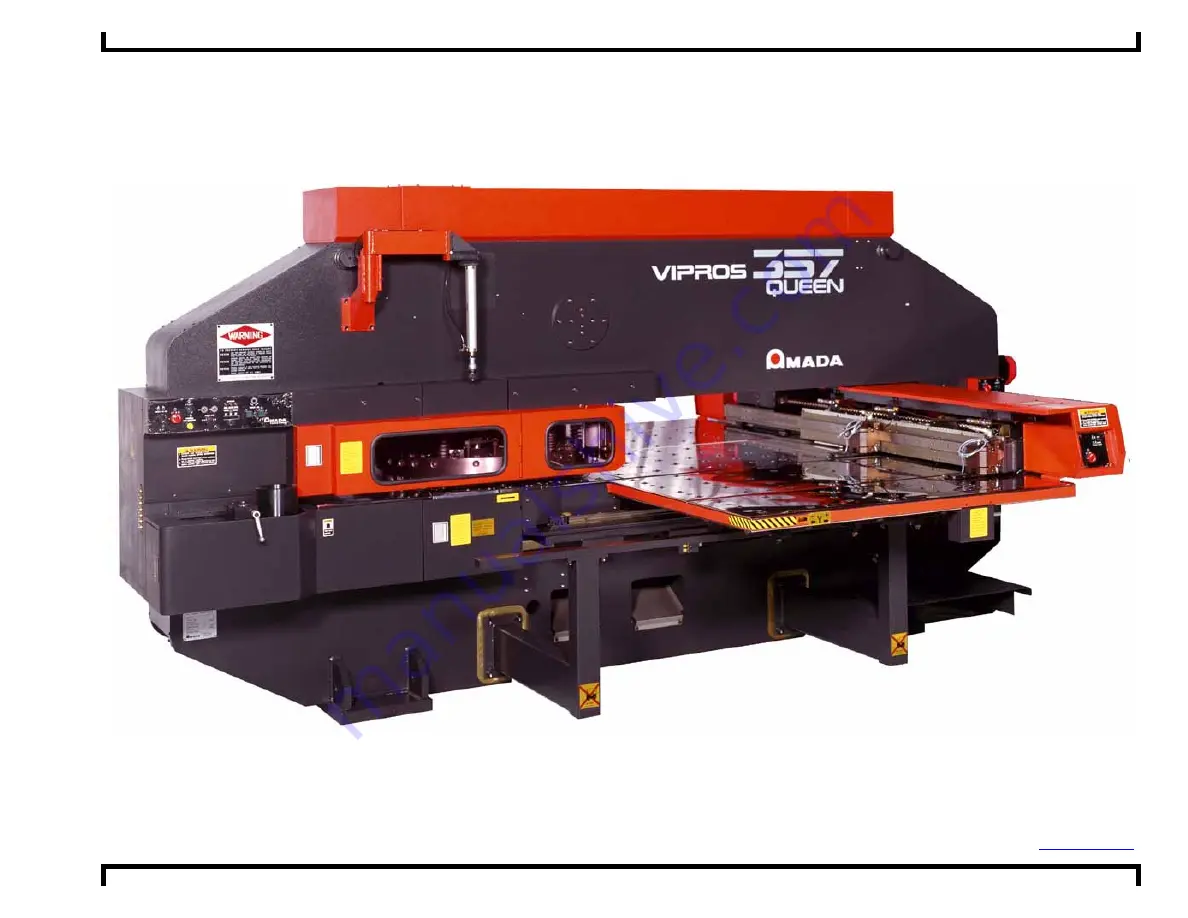
Vipros 357 Queen with Fanuc 18PC User Pre-installation Guide
©Amada America, Inc.
Print Date 01/24/2001 Revision 4.0
This document available on the World Wide Web at http://www.amada.com
Page 1 of 37
Vipros 357 Queen with Fanuc 18PC
User Pre-installation Guide
Amada America Inc.
7025 Firestone Blvd.
Buena Park CA. 90621
Phone: (714) 739 2111
Fax.: (714) 739 4099