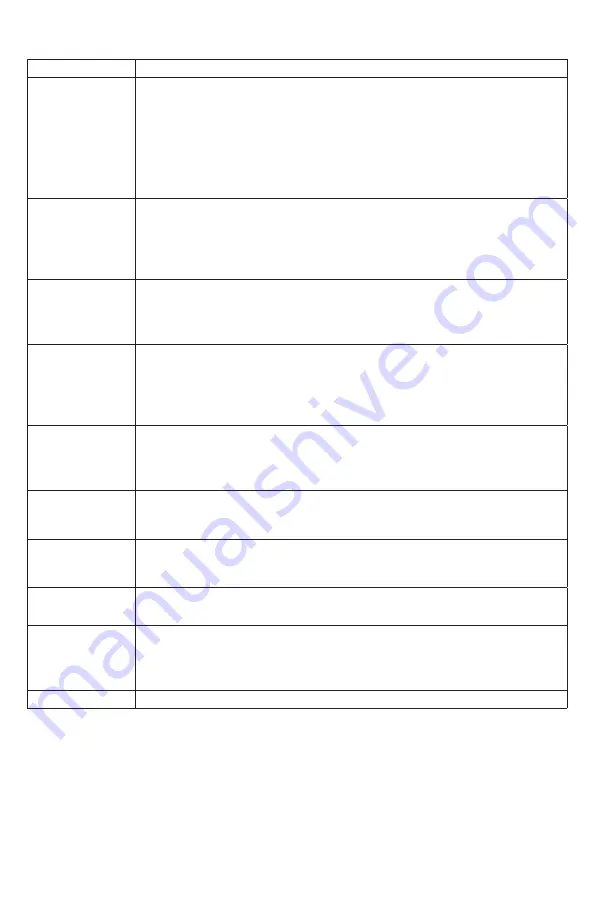
- 8 -
AL1042ULADA / R1042ULADA Installation Guide
Terminal Identification Table:
AL842LGK Logic Board
Terminal Legend
Function/Description
– IN1 +
– IN2 +
(Supervised)
These terminals connect to the 24VDC FACP notification appliance circuit outputs. (Class
A or Class B) Input trigger voltage is 8-33VDC @ 6.5mA min. Terminal polarity is shown
in alarm condition. During an alarm condition these inputs will cause the selected outputs
chosen to drive notification appliances. The designated outputs are set by output switches
[OUT1 through OUT4]
(Output Programming Selection Table, pg. 5).
A trouble condition on
an output loop will cause the corresponding input to trip the FACP by opening the FACP
loop. An alarm condition will always override trouble to drive notification appliances. Rated
12V 6.5mA, 24V 6.5mA.
– RET1 +
– RET2 +
(Supervised)
For Class A hookups these terminal pairs return to FACP NAC1 and/or NAC2.
For Class B hookups the FACP EOL resistor from the NAC1 and/or NAC2 outputs are
terminated at these terminals. Optionally, other notification appliances or additional signaling
circuit power supplies may be connected to these terminals.
If this option is chosen, the EOL resistor must be terminated at the last device.
NC “DRY1” C
NC “DRY2” C
(Dry input trigger)
An open across these inputs, will cause the selected outputs chosen to drive notification
appliances. The designated outputs are set by output switches [OUT1 through OUT4]
(Output Programming Selection Table, pg. 5).
Note these inputs are unidirectional and
will not report a trouble condition to the FACP.
– OUT1 +
– OUT2 +
– OUT3 +
– OUT4 +
(Supervised)
Notification appliances are connected to these regulated outputs
(see Application Guide
pg. 2-4).
Each power-limited output will supply 2.5A. Total supply current is 10A
(see
note below).
Outputs are controlled by designated Input 1 [IN1] or Input 2 [IN2]
(Output
Programming Selection Table, pg. 5).
Maximum line loss or voltage drop (tested with 2.5V).
– Loop 1 +
– Loop 2 +
– Loop 3 +
– Loop 4 +
Used for Class A hook-ups to terminate loops originating on
[OUT1], [OUT2], [OUT3], and [OUT4] respectively.
C “FAULT” NC
(Common
trouble input)
An open circuit across this pair of terminals will cause [INP1 and INP2] LEDs
to simultaneously signal a trouble condition back to the FACP. Typically used
to report AC or BAT Fail.
(Fig. 8b, pg. 11).
NC, C, NO
(Common
trouble output)
These are dry contact trouble outputs that report any general loop/system trouble
conditions. Typically used to trigger a digital communicator or other reporting devices.
Form “C” contact 1A / 28VDC 0.35 Power Factor
(Fig. 8, pg. 11)
.
– AUX1 +
This separate 1A max. auxiliary Special Application Power output circuit is disconnected
from load during AC power failure. See attached list of devices
(Appendix A, pgs. 14-17)
.
– AUX2 +
This separate auxiliary special application output supplies up to 1A during stand-by and
alarm condition. Since this output is not disconnected from its load during AC power
failure use the
Battery Calculation Worksheet, pg. 12
to determine battery size and/or
allowable stand-by and alarm current.
+ DC –
24VDC from power supply.
Note: Unit is equipped with two (2) 1A max. auxiliary outputs: “AUX1” will automatically disconnect when
AC is lost. “AUX2” will remain battery backed up during power outage. For loads connected to “AUX2”
please, refer to Battery Stand-by Specifications, pg. 3 for ratings. When loads are connected to the
“AUX1” and or “AUX2” outputs during alarm condition, the remaining outputs may not exceed 10A total
alarm current. Example: AUX1 = 1A, AUX2 = 1A, outputs up to 8A.
To reset the memory depress the reset button located on the AL842LGK logic board
(Fig. 8c, pg. 11)
.
The LED(s) will extinguish.
Note:
When indicating circuits have restored, trouble memory reset is not required for normal operation.