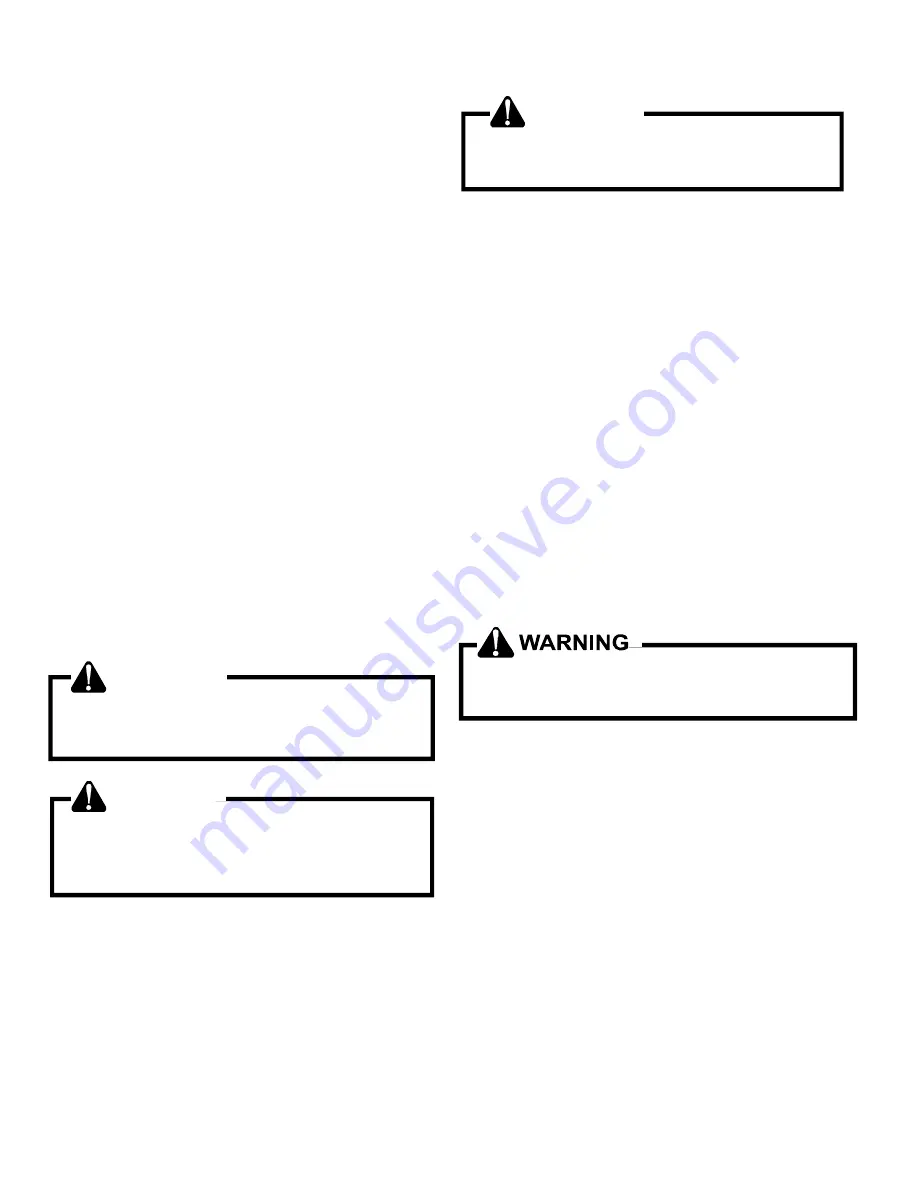
SERVICING
40
2. Plug or cap all openings.
3. Remove all burrs and clean the brazing surfaces of the tubing
with sand cloth or paper. Brazing materials do not flow well
on oxidized or oily surfaces.
4. Clean the inside of all new tubing to remove oils and pipe
chips.
5. When brazing, sweep the tubing with dry nitrogen to prevent
the formation of oxides on the inside surfaces.
6. Complete any repair by replacing the liquid line drier in the
system, evacuate and charge.
BRAZING MATERIALS
I
MPORTANT NOTE:
Torch heat required to braze tubes of various
sizes is proportional to the size of the tube. Tubes of smaller size
require less heat to bring the tube to brazing temperature before
adding brazing alloy. Applying too much heat to any tube can melt
the tube. Service personnel must use the appropriate heat level
for the size of the tube being brazed.
NOTE:
The use of a heat shield when brazing is recommended to
avoid burning the serial plate or the finish on the unit. Heat trap
or wet rags should be used to protect heat sensitive components
such as service valves and TXV valves.
Copper to Copper Joints
- Sil-Fos used without flux (alloy of 15%
silver, 80% copper, and 5% phosphorous). Recommended heat
1400°F.
Copper to Steel Joints
- Silver Solder used without a flux (alloy of
30% silver, 38% copper, 32% zinc). Recommended heat - 1200°F.
S-101
LEAK TESTING (NITROGEN OR NITROGEN-
TRACED)
To avoid the risk of fire or explosion, never use
oxygen, high pressure air or flammable gases for leak
testing of a refrigeration system.
WARNING
To avoid possible explosion, the line from the
nitrogen cylinder must include a pressure regulator
and a pressure relief valve. The pressure relief valve
must be set to open at no more than 150 psig.
WARNING
Pressure test the system using dry nitrogen and soapy water to
locate leaks. If you wish to use a leak detector, charge the system
to 10 psi using the appropriate refrigerant then use nitrogen to
finish charging the system to working pressure, then apply the
detector to suspect areas. If leaks are found, repair them. After
repair, repeat the pressure test. If no leaks exist, proceed to sys-
tem evacuation.
S-102
EVACUATION
WARNING
REFRIGERANT UNDER PRESSURE!
Failure to follow proper procedures may cause
property damage, personal injury or death.
IMPORTANT NOTE:
Because of the potential damage to compres-
sors, do not allow suction pressure at service valve to drop below 5
PSIG when pumping unit system down for repair. Outdoor section,
depending on line set length and amount of charge in system, may
not be able to hold the entire system charge.
This is the most important part of the entire service procedure.
The life and efficiency of the equipment is dependent upon the
thoroughness exercised by the serviceman when evacuating air
(non-condensables) and moisture from the system.
Air in a system causes high condensing temperature and pres-
sure, resulting in increased power input and reduced performance.
Moisture chemically reacts with the refrigerant oil to form corro-
sive acids. These acids attack motor windings and parts, caus-
ing breakdown.
The equipment required to thoroughly evacuate the system is a
high vacuum pump, capable of producing a vacuum equivalent
to 25 microns absolute and a thermocouple vacuum gauge to
give a true reading of the vacuum in the system
NOTE:
Never use the system compressor as a vacuum pump or
run when under a high vacuum. Motor damage could occur.
Do not front seat the service valve(s) with the
compressor open, with the suction line of the
compressor closed or severely restricted.
1. Connect the vacuum pump, vacuum tight manifold set with
high vacuum hoses, thermocouple vacuum gauge and charg-
ing cylinder as shown.
2. Start the vacuum pump and open the shut off valve to the high
vacuum gauge manifold only. After the compound gauge (low
side) has dropped to approximately 29 inches of vacuum,
open the valve to the vacuum thermocouple gauge. See that
the vacuum pump will blank-off to a maximum of 25 microns.
A high vacuum pump can only produce a good vacuum if its
oil is non-contaminated.