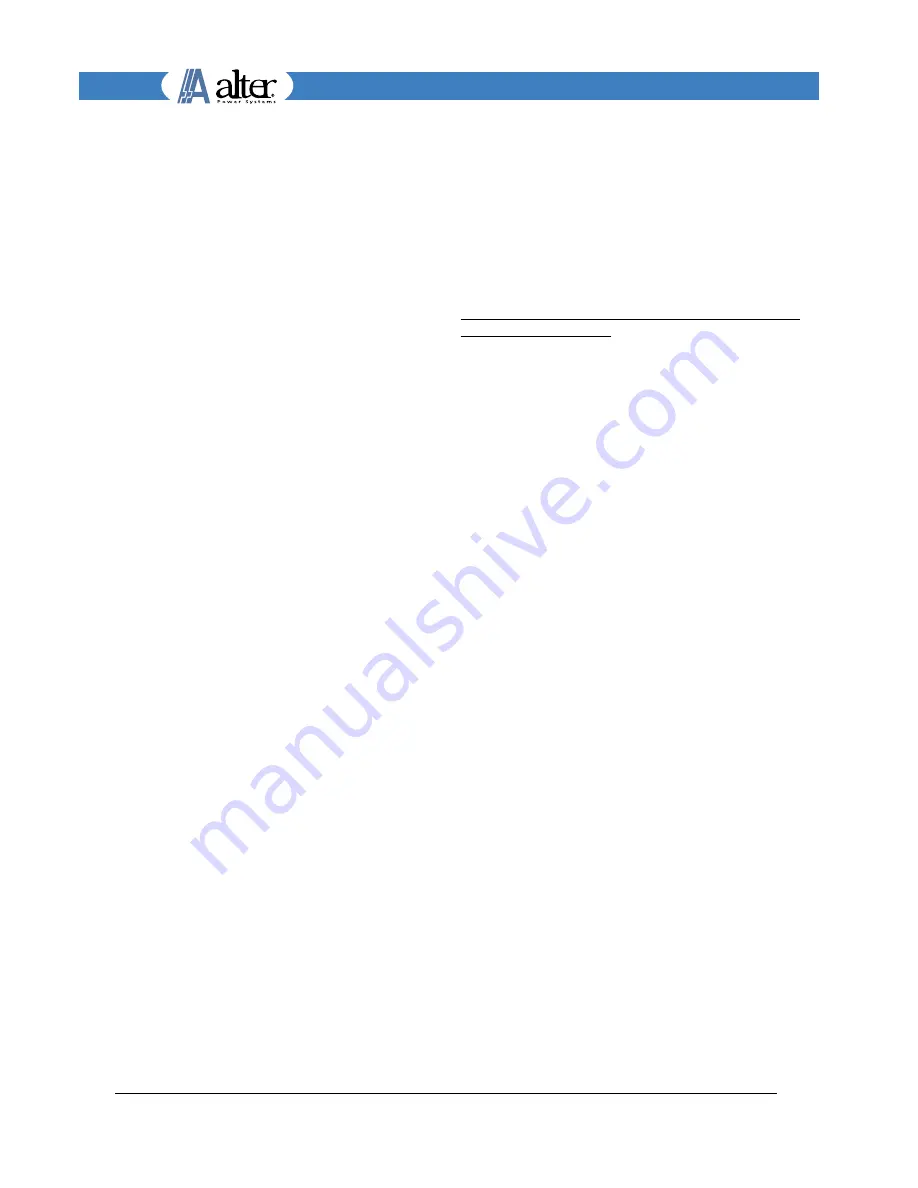
page 8
of 29
File: SM1150_r5eng - February 2007 - Technical note: SM1150
SM 1150
File: SM1150_r5eng - February 2007 - Technical note: SM 1150
page 9
of 29
SM 1150
III) The main supply, 3 x 208V or 3 x400V must be provided
through connector #1: connect phases according to schematic
at page 20, the connector’s pins can house wires with gauge up
to 4 mm².
