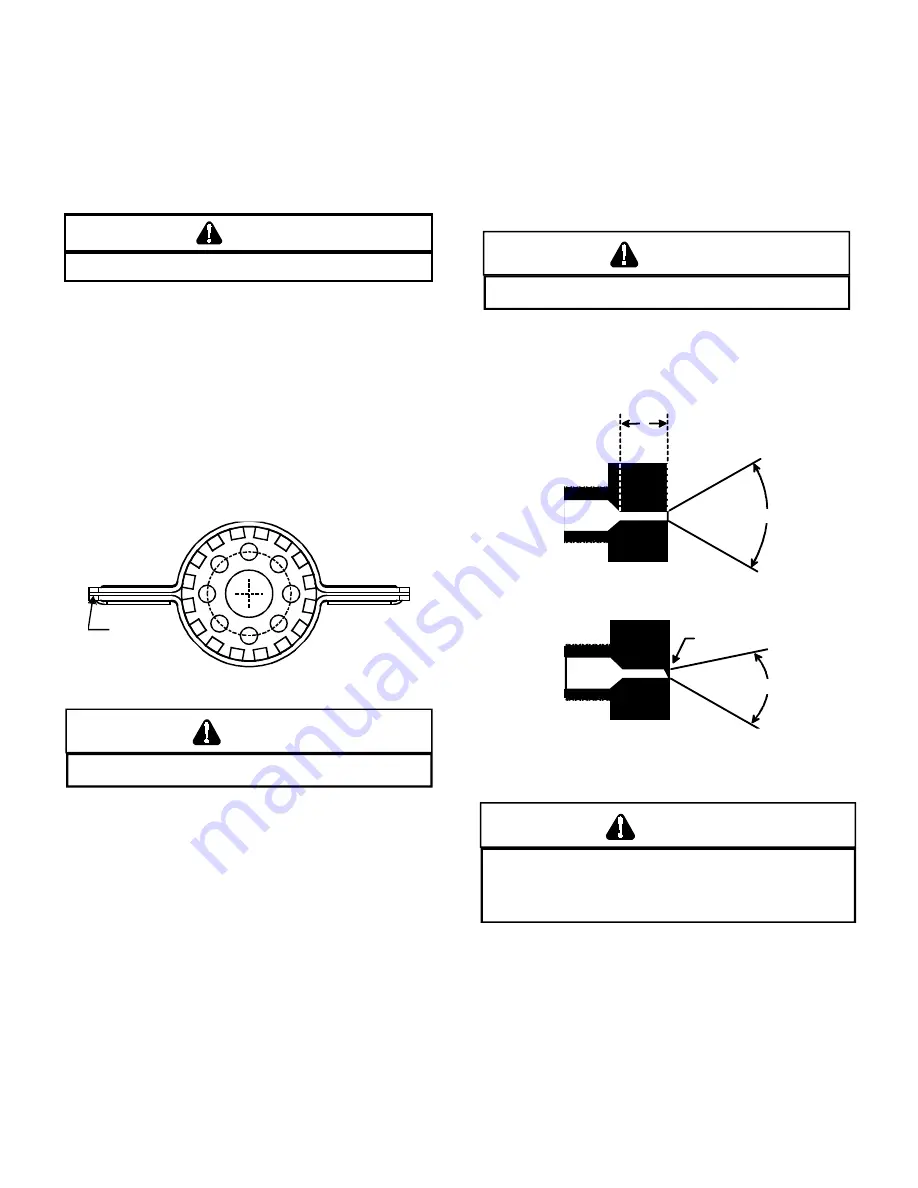
SERVICING
49
S-304 CHECKING GAS VALVE (Redundant)
A combination redundant operator type gas valve which
provides all manual and automatic control functions required
for gas fired heating equipment is used.
The valve provides control of main burner gas flow, pressure
regulation, and 100 percent safety shut-off.
WARNING
D
ISCONNECT
ALL
POWER BEFORE SERVICING
Single stage gas valves should be tested on the furnance
with 24 VAC connected to the gas valve and manometers
reading supply line and manifold pressures.
S-305 CHECKING MAIN BURNERS
The main burners are used to provide complete combustion
of various fuels in a limited space, and transfer this heat of
the burning process to the heat exchanger.
Proper ignition, combustion, and extinction are primarily due
to burner design, orifice sizing, gas pressure, primary and
secondary air, vent and proper seating of burners.
.023" - .027"
Beckett Burner
WARNING
D
ISCONNECT
ALL
G
AS AND
E
LECTRICAL
P
OWER
S
UPPLY.
In checking main burners, look for signs of rust, oversized
and undersized carry over ports restricted with foreign ma-
terial, etc, refer to previous drawing. Burner cross-over slots
must not be altered in size.
S-306 CHECKING ORIFICES
A predetermined fixed gas orifice is used in all of these fur
-
naces. That is an orifice which has a fixed bore and position
as shown in the following drawing.
No resizing should be attempted until all factors are taken
into consideration such as inlet and manifold gas pressure,
alignment, and positioning, specific gravity and BTU content
of the gas being consumed.
The only time resizing is required is when a reduction in
firing rate is required for an increase in altitude.
Orifices should be treated with care in order to prevent dam
-
age. They should be removed and installed with a box-end
wrench in order to prevent distortion. In no instance should
an orifice be peened over and redrilled. This will change
the angle or deflection of the vacuum effect or entraining
of primary air, which will make it difficult to adjust the flame
properly. This same problem can occur if an orifice spud of
a different length is substituted.
WARNING
D
ISCONNECT
ALL
G
AS AND
E
LECTRICAL
P
OWER
S
UPPLY.
1. Check orifice visually for distortion and/or burrs.
2. Check orifice size with orifice sizing drills.
3. If resizing is required, a new orifice of the same physical
size and angle with proper drill size opening should be
installed.
A
GAS
STREAM B
The length of Dimension "A" determines the angle of Gas
Stream "B".
DENT OR
BURR
GAS
STREAM B
A dent or burr will cause a severe deflection of the gas stream.
S-307 CHECKING GAS PRESSURE
Gas Supply Pressure Measurement
T
O PREVENT UNRELIABLE OPERATION OR EQUIPMENT DAMAGE, THE
INLET GAS SUPPLY PRESSURE MUST BE AS SPECIFIED ON THE UNIT
RATING PLATE WITH ALL OTHER HOUSEHOLD GAS FIRED APPLIANCES
OPERATING.
CAUTION
Gas inlet and manifold pressures should be checked and
adjusted in accordance to the type of fuel being consumed.
The line pressure supplied to the gas valve must be within
the range specified below. The supply pressure can be mea
-
sured at the gas valve inlet pressure tap or at a hose fitting
installed in the gas piping drip leg. The supply pressure must
be measured with the burners operating. To measure the gas
supply pressure, use the following procedure.