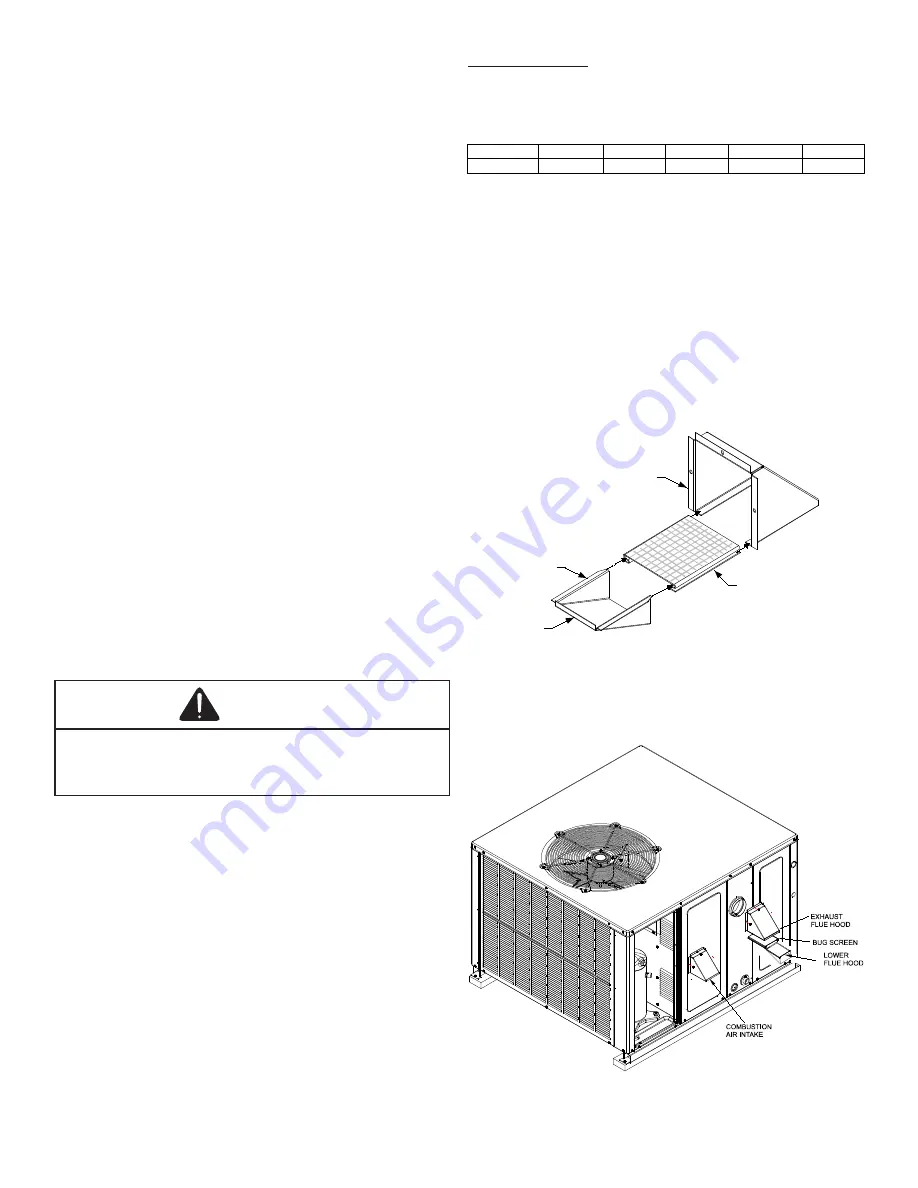
12
Ductwork
Duct systems and register sizes must be properly designed
for the C.F.M. and external static pressure rating of
the unit. Ductwork should be designed in accordance
with the recommended methods of Air Conditioning
Contractors of America Manual D (Residential) or Manual Q
(Commercial). All ductwork exposed to the outdoors must
include a weatherproof barrier and adequate insulation.
A duct system should be installed in accordance with
Standards of the National Board of Fire Underwriters for
the Installation of Air Conditioning, Warm Air Heating and
Ventilating Systems. Pamphlets No. 90A and 90B.
The supply duct from the unit through a wall may be
installed without clearance. However, minimum unit
clearances as shown in the appendix must be maintained.
The supply duct should be provided with an access panel
large enough to inspect the air chamber downstream of
the heat exchanger. A cover should be tightly attached to
prevent air leaks.
For duct flange dimensions on the unit refer to the Unit
Dimension illustration in the appendix.
For down-discharge applications, the ductwork should
be attached to the roof curb prior to installing the unit.
Ductwork dimensions are shown in the roof curb installation
manual.
If desired, supply and return duct connections to the unit
may be made with flexible connections to reduce possible
unit operating sound transmission.
Filters
CAUTION
To prevent property damage due to fire and loss of
equipment efficiency or equipment damage due to dust and
lint build-up on internal parts, never operate the unit
without an air filter installed in the return air system.
Even though a return air filter is not supplied with this unit,
there must be a means of filtering all return air. All units
may be externally filtered.
Refer to the unit filter size chart in the appendix for filter
size information.
Filters installed external to the unit should be sized in
accordance with their manufacturer recommendations. A
throwaway filter must be sized for a maximum face velocity
of 300 feet per minute.
Filter Installation
IMPORTANT NOTE: When installing a filter, the air
flow arrows on the filter must point toward the
circulator blower.
UNIT
2 Ton
2 1/2 Ton
3 Ton
3 1/2 & 4 Ton
5 Ton
Min. Filter Size (1)20 x 20 x 1 (1)20 x 25 x1 (1)25 x 25 x1 (2)20 x 20 x 1 2(20) x 25 x1
Filter Size Recommendations
VENTING
NOTE: Venting is self-contained. Do not modify or
block.
Installation - Flue Hood Exhaust
1.
Locate the flue hood assembly box in the unit.
2.
Slide screen over flanges on the lower flue hood.
3.
Slide screen and lower flue hood into hood.
4. Using the three screws provided, attach the hood
(with the opening facing down) over the flue exhaust
opening in the utility panel.
SCREEN
HOOD
LOWER
FLUE
HOOD
LIP
Installation - Combustion Air Intake Hood
1. Locate the second hood.
2. Using the three screws provided, attach the hood
(with the opening facing down) to the heat exchanger
access door.