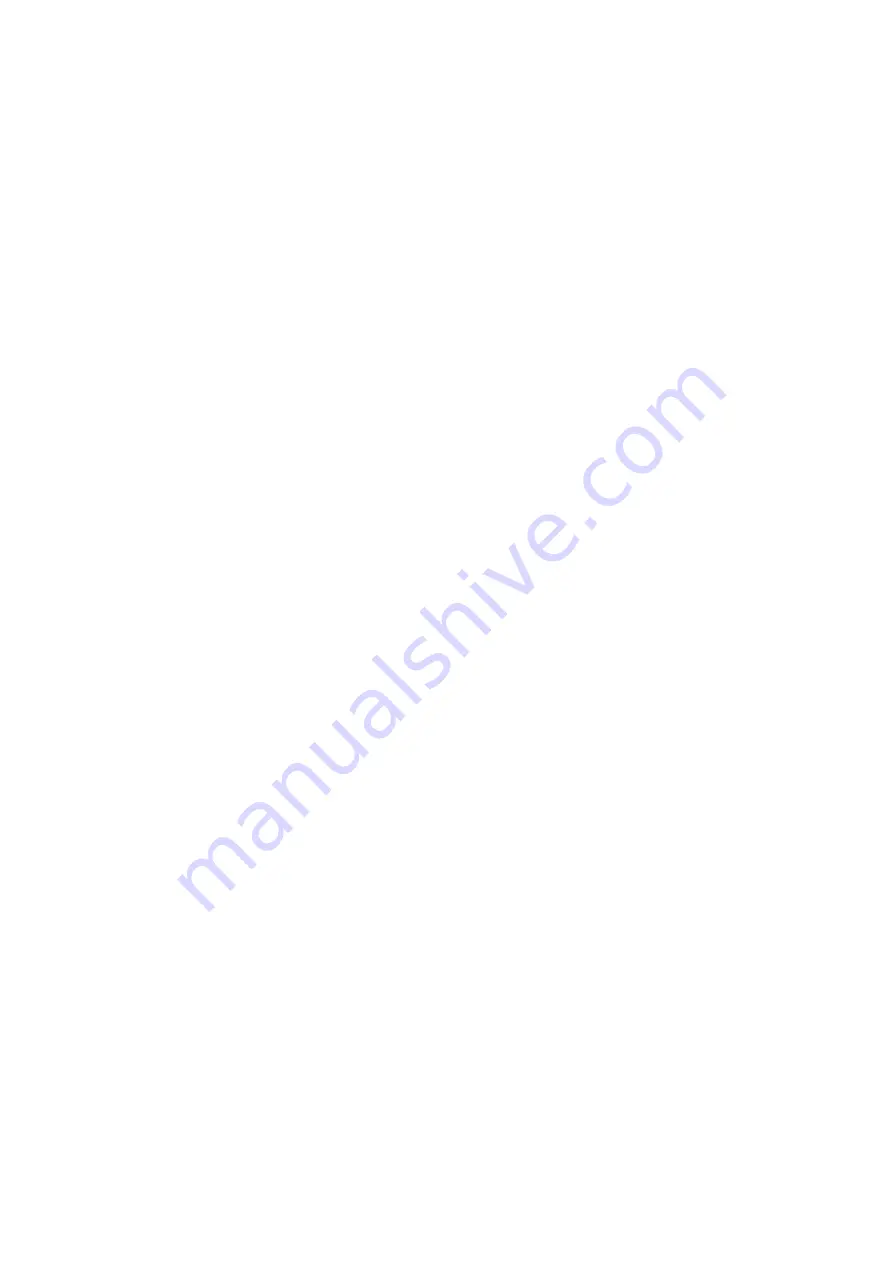
7.7
PI relay integral control low limit
Display:
A
x.
IL
Range:
0.0
to
100.0
Default Value:
100.0
The minimum limit can be used to reduce overshoot of the control setpoint when the control output
is being reduced i.e. falling below the setpoint. The low limit reduces the available output swing
by a percentage of the maximum output. Without a limit the integral output can be very large at
the time the setpoint is reached and a large overshoot of the will then result. Settings available are
from
0.0
to
100.0
(%). If the limit setting is too high then overshoot will result. If the setting
is too low then the integral output can be limited to such an extent that the setpoint cannot be
maintained.
Start with a low value such as
20.0
and increase or decrease the value until a satisfactory result
is obtained. The advantage of using separate low and high limits is that in many applications the
response is very one directional e.g. the system may respond very quickly to a heat input but may
cool down at a much slower rate. Separate high and low limit settings allow independent limiting
of the integral control swing below and above the setpoint so a smaller minimum limit can be set
to limit swings below the setpoint to compensate for the slower cooling time.
The minimum and maximum limits are used in conjunction with the output bias setting to maintain
the control process setpoint value. For example with a bias (
A
x.
bs
) set at 50%, minimum limit
set at 20% and a maximum limit of 30% the actual bias when the process is at the setpoint may
be anywhere between 30% and 80% i.e. Integral control is being used to alter the bias setting in
order to maintain the process at the setpoint. In this case the minimum term will allow the bias to
drop to a value between 50% and 30% in order to maintain the setpoint. The maximum term will
allow the bias point to rise to a value between 50% and 80% in order to maintain the setpoint.
7.8
PI relay control output bias
Display:
A
x.
bs
Range:
0.0
to
100.0
Default Value:
50.0
The control bias sets the ideal steady state output required once the setpoint is reached. Settings
are in % from
0.0
to
100.0
. When set at
0.0
the relay will be de-activated for the entire control
period when the measured input is at the setpoint (depending on proportional and integral gain
settings). If set at
50.0
then the relay operation frequency will on for 50% and off for 50% of the
duty cycle time when the measured input is at the setpoint. If set at
100.0
then the relay will
activated for the whole time whist the measured input is at the setpoint.
7.9
PI relay control cycle period
Display:
A
x.
dc
Range:
0
to
250
Default Value:
10
Displays and sets the control period cycle from
0
to
250
seconds. The control period sets the
total time for each on/off cycle. This time should be set as long as possible to reduce wear of the
RM4IVMAN-2.1-0
43 of
Summary of Contents for RM4-IV
Page 8: ...8 of 49 RM4IVMAN 2 1 0...
Page 10: ...10 of 49 RM4IVMAN 2 1 0...