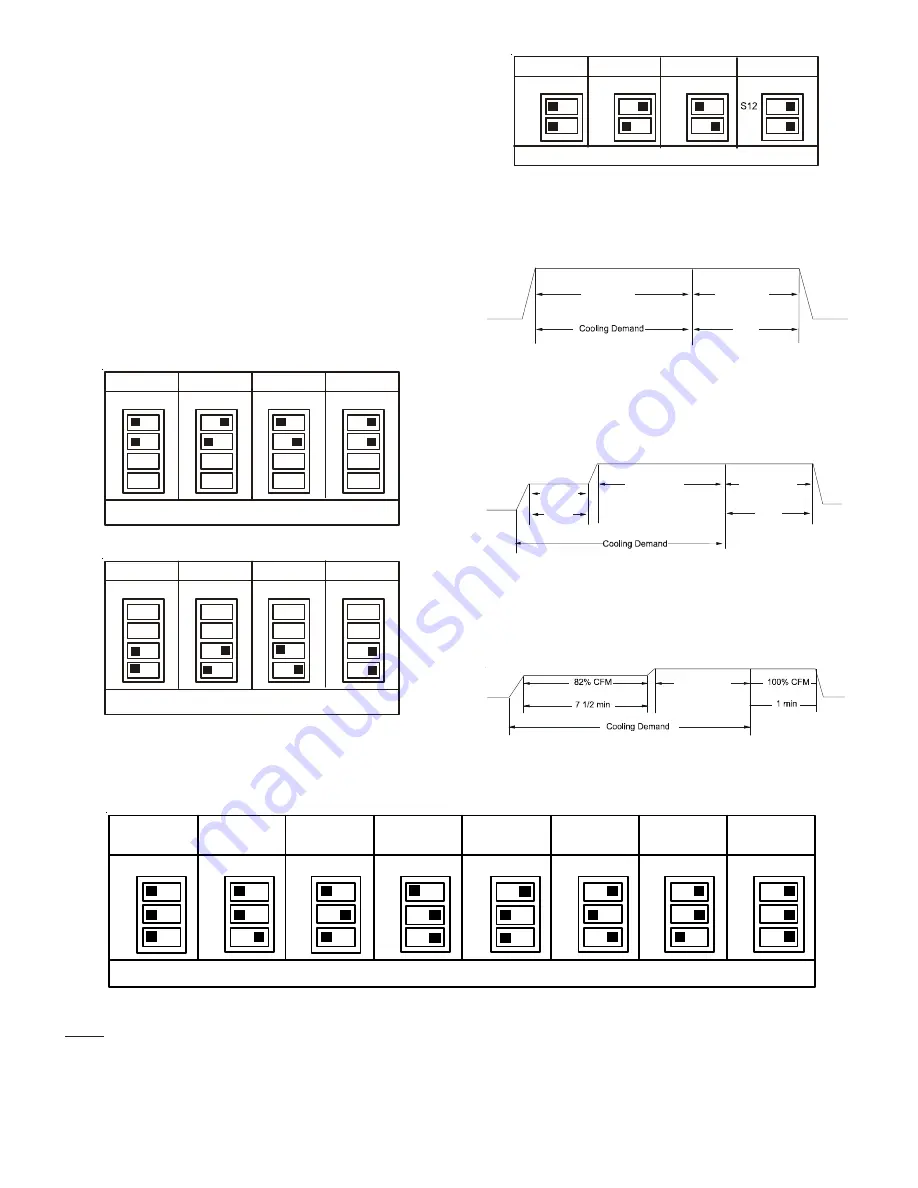
15
12
13
12
13
12
13
12
13
OFF
OFF
OFF
OFF
ON
ON
ON
ON
25%
50%*
Fan Only Selection (*indicates factory setting)
75%
100%
S12
S13
S12
S13
S12
S13
S13
OFF
OFF
OFF
OFF
ON
ON
ON
ON
Fan Only Selection (*indicates factory setting)
Figure 24
• Profile A provides only an OFF delay of one (1) minute at
100% of the cooling demand airflow.
OFF
100% CFM
100% CFM
1 min
OFF
Figure 26
• Profile B ramps up to full cooling demand airflow by first
stepping up to 50% of the full demand for 30 seconds. The
motor then ramps to 100% of the required airflow. A one
(1) minute OFF delay at 100% of the cooling airflow.
50% CFM
1/2 min
100% CFM
100% CFM
1 min
OFF
OFF
Figure 27
• Profile C ramps up to 82% of the full cooling demand air-
flow and operates there for approximately 7 1/2 minutes.
The motor then steps up to the full demand airflow. Profile
C also has a one (1) minute 100% OFF delay.
100% CFM
OFF
OFF
Figure 28
5. Continuous fan speeds that provide 25, 50, 75, and 100% of
the air handler’s maximum airflow capability are selectable
via dip switches S12 and S13.
If the air handler’s maximum airflow capability is 2000 CFM
and 25% continuous fan speed is selected, the continuous
fan speed will be 0.25 x 2000 CFM = 500 CFM.
6. The multi-circulator blower also offers several custom ON/
OFF ramping profiles. These profiles may be used to enhance
cooling performance and increase comfort level. The ramp-
ing profiles are selected using DIP switches 5 and 6. Refer to
the following
Dip Switches - Cooling Airflow Ramping Pro-
files
figure for switch positions and their corresponding taps.
Refer to the bullet points below for a description of each
ramping profile. Verify profile selection by counting the
green CFM LED blinks and timing each step of the ramping
profile.
S1
S2
S1
S2
S1
S2
S1
S2
OFF
OFF
OFF
OFF
ON
ON
ON
ON
Tap A
Tap B
Cooling Airflow Speed Tap (*indicates factory setting)
Tap C
Tap D*
Figure 22
S3
S4
OFF
OFF
OFF
OFF
ON
ON
ON
ON
+5%
-5%
Airflow Adjust Taps (*indicates factory setting)
+10%
-10%
S3
S4
S3
S4
S3
S4
Dip Switches -
Cooling Airflow and Airflow Adjust Taps
Figure 23
NOTE:
Upon start up in communicating mode the
circuit board may display an “Ec” error. This is an indication that the dip switches
on the control board need to be configured in accordance with the Electric Heating Airflow Table. Configuring the dip switches
and resetting power to the unit will clear the error code.
Within the thermostat user menu, CTK0* communicating thermostat will display 20 kW for OFF-OFF-ON dip switch selection and
21 kW for OFF-OFF-OFF dip switch selection.
S9
S10
OFF
OFF
OFF
OFF
ON
ON
ON
ON
21 kW* or
25 kW*
19 kW or
20 kW
Electric Heating Airflow (*indicates factory setting)
15 kW
10 kW
OFF
OFF
OFF
OFF
ON
ON
ON
ON
8 kW
6 kW
5 kW
3 kW
S11
S9
S10
S11
S9
S10
S11
S9
S10
S11
S9
S10
S11
S9
S10
S11
S9
S10
S11
S9
S10
S11
Figure 25