IV) The connector #2, with 14 pins, brings the head’s signals
to the equipment. Use wires with max gauge of 1.5 mm², refer
to wiring diagram at page 21.
V) The connector #3 is the
high voltage output
and must be
connected to magnetron’s cathode, usually marked with the
symbol “FA” on the magnetron’s teminal. The voltage value is
near 5 kV .Use a proper insulated cable with working voltage
>8 kVdc and minimum gauge of 0.25 mm²; protect the wire
with sheating (armoured if appropriate).
Assemble the wire into plug according to professional rules.
The reliability of the equipment starts from the h.v. connec-
tions.
ALTER may supply the HV cable with lenght on request.
VI) The connector #4 provides the power supply for the
filament transformer (usually located near the magnetron), the
magnetron fan and a warning lamp. Use wires wih max gauge
1.5 mm². Refer to wiring diagram at page 21;
VII) The “D” type female connector #5 has 25 pins and brings
the I/O signals to the equipment. We suggest to use a shielded
ribbon cable. Refer to wiring diagram at page 22.
VIII) The “D” type male connector # 6 has 9 pins and is the
RS485 serial port on the standard version of the equipment. It
will be used fo future implementation of a field-bus (like the
CANbus).
IX) The “D” type female connector RS232 has 9 pins and it’s
a standard serial port, useful to allow upgrade of the software
from a PC. Look the pin-out at pg 23.
X) The user must provide external cut-off device, to protect the
SM1150 from short-citcuit and thermal runaway; this external
protection device must allow to switch-off the main line for
maintenance operations.
XI) The external circuit breaker must be a 3-poles breaker and
must comply the norm EN61010-1.
XII) The external circuit breaker must be in close proximity of
the equipment and within easy reach of the operator.
XIII) The external circuit breaker must be marked as the
disconnecting device for the SM1150.
XIV) The connector #1 must never be used as a switch-off
device.
Failure to comply with these instructions may involve con-
siderable risks for the staff responsible for checking and
using the equipment, as well as the risk of general malfunc-
tions of the equipment itself.
Equipment operation
Power-up procedure
Before power-up the equipment you must be sure to have pro-
perly connected (look at the chapter “Wiring Instruction” for
any doubt), then set the front panel breaker in “ON” position,
marked with “1”; to switch-OFF set it to “0”.
Once set to OFF (position “zero”) wait at least five seconds
before setting it ON again.
This rule must be valid even in case the power is given by an
external contactor (and the panel breaker has always left in ON
state): the OFF state, between two consecutive ON state, must
last five seconds minimum.
At power on the unit enters into “POWER-ON” state for few
seconds to performs some controls, then goes immediately
into “STAND-BY” and here stays until the “filament heating”
command is switched ON.
It’s also possible to enable permanently the “filament heating”
command: in this case the SM1150 performs the filament
heating immediately after the “POWER-ON” state, but only in
absence of alarms.
At the end of the heating cycle the unit enters in “READY”
mode: the power supply may power the magnetron, which
generates microwave, only when it will receive the enabling
command.
Any tipes of alarms force the unit to exits from “READY”
state and enters in “ALARM” state.
In absence of alarms the power supply may be left in “Ready”
continuously: when it receives the enabling command (ON) it
enters into “RF-ON” state and generates output power, when
the enabling command is removed (OFF) the unit comes back
to “READY” state.
Summary of Contents for SM1150
Page 19: ...page 18 of 29 File SM1150_r5eng February 2007 Technical note SM1150 SM 1150 ...
Page 21: ...page 20 of 29 File SM1150_r5eng February 2007 Technical note SM1150 SM 1150 Pin out of conn 1 ...
Page 23: ...page 22 of 29 File SM1150_r5eng February 2007 Technical note SM1150 SM 1150 Pin out of conn 5 ...