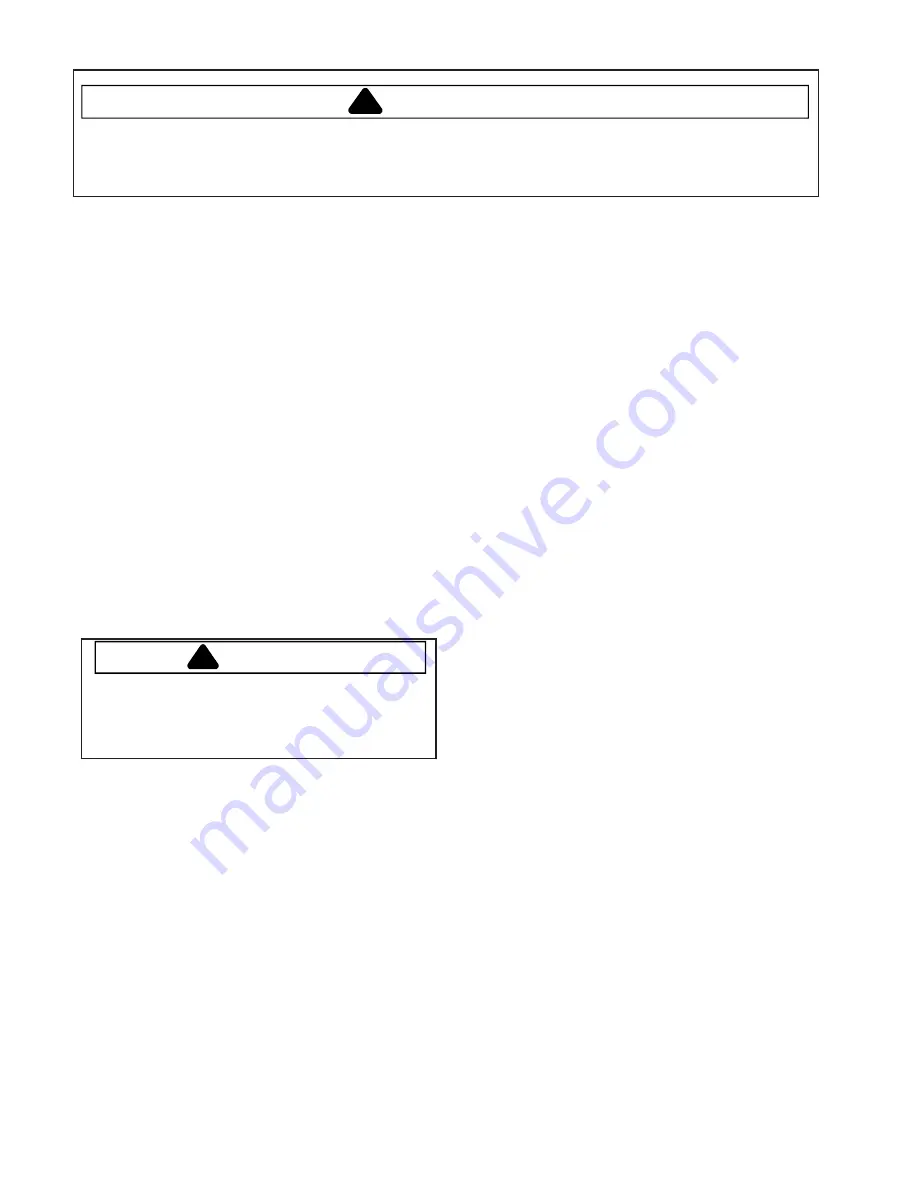
!
WARNING
To avoid risk of electrical shock, personal injury, or death, disconnect electrical power source to unit and
discharge capacitor through a 10,000 ohm resistor before attempting to service, unless test procedures
require power to be connected. Ensure all ground wires are connected before certifying unit as repaired
and/or operational.
16
16022379 Rev. 0
©2003 Maytag Appliances Company
NOTE
: Before opening any refrigeration system, EPA
regulations require refrigerant in system to
be captured for safe disposal.
Proper evacuation of sealed refrigeration system is
an important service procedure. Usable life and
operational efficiency of air conditioner greatly
depends upon how completely air, moisture and
other non-condensables are evacuated from sealed
system.
Air in sealed system causes high condensing
temperature and pressure, resulting in increased
power requirements and reduced performance.
Moisture in sealed system chemically reacts with
refrigerant and oil to form corrosive hydrofluoric and
hydrochloric acids. These acids attack motor
windings and parts, causing Restriction / Burnout
condition.
Equipment required to evacuate sealed system
includes:
•
High vacuum pump, capable of producing a
vacuum equivalent to 25 microns.
•
Thermocouple vacuum gauge capable of providing
true readings of vacuum in system.
CAUTION
!
To avoid damage to compressor motor, never
use air conditioner compressor as a vacuum
pump or run compressor when system is under
high vacuum.
To evacuate sealed refrigeration system:
1. Connect vacuum pump, vacuum tight manifold set
with high vacuum hoses, thermocouple vacuum
gauge and charging cylinder as shown in
illustration.
2. Connect low side line to compressor process tube.
3. Connect high side line to process tube of liquid line
strainer.
NOTE:
If a compression or flare fitting cannot be
attached to process tube(s) and still leave
room for a pinch-off, swage tube(s) and
braze on an additional length of tubing.
4. Start vacuum pump and open shut off valve to high
vacuum gauge manifold only.
5. After compound gauge (low side) drops to
approximately 29 inches gauge, open valve to
vacuum thermocouple gauge.
6. Ensure vacuum pump will blank-off to a maximum
of 25 microns.
NOTE
: A high vacuum pump can only produce a
good vacuum if oil in pump is not
contaminated.
7. If vacuum pump is working properly, close valve to
vacuum thermocouple gauge.
8. Open high and low side valves of high vacuum
manifold set. With valve on charging cylinder
closed, open manifold valve to cylinder.
9. Evacuate system to at least 29 inches gauge.
Open valve to thermocouple vacuum gauge.
10.Continue to evacuate to a maximum of 250
microns. Close valve to vacuum pump and watch
rate of rise:
•If vacuum does not rise above 1500 microns in
three minutes, system can be considered properly
evacuated.
•If thermocouple vacuum gauge continues to rise,
then levels off above 5000 microns, moisture and
non-condensables are still present. Re-evacuate.
•If gauge continues to rise above 5000 microns, a
leak is present. Locate, repair, and re-evacuate.
11. When system is properly evacuated, close valve
to thermocouple vacuum gauge and vacuum
pump. Shut off pump and prepare to charge
system.
Charging
NOTE
: Do not use captured or recycled refrigerant in
units. Captured or recycled refrigerant
voids all and/or compressor manufacturer’s
warranties.
NOTE
: Charge system with exact amount of
refrigerant. SeeTechnical Sheet or refer to
unit nameplate for correct refrigerant charge.
Inaccurately charged system will cause
future problems.
Testing Procedures
Summary of Contents for AAC051FRB
Page 24: ...2003 Maytag Appliances Company 16022379 Rev 0 A 1 Appendix A...
Page 43: ...19...