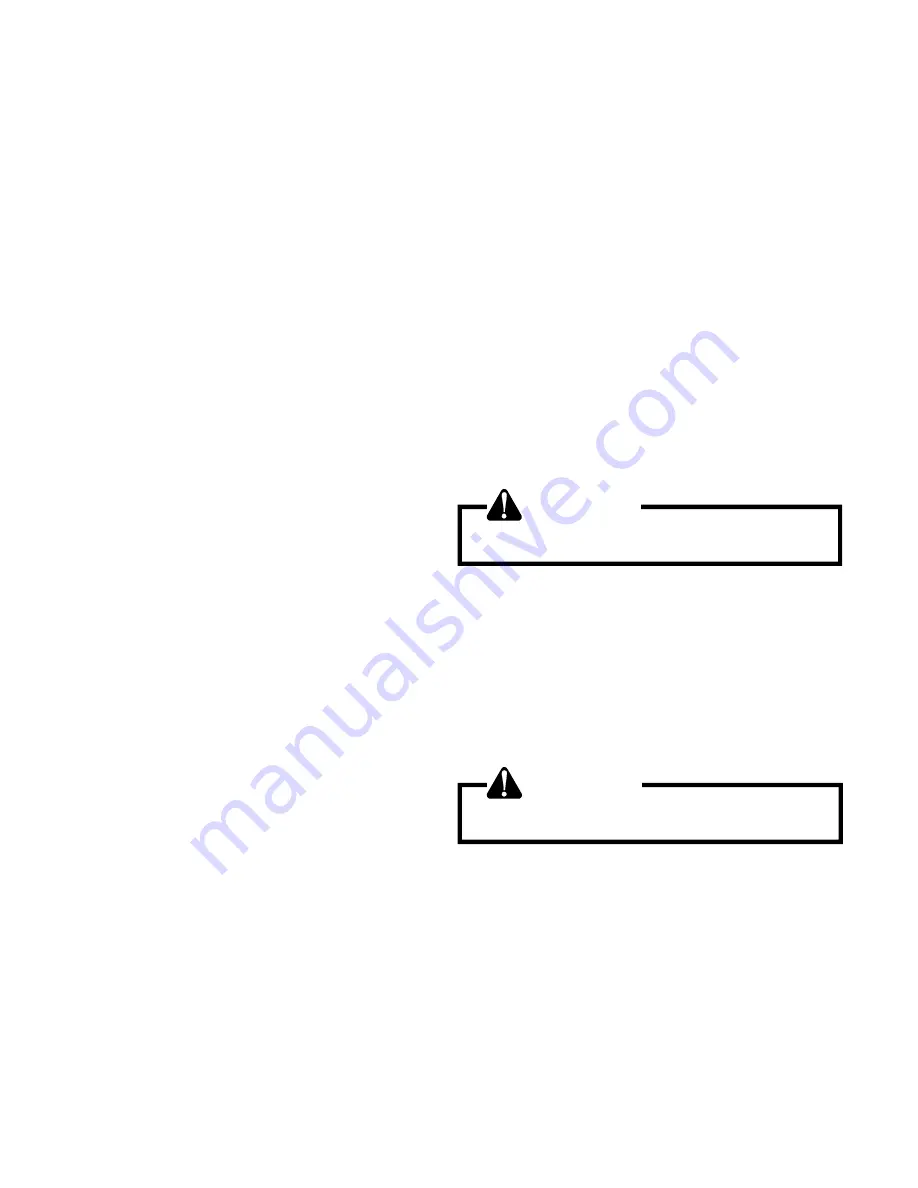
SERVICING
46
S-109
CHECKING SUBCOOLING
Refrigerant liquid is considered subcooled when its temperature is
lower than the saturation temperature corresponding to its pressure.
The degree of subcooling equals the degrees of temperature decrease
below the saturation temperature at the existing pressure.
1. Attach an accurate thermometer or preferably a thermo-
couple type temperature tester to the liquid line as it leaves
the condensing unit.
2. Install a high side pressure gauge on the high side (liquid)
service valve at the front of the unit.
3. Record the gauge pressure and the temperature of the line.
4. Review the technical information manual or specification
sheet for the model being serviced to obtain the design
subcooling.
5. Compare the hi-pressure reading to the "Required Liquid
Line Temperature" chart (page 48). Find the hi-pressure value
on the left column. Follow that line right to the column un-
der the design subcooling value. Where the two intersect is
the required liquid line temperature.
Alternately you can convert the liquid line pressure gauge
reading to temperature by finding the gauge reading in Tem-
perature - Pressure Chart and reading to the left, find the
temperature in the °F. Column.
6. The difference between the thermometer reading and pres-
sure to temperature conversion is the amount of subcooling.
ADD CHARGE TO RAISE SUBCOOLING. RECOVER CHARGE
TO LOWER SUBCOOLING.
Subcooling Formula = Sat. Liquid Temp. - Liquid Line Temp.
NOTE:
To adjust subcooling, follow the sequence of S-108.
EXAMPLE:
a. Liquid Line Pressure = 417 psi
b. Corresponding Temp. = 120°F.
c. Thermometer on Liquid line = 109°F.
To obtain the amount of subcooling subtract 109°F from 120°F.
The difference is 11° subcooling. See the specification sheet or
technical information manual for the design subcooling range
for your unit.
There are other causes for high head pressure which may be
found in the "Service Problem Analysis Guide."
If other causes check out normal, an overcharge or a system
containing non-condensables would be indicated.
If this system is observed:
1. Start the system.
2. Remove and capture small quantities of gas from the suc-
tion line dill valve until the head pressure is reduced to
normal.
3. Observe the system while running a cooling performance test.
If a shortage of refrigerant is indicated, then the system con-
tains non-condensables.
S-114
NON-CONDENSABLES
If non-condensables are suspected, shut down the system and
allow the pressures to equalize. Wait at least 15 minutes. Com-
pare the pressure to the temperature of the coldest coil since this
is where most of the refrigerant will be. If the pressure indicates
a higher temperature than that of the coil temperature, non-
condensables are present.
Non-condensables are removed from the system by first removing
the refrigerant charge, replacing and/or installing liquid line drier,
evacuating and recharging.
S-115
COMPRESSOR BURNOUT
When a compressor burns out, high temperature develops caus-
ing the refrigerant, oil and motor insulation to decompose form-
ing acids and sludge.
If a compressor is suspected of being burned-out, attach a refrig-
erant hose to the liquid line dill valve and properly remove and
dispose of the refrigerant.
NOTICE
Violation of EPA regulations may result in fines
or other penalties.
Now determine if a burn out has actually occurred. Confirm by
analyzing an oil sample using a Sporlan Acid Test Kit, AK-3 or its
equivalent.
Remove the compressor and obtain an oil sample from the suc-
tion stub. If the oil is not acidic, either a burnout has not occurred
or the burnout is so mild that a complete clean-up is not neces-
sary.
If acid level is unacceptable, the system must be cleaned by using
the clean-up drier method.
CAUTION
Do not allow the sludge or oil to contact the skin.
Severe burns may result.
NOTE:
The Flushing Method using R-11 refrigerant is no longer
approved by Amana® Brand Heating-Cooling.
S-120
REFRIGERANT PIPING
The piping of a refrigeration system is very important in relation
to system capacity, proper oil return to compressor, pumping rate
of compressor and cooling performance of the evaporator. A bi-
flow filter drier must be brazed on by the installer onsite. Ensure
the bi-flow filter drier pain finish is intact after brazing. If the
paint of the steel filter drier has been burned or chipped, repaint
or treat with a rust preventtive. The recommended location of the
filter drier is before the expansion deveice at the indoor unit